-
- News
- Books
Featured Books
- smt007 Magazine
Latest Issues
Current IssueMoving Forward With Confidence
In this issue, we focus on sales and quoting, workforce training, new IPC leadership in the U.S. and Canada, the effects of tariffs, CFX standards, and much more—all designed to provide perspective as you move through the cloud bank of today's shifting economic market.
Intelligent Test and Inspection
Are you ready to explore the cutting-edge advancements shaping the electronics manufacturing industry? The May 2025 issue of SMT007 Magazine is packed with insights, innovations, and expert perspectives that you won’t want to miss.
Do You Have X-ray Vision?
Has X-ray’s time finally come in electronics manufacturing? Join us in this issue of SMT007 Magazine, where we answer this question and others to bring more efficiency to your bottom line.
- Articles
- Columns
- Links
- Media kit
||| MENU - smt007 Magazine
Estimated reading time: 4 minutes
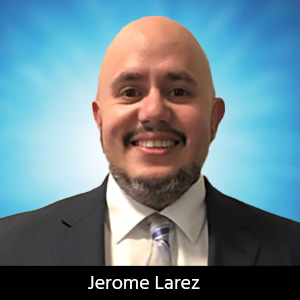
Global PCB Connections: Rigid-flex and Flexible PCBs—The Backbone of Modern Electronics
In the past decade, flex and rigid-flex PCB technology has become the fastest-growing market segment. As an increasing number of PCB companies develop the capabilities to fabricate this technology, PCB designers are becoming comfortable incorporating these designs into their products.
Designers were once reluctant to call out this technology because few shops could successfully fabricate these types of PCBs. This is no longer the case. The demand for flex and rigid-flex PCBs is growing and many PCB fabricators support it.
The demand for smaller, lighter, and more reliable electronic devices also continues to grow. At the heart of this revolution are flexible and rigid-flex PCBs, integral to modern electronic designs. These advanced circuit board solutions are indispensable in industries ranging from consumer wearables to medical devices and aerospace applications.
Flexible Printed Circuits (FPCs): Critical for Wearables and IoT
The rise of wearables and the Internet of Things (IoT) has pushed the boundaries of traditional electronics, requiring compact, lightweight, and highly adaptable circuit boards. FPCs provide:
- Enhanced form factor: Unlike rigid PCBs, FPCs can bend, twist, and fold while maintaining electrical connections. Medical and wearable applications leverage the benefits of these innovative FPC designs.
- Increased durability: FPCs can withstand repeated mechanical stresses, making them ideal for fitness trackers, smartwatches, and medical implants.
- Lightweight design: With the miniaturization of IoT devices, FPCs help reduce weight and bulk, improving portability and user comfort.
The Difference Between Flex, Rigid-flex, and Stretchable PCBs
Understanding the distinctions between different PCB types is critical in choosing the right solution for a given application:
- Flexible PCBs (FPCs): Made entirely of flexible substrates, these circuits can conform to various shapes, whether in dynamic or static bending applications.
- Rigid-flex PCBs: A hybrid of rigid and flexible materials, these boards offer structural integrity where needed while maintaining flexibility in other areas.
- Stretchable PCBs: A developing technology, stretchable PCBs use elastic materials that can expand and contract, ideal for bio-integrated devices and advanced wearable applications.
Key Design Rules for Durability and Reliability
To maximize the performance and lifespan of flexible and rigid-flex PCBs, engineers must adhere to specific design principles:
- Optimized bending radius: Avoiding sharp bends and maintaining appropriate bend radii prevents mechanical stress and cracking.
- Layer stacking considerations: Proper layer arrangement reduces electrical interference and enhances mechanical stability.
- Reinforcement strategies: Adding stiffeners or support structures in high-stress areas can extend durability.
- Trace routing best practices: Using curved traces instead of 90-degree angles minimizes stress points and signal integrity issues.
- Via placement: Avoiding plated vias in bend areas is a common design practice.
Material Selection: Polyimide vs. Liquid Crystal Polymer (LCP)
Material choice is vital in determining a PCB’s flexibility, thermal stability, and signal performance:
- Polyimide (PI): The most used flexible substrate due to its excellent thermal resistance, mechanical strength, and cost-effectiveness.
- Liquid crystal polymer (LCP): Offers superior moisture resistance, low dielectric constant, and high-frequency performance, making it ideal for RF and high-speed applications.
How Rigid-Flex Is Solving Miniaturization Challenges
Miniaturization is a primary driver of innovation across industries, and rigid-flex PCBs offer effective solutions:
- Elimination of connectors: By integrating flexible circuits within rigid boards, designers can remove bulky connectors, saving space and improving reliability.
- Reduced assembly complexity: Fewer interconnects and streamlined layouts simplify manufacturing and assembly processes.
- Compact multi-layered designs: Enable the stacking of multiple layers in a compact form without sacrificing performance.
EMI and Signal Integrity Considerations for Flex Circuits
With increased data speeds and wireless communication demands, mitigating EMI and ensuring signal integrity are critical challenges:
- Proper shielding: Implementing EMI shielding layers and ground planes reduces signal noise and crosstalk.
- Controlled impedance: Maintaining consistent impedance along traces enhances high-speed signal transmission.
- Minimized parasitic effects: Optimized routing and spacing prevent signal degradation and unwanted electromagnetic interactions.
Cost Vs. Performance: When to Choose Rigid-Flex Over Standard PCBs
While rigid-flex PCBs offer many advantages, they also come with a higher manufacturing cost. To determine when to invest in rigid-flex technology, consider:
- Complexity of the design: For intricate layouts requiring multiple interconnects, rigid-flex PCBs can reduce component counts and improve reliability.
- Environmental factors: Applications exposed to extreme conditions, such as aerospace or medical implants, benefit from robust, rigid-flex designs.
- Production volume: While expensive for low-volume fabrication, rigid-flex PCBs can lower overall costs in mass production by reducing assembly steps and material waste.
Emerging Applications: Space, Medical, and Automotive Innovations
The versatility of flexible and rigid-flex PCBs is unlocking new possibilities across multiple high-tech industries:
- Space exploration: Satellites, rovers, and space probes use lightweight, radiation-resistant flex circuits.
- Medical devices: Manufacturers use flexible PCBs in ultra-miniature biocompatible electronic devices, from pacemakers to wearable health monitors.
- Automotive electronics: Modern vehicles leverage flex and rigid-flex circuits for advanced driver-assistance systems (ADAS), in-dash displays, and sensor integrations.
The integration of flexible and rigid-flex PCBs has revolutionized modern electronics, providing versatility, durability, and performance. As miniaturization, IoT, and high-speed applications evolve, these PCB technologies will remain at the forefront of innovation and shape the next generation of electronic devices.
Jerome Larez is a field application engineer and director of technical sales with CEE PCB.
More Columns from Global PCB Connections
Global PCB Connections: Embedded Components—The Future of High-performance PCB DesignGlobal PCB Connections: The Next Wave of HDI PCBs– How Design Engineers Can Stay Ahead
Global PCB Connections: A Field Engineer’s Perspective on the Top 10 Trends to Watch
Global PCB Connections: How Technology Can Level the Playing Field
Global PCB Connections: The Future of HDI PCBs
Global PCB Connections: Following DFM Rules Leads to Better Boards
Global PCB Connections: A Technical Overview of Long-flex Printed Circuit Boards
Global PCB Connections: Mission Critical—Communication Between PCB Designers and Fabricators