Specially Developed for Laser Plastic Welding from LPKF
June 25, 2025 | LPKFEstimated reading time: 1 minute
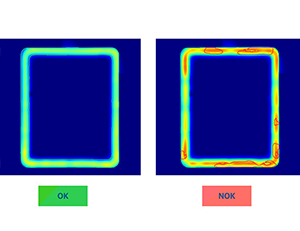
LPKF introduces TherMoPro, a thermographic analysis system specifically developed for laser plastic welding that transforms thermal data into concrete actionable insights. Through automated capture, evaluation, and interpretation of surface temperature patterns immediately after welding, the system provides unprecedented process transparency that correlates with product joining quality and long-term product stability. TherMoPro data enables welding process optimization to enhance component strength and long-term stability in a new dimension – completely non-destructively.
The system is designed for easy integration into existing production lines as a retrofit solution or as part of any new installation from the LPKF laser plastic welding product portfolio. Since thermographic analysis takes place directly after the welding process, usually cycle-time neutral, TherMoPro saves valuable space and time. Depending on the process, this inline approach can replace conventional quality control stations or reduce testing intervals for cost-intensive additional inspections, thus keeping production flow efficient – including full process transparency and traceability to every product ID.
"TherMoPro is far more than a standard thermal camera," explains Thomas Sontheimer, Senior Project Leader WeldingEquipment at LPKF. "Our solution approach offers real added value through the perfect synergy between specialized data acquisition and application-oriented analysis."
Developed in collaboration with experts specifically from the field of Automatic Optical Inspection (AOI), the system converts complex thermal data into more than 20 different quality parameters. This comprehensive analysis enables users to:
• Identify components that pass initial leak tests but would fail during temperature cycling tests
• Optimize processes for improved strength and reduced cycle times
• Monitor material property or process variations in real-time
• Achieve secure traceability with thermal data linked to each component ID
Benefits for markets with high quality requirements
For medical device manufacturers, the TherMoPro system provides the foundation for regulatory compliance, essential documentation requirements, and traceability while ensuring the long-term integrity of, for example, fluid-carrying components and sensitive enclosures. The ability to detect subtle thermal anomalies is particularly important for components with zero-defect tolerance.
Automotive suppliers benefit from TherMoPro's ability to monitor production variations in multi-cavity tools, ensuring consistent quality in high-volume production. As the industry increasingly incorporates recycled materials and flame retardants into plastic components, the system's ability to detect and compensate for varying material properties becomes crucial for maintaining quality standards while meeting sustainability goals.
Suggested Items
SMT007 Magazine July—What’s Your Competitive Sweet Spot?
07/01/2025 | I-Connect007 Editorial TeamAre you in a niche that’s growing or shrinking? Is it time to reassess and refocus? We spotlight companies thriving by redefining or reinforcing their niche—what are their insights? In the July 2025 issue of SMT007 Magazine, we spotlight companies thriving by redefining or reinforcing their niche and offer insights to help you evaluate your own.
Smarter Machines Use AOI to Transform PCB Inspections
06/30/2025 | Marcy LaRont, PCB007 MagazineAs automated optical inspection (AOI) evolves from traditional end-of-process inspections to proactive, in-line solutions, the integration of AI and machine learning is revolutionizing defect reduction and enhancing yields, marking a pivotal shift in how quality is managed in manufacturing.
Magnalytix and Foresite to Host Technical Webinar on SIR Testing and Functional Reliability
06/26/2025 | MAGNALYTIXMagnalytix, in collaboration with Foresite Inc., is pleased to announce an upcoming one-hour Webinar Workshop titled “Comparing SIR IPC B-52 to Umpire 41 Functional & SIR Test Method.” This session will be held on July 24, 2025, and is open to professionals in electronics manufacturing, reliability engineering, and process development seeking insights into new testing standards for climatic reliability.
The Death of the Microsection
06/26/2025 | Bob Neves, Reliability Assessment Solutions, Inc.I got my start out of college grinding and polishing PCB microsections. My thumbs are a bit arthritic today because of the experience (microsection grinders know what I mean). Back then, via structures were rather large, and getting to the center in six steps of grinding and polishing was easy compared to what my team has been doing recently at the lab.
Knocking Down the Bone Pile: Tin Whisker Mitigation in Aerospace Applications, Part 3
06/25/2025 | Nash Bell -- Column: Knocking Down the Bone PileTin whiskers are slender, hair-like metallic growths that can develop on the surface of tin-plated electronic components. Typically measuring a few micrometers in diameter and growing several millimeters in length, they form through an electrochemical process influenced by environmental factors such as temperature variations, mechanical or compressive stress, and the aging of solder alloys.