-
-
News
News Highlights
- Books
Featured Books
- pcb007 Magazine
Latest Issues
Current IssueSales: From Pitch to PO
From the first cold call to finally receiving that first purchase order, the July PCB007 Magazine breaks down some critical parts of the sales stack. To up your sales game, read on!
The Hole Truth: Via Integrity in an HDI World
From the drilled hole to registration across multiple sequential lamination cycles, to the quality of your copper plating, via reliability in an HDI world is becoming an ever-greater challenge. This month we look at “The Hole Truth,” from creating the “perfect” via to how you can assure via quality and reliability, the first time, every time.
In Pursuit of Perfection: Defect Reduction
For bare PCB board fabrication, defect reduction is a critical aspect of a company's bottom line profitability. In this issue, we examine how imaging, etching, and plating processes can provide information and insight into reducing defects and increasing yields.
- Articles
- Columns
- Links
- Media kit
||| MENU - pcb007 Magazine
Book Excerpt: The Printed Circuit Assembler’s Guide to... Low-Temperature Soldering, Vol. 2, Chapter 5
December 23, 2024 | I-Connect007 Editorial TeamEstimated reading time: 1 minute
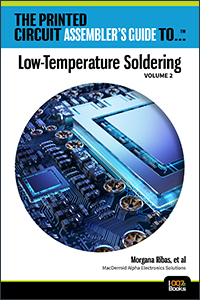
By Morgana Ribas, Pritha Choudhury, Ramakrishna H V, and Rahul Raut, MacDermid Alpha Electronics Solutions
Chapter 5: Unveiling a Total Solution for Soldering Through-hole Components Using a Low-temperature Alloy
Electronic assembly developers have a myriad of material and process choices to make, and low- temperature soldering is a process increasingly being considered for various assembly needs. LTS is attractive for a range of advantages:
- Potentially reduces material cost by enabling the use of lower cost PCBs and components due to lower processing temperature
- Promotes long-term reliability by reducing exposure to thermal excursion
- Long-term reliability is promoted by improvement in micro-via lifetime performance
- Lower energy cost
- Lower dynamic warpage in sensitive components
- Improved memory cell retention in high-density memory products such as LPDDR5
Use of the same low-temperature alloy for solder paste and solid solder provides a total solution for assembling a wider variety of electronic packages, including through-hole components.
The key benefits of using a low-temperature alloy for through-hole components are:
- Enables the use of low temperature in selective soldering
- Enables soldering processes with heat-sensitive substrates, components, or board materials
- Provides efficiencies in both energy and cost versus standard lead-free alloys
- Reduction of warpage up to 99% (component and board/substrate) vs. SAC305 processes
- Comparable mechanical performance with SAC305 under certain conditions
- Cost effective
Solder joints are an essential part of electronic devices that provide an electrical connection as well as a mechanical and thermal bond. Increased digitalization and greater connectivity are driving factors for miniaturization and more complex and integrated designs in electronics. With shrinking real estate on the PCBs, package sizes continue to shrink and the demand for reliability only increases. The requirement for solders with higher thermal and electrical reliability is the most important technology driver for designing new soldering materials. The ability of soldering at lower temperatures needs to be balanced with the thermal and mechanical reliability requirements for a specific application. The higher reflow temperature required for soldering a hybrid solder joint involving SAC BGA can potentially result in soldering defects such as non-wet opens, solder bridging, head on pillow, and non-contact opens in packages such as Package on Package (PoP) bottom and PoP memory. Low-temperature soldering is becoming a crucial technology, as it helps prevent defects caused by warpage in ultra-thin, high I/O CSP packages used in complex electronic devices.
Testimonial
"In a year when every marketing dollar mattered, I chose to keep I-Connect007 in our 2025 plan. Their commitment to high-quality, insightful content aligns with Koh Young’s values and helps readers navigate a changing industry. "
Brent Fischthal - Koh YoungSuggested Items
KOKI to Showcase Analytical Services and New HF1200 Solder Paste at SMTA Guadalajara 2025
07/31/2025 | KOKIKOKI, a global leader in advanced soldering materials and process optimization services, will exhibit at the SMTA Guadalajara Expo & Tech Forum, taking place September 17 & 18, 2025 at Expo Guadalajara, Salón Jalisco Halls D & E in Guadalajara, Mexico.
Weller Tools Supports Future Talent with Exclusive Donation to SMTA Michigan Student Soldering Competition
07/23/2025 | Weller ToolsWeller Tools, the industry leader in hand soldering solutions, is proud to announce its support of the upcoming SMTA Michigan Expo & Tech Forum by donating a limited-edition 80th Anniversary Black Soldering Set to the event’s student soldering competition.
Silicon Mountain Contract Services Enhances SMT Capabilities with New HELLER Reflow Oven
07/17/2025 | Silicon Mountain Contract ServicesSilicon Mountain Contract Services, a leading provider of custom electronics manufacturing solutions, is proud to announce a significant upgrade to its SMT production capability with the addition of a HELLER 2043 MK5 10‑zone reflow oven to its Nampa facility.
SHENMAO Strengthens Semiconductor Capabilities with Acquisition of PMTC
07/10/2025 | SHENMAOSHENMAO America, Inc. has announced the acquisition of Profound Material Technology Co., Ltd. (PMTC), a premier Taiwan-based manufacturer of high-performance solder balls for semiconductor packaging.
Hands-On Demos Now Available for Apollo Seiko’s EF and AF Selective Soldering Lines
06/30/2025 | Apollo SeikoApollo Seiko, a leading innovator in soldering technology, is excited to spotlight its expanded lineup of EF and AF Series Selective Soldering Systems, now available for live demonstrations in its newly dedicated demo room.