-
- News
- Books
Featured Books
- pcb007 Magazine
Latest Issues
Current IssueIt's Show Time!
In this month’s issue of PCB007 Magazine we reimagine the possibilities featuring stories all about IPC APEX EXPO 2025—covering what to look forward to, and what you don’t want to miss.
Fueling the Workforce Pipeline
We take a hard look at fueling the workforce pipeline, specifically at the early introduction of manufacturing concepts and business to young people in this issue of PCB007 Magazine.
Inner Layer Precision & Yields
In this issue, we examine the critical nature of building precisions into your inner layers and assessing their pass/fail status as early as possible. Whether it’s using automation to cut down on handling issues, identifying defects earlier, or replacing an old line...
- Articles
- Columns
Search Console
- Links
- Media kit
||| MENU - pcb007 Magazine
Overview of Soldering Systems With Vacuum
December 18, 2024 | Dr. Paul Wild, Rehm Thermal Systems GmbHEstimated reading time: 1 minute
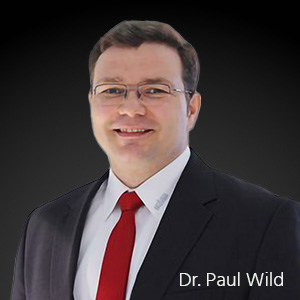
When soldering electronic assemblies, the focus of the vacuum application is on the removal of volatile substances from the solder joints and the associated reduction of pore formation. Particularly in the thermal management of power electronics components, pores can cause so-called hotspots with higher temperatures due to their poor heat conduction. These hotspots can lead to overheating of the components on the one hand and to thermally induced destruction of the solder structure on the other. Vacuum soldering is used in the production of assemblies in the field of power electronics (e.g., inverters for electric cars and renewable energy sources).
Figure 1 shows various SMD components after soldering with and without vacuum. A comparison shows that with a vacuum of 10 mbar, both the number of pores and the pore area can be drastically minimized. In the case of flat solder joints, such as QFNs or Si chips, a low proportion of pores results in better thermal performance as well as less tilting of the component.
Figure 1: X-ray images of various SMD components after soldering without vacuum and with 10 mbar vacuum.
In addition to temperature profiling, the negative pressure in the vacuum chamber and the duration of the negative pressure are also set during vacuum soldering. Figure 2 shows the influence of these parameters on the proportion of pore area in the thermal pad of a QFN64 component.
Figure 2: X-ray images of the QFN64 solder joint after soldering without vacuum and after soldering at different vacuum levels and different holding times.
Previous experience from industry and research has led to the essential realization that pore formation depends on many factors and that a sustainable reduction of pores in the solder joints can only be achieved with the help of a vacuum process. A vacuum of 150 mbar can already reduce the proportion of pores from, for example, 40% to less than 10%. If very low void ratios (< 5%) are to be achieved, other parameters, such as the surface finish, the solder paste type, or the design of the pads, must also be considered. In addition to the primary goal of reducing porosity, vacuum soldering offers other advantages that vary depending on the soldering system. A comparison of the contact, condensation and convection soldering processes is presented below.
To continue reading this article, which originally published in the December 2024 edition of SMT007 Magazine, click here.
Suggested Items
IonQ Announces Innovations in Compact, Room-Temperature Quantum Computing through XHV Technology
02/21/2025 | BUSINESS WIREIonQ, a leader in the quantum computing and networking industries, announced the completion of its next-generation ion trap vacuum package prototype intended to realize smaller, more compact, room temperature quantum systems.
Rehm Thermal Systems Brings Pioneering Manufacturing Technologies to productronica China 2025
02/11/2025 | Rehm Thermal SystemsRehm Thermal Systems will be presenting its further developments in areas such as convection soldering under vacuum, condensation soldering, coating and dispensing in Hall E4 of the Shanghai New International Expo Centre from 26 to 28 March.
SIA Applauds CHIPS Act Incentives for Infinera, Corning, Edwards Vacuum, and GlobalFoundries
01/20/2025 | SIAThe Semiconductor Industry Association (SIA) today released the following statement from SIA President and CEO John Neuffer commending a series of CHIPS and Science Act agreements announced by the U.S. Department of Commerce.
Altus Highlights Heller Industries Advances in Void Reduction Under 1%
01/06/2025 | Altus GroupAltus Group, a leading distributor of capital equipment in the UK and Ireland, emphasises the importance of reducing voids in reflow soldering to improve manufacturing efficiency and product reliability
SMT007 Magazine Explores Soldering Technologies—December 2024
12/02/2024 | I-Connect007 Editorial TeamSoldering is the heartbeat of assembly, and new developments are taking place to match the rest of the innovation in electronics. There are tried-and-true technologies for soldering. But new challenges in packaging, materials, and sustainability may be putting this key step in flux.