-
- News
- Books
Featured Books
- smt007 Magazine
Latest Issues
Current IssueMoving Forward With Confidence
In this issue, we focus on sales and quoting, workforce training, new IPC leadership in the U.S. and Canada, the effects of tariffs, CFX standards, and much more—all designed to provide perspective as you move through the cloud bank of today's shifting economic market.
Intelligent Test and Inspection
Are you ready to explore the cutting-edge advancements shaping the electronics manufacturing industry? The May 2025 issue of SMT007 Magazine is packed with insights, innovations, and expert perspectives that you won’t want to miss.
Do You Have X-ray Vision?
Has X-ray’s time finally come in electronics manufacturing? Join us in this issue of SMT007 Magazine, where we answer this question and others to bring more efficiency to your bottom line.
- Articles
- Columns
Search Console
- Links
- Media kit
||| MENU - smt007 Magazine
Estimated reading time: 4 minutes
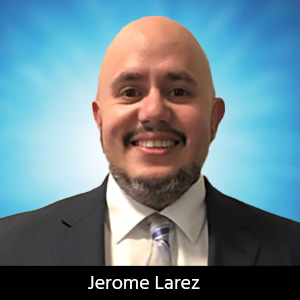
Global PCB Connections: The Next Wave of HDI PCBs– How Design Engineers Can Stay Ahead
High density interconnect (HDI) printed circuit boards have come a long way from their origins as a niche technology for miniaturized applications. Today, HDI PCBs are at the forefront of innovation, driven by an insatiable demand for faster, smaller, and more powerful electronic devices. As consumer electronics, 5G infrastructure, and AI-driven systems advance, design engineers must stay ahead of the curve to ensure their PCB designs meet evolving industry demands. In this article, we explore the next wave of HDI PCB technology, the challenges and opportunities it presents, and how engineers can leverage the latest advancements to maintain a competitive edge.
Why HDI Demand Is Growing
As Moore’s Law continues to push the boundaries of semiconductor technology, traditional PCB designs have struggled to keep pace with the miniaturization of integrated circuits. HDI technology allows for finer lines and spaces, multiple layers, and higher component densities, enabling cutting-edge applications in industries such as telecommunications, aerospace, medical devices, and consumer electronics. The push for smaller form factors, improved signal integrity, and lower power consumption further cements HDI PCBs as a critical technology for next-generation electronics.
How Microvias Enable Next-gen Designs
A defining feature of HDI PCBs is the use of microvias—small, laser-drilled vias that enable high-density routing. Unlike traditional through-hole vias, microvias reduce parasitic capacitance and inductance, improving signal integrity and overall performance. By employing stacked, staggered, or skip vias, design engineers can route traces more efficiently and create multilayered PCBs without significantly increasing board thickness. This is particularly beneficial for high-speed and RF applications, where maintaining signal integrity is crucial. As the industry increases circuit density, microvias become more prevalent in PCB designs.
Challenges of Routing in Ultra-dense Environments
While HDI technology offers numerous advantages, it also presents significant challenges, particularly in ultra-dense routing environments. Engineers must carefully balance trace width, spacing, and via placement to prevent signal integrity issues such as crosstalk and electromagnetic interference (EMI). Furthermore, power integrity considerations become more complex as current densities increase. Advanced design tools incorporating electromagnetic simulation and signal integrity analysis are essential for mitigating these challenges. Additionally, implementing a design-for-manufacturing (DFM) approach early in the design phase helps reduce potential fabrication issues, ensuring a more reliable final product.
HDI Applications in 5G, Wearables, and High-speed Computing
HDI technology is a game-changer in several key industries. The rollout of 5G networks demands PCBs with high-speed interconnects, low latency, and enhanced power efficiency—attributes that HDI PCBs provide. Wearable devices, from smartwatches to health monitoring sensors, rely on HDI to maintain compact and lightweight designs while incorporating advanced functionalities. In high-speed computing, HDI PCBs enable higher data transfer rates and improved thermal management, essential for AI-driven applications, cloud computing, and next-generation GPUs. As these industries push the envelope of technological innovation, HDI PCBs will remain indispensable.
Materials Used for HDI and Their Performance Trade-offs
Selecting the right materials for HDI PCBs is crucial to achieving optimal performance. Traditional FR-4 substrates are often insufficient for high-frequency applications because of their limited dielectric properties. Instead, high-performance laminates and polyimide-based materials are gaining traction. These materials offer lower signal loss, better thermal stability, and improved mechanical strength. However, they come at a higher cost and may present processing challenges. Design engineers must weigh these trade-offs based on application requirements, balancing performance, cost, and manufacturability.
Cost Considerations for Mass Production vs. Prototyping
The cost of manufacturing HDI PCBs varies between prototyping and mass production. Prototyping typically incurs higher costs because of limited production runs, extensive testing, and potential design iterations. However, in mass production, economies of scale help drive down per-unit costs. To optimize costs, engineers should consider design simplifications, such as reducing the number of microvia layers or using standard laminate materials when possible. Additionally, collaborating closely with manufacturers during the design phase can help streamline production and minimize waste.
Manufacturing Tolerances and the Impact on Yields
As feature sizes shrink, tighter tolerances are required to ensure reliable fabrication. Factors such as laser drilling precision, plating uniformity, and registration accuracy all influence the final product’s quality. Small deviations can lead to increased defect rates, reducing overall yields and driving up costs. To mitigate these risks, manufacturers are investing in advanced equipment, automation, and AI-driven quality control systems. Engineers should also work with fabricators with track records in HDI manufacturing to ensure consistent results.
Future Trends: AI-assisted HDI Design and Manufacturing
The future of HDI PCB design and manufacturing is being shaped by artificial intelligence (AI) and machine learning (ML). AI-driven design tools can optimize routing, predict signal integrity issues, and suggest material choices based on application needs. In manufacturing, AI-powered quality control systems analyze production data in real time and identify defects before they impact yield, also known as Industry 5.0. Additionally, generative design algorithms are being explored to create PCB layouts that maximize space and minimize electrical losses. As AI technology matures, engineers who embrace these tools will have a significant advantage in developing the next generation of HDI PCBs.
HDI PCBs are at the forefront of electronic innovation, enabling smaller, faster, and more efficient devices across multiple industries. From the evolution of microvia technology to the integration of AI in design and manufacturing, staying ahead in HDI PCB development requires a deep understanding of emerging trends and challenges. Design engineers with a forward-thinking approach, using cutting-edge tools and collaborating with experienced fabricators, are best suited to lead HDI advancements. By embracing these innovations, the industry can continue to push the boundaries of what’s possible in electronic design.
Jerome Larez is a field application engineer and director of technical sales with CEE PCB.
More Columns from Global PCB Connections
Global PCB Connections: Rigid-flex and Flexible PCBs—The Backbone of Modern ElectronicsGlobal PCB Connections: A Field Engineer’s Perspective on the Top 10 Trends to Watch
Global PCB Connections: How Technology Can Level the Playing Field
Global PCB Connections: The Future of HDI PCBs
Global PCB Connections: Following DFM Rules Leads to Better Boards
Global PCB Connections: A Technical Overview of Long-flex Printed Circuit Boards
Global PCB Connections: Mission Critical—Communication Between PCB Designers and Fabricators