-
- News
- Books
Featured Books
- pcb007 Magazine
Latest Issues
Current IssueIn Pursuit of Perfection: Defect Reduction
For bare PCB board fabrication, defect reduction is a critical aspect of a company's bottom line profitability. In this issue, we examine how imaging, etching, and plating processes can provide information and insight into reducing defects and increasing yields.
Voices of the Industry
We take the pulse of the PCB industry by sharing insights from leading fabricators and suppliers in this month's issue. We've gathered their thoughts on the new U.S. administration, spending, the war in Ukraine, and their most pressing needs. It’s an eye-opening and enlightening look behind the curtain.
The Essential Guide to Surface Finishes
We go back to basics this month with a recount of a little history, and look forward to addressing the many challenges that high density, high frequency, adhesion, SI, and corrosion concerns for harsh environments bring to the fore. We compare and contrast surface finishes by type and application, take a hard look at the many iterations of gold plating, and address palladium as a surface finish.
- Articles
- Columns
Search Console
- Links
- Media kit
||| MENU - pcb007 Magazine
Estimated reading time: 1 minute
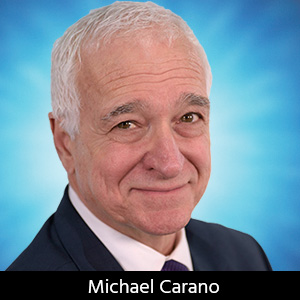
Contact Columnist Form
PTH Drilling Revisited - Fundamentals, Part 1
Anyone involved in coaching athletes preaches fundamentals. That means understanding what is at stake and relentlessly executing the basic fundamentals of the craft. Drilling circuit boards is no exception. The basic fundamentals of PTH drilling revolve around several key factors: 1) speeds and feeds--drill in-feed rate and spindle speed of the drill bit; 2) surface feet per minute; and 3) the material to be drilled. Understanding and applying these first few critical factors will influence the overall quality of the drilled, plated through-hole, and eliminate issues such as rough hole-walls, excessive nailheading and resin smear. In a future column, additional drill fundamentals will be explored.
Regardless of whether you are playing a football game or manufacturing a printed circuit board, it is all about fundamentals. Understand what needs to be accomplished and how to get there. Success, however it is defined, should not be difficult to achieve. In this edition of Trouble in Your Tank, I will present some of what I consider the key fundamental understandings required if one is to drill a quality plated through-hole.
Basic Fundamentals
The goal is quite simple. You want to build as much reliability into the PTH as possible. Of course, there are numerous factors and process steps involved in manufacturing high-quality, highly reliable PCBs. And yes, drilling is just one of those processes. But the old adage applies here: Garbage in, garbage out. A poor quality drilled via will only exacerbate additional problems downstream in the fabrication process. So it is first and foremost about fundamentals. In my travels working with PCB and assembly companies on a global basis, I am often struck by the lack of understanding with respect to the basic fundamentals of drilling a plated through-hole. One would think that common sense would prevail, that does not always happen. Suffice to say that one should always consult the drill supplier with help in setting up the proper parameters. This will depend on hole diameters, board thickness, resin materials and drill machine capabilities. But there are basic fundamentals that apply. So let’s discuss the basics and illustrate what some of the undesired outcomes are when we do not follow the rules.
Read the full column here.
Editor's Note: This column originally appeared in the April 2014 issue of The PCB Magazine.
More Columns from Trouble in Your Tank
Trouble in Your Tank: Yield Improvement and ReliabilityTrouble in Your Tank: Causes of Plating Voids, Pre-electroless Copper
Trouble in Your Tank: Organic Addition Agents in Electrolytic Copper Plating
Trouble in Your Tank: Interconnect Defect—The Three Degrees of Separation
Trouble in Your Tank: Things You Can Do for Better Wet Process Control
Trouble in Your Tank: Processes to Support IC Substrates and Advanced Packaging, Part 5
Trouble in Your Tank: Materials for PWB Fabrication—Drillability and Metallization
Trouble in Your Tank: Supporting IC Substrates and Advanced Packaging, Part 5