-
- News
- Books
Featured Books
- pcb007 Magazine
Latest Issues
Current IssueIn Pursuit of Perfection: Defect Reduction
For bare PCB board fabrication, defect reduction is a critical aspect of a company's bottom line profitability. In this issue, we examine how imaging, etching, and plating processes can provide information and insight into reducing defects and increasing yields.
Voices of the Industry
We take the pulse of the PCB industry by sharing insights from leading fabricators and suppliers in this month's issue. We've gathered their thoughts on the new U.S. administration, spending, the war in Ukraine, and their most pressing needs. It’s an eye-opening and enlightening look behind the curtain.
The Essential Guide to Surface Finishes
We go back to basics this month with a recount of a little history, and look forward to addressing the many challenges that high density, high frequency, adhesion, SI, and corrosion concerns for harsh environments bring to the fore. We compare and contrast surface finishes by type and application, take a hard look at the many iterations of gold plating, and address palladium as a surface finish.
- Articles
- Columns
Search Console
- Links
- Media kit
||| MENU - pcb007 Magazine
Estimated reading time: 1 minute
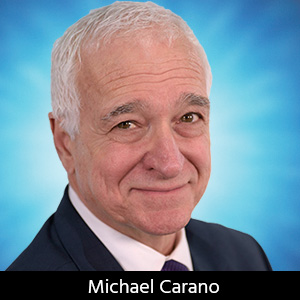
Contact Columnist Form
Oxide vs. Oxide Alternative, Part 2
In last month’s column, I presented an overview of conventional oxide chemistry and the critical success factors of the process. In this column, we begin our review of the oxide alternative process that is often referred to as an organo-metallic coating process. The reason for this alternative name will be explained in this column.
With continued emphasis on long-term reliability and vastly improved electrical performance, manufacturers of high layer-count multilayer printed wiring boards are beginning to abandon the reduced oxide bonding process in favor of alternative methods. One such method, presented here as an organo-metallic adhesion promotion system, increases the bond strength of the resin to the copper by modifying the topography of the copper surface and simultaneously depositing an organic layer that acts as an adhesion promoter. The surface area or topography of the copper is enhanced by the selective micro-etching along the grain boundaries of the copper. (This mechanism will be discussed further below.) This is in contrast to the oxide-based chemical processes in that the oxide processes are designed to “grow a crystal structure” on the copper surface. The concern with oxide processes (even the formulations designed to give a denser shorter crystal structure) is that the higher pressures and temperatures of lamination required for higher performance laminate materials will fracture the oxide crystal structure reducing the bond strength. With that said, let’s discuss oxide alternative or organo-metallic chemistry and how it all works.
Read the full column here.
Editor's Note: This column originally appeared in the March 2014 issue of The PCB Magazine.
More Columns from Trouble in Your Tank
Trouble in Your Tank: Yield Improvement and ReliabilityTrouble in Your Tank: Causes of Plating Voids, Pre-electroless Copper
Trouble in Your Tank: Organic Addition Agents in Electrolytic Copper Plating
Trouble in Your Tank: Interconnect Defect—The Three Degrees of Separation
Trouble in Your Tank: Things You Can Do for Better Wet Process Control
Trouble in Your Tank: Processes to Support IC Substrates and Advanced Packaging, Part 5
Trouble in Your Tank: Materials for PWB Fabrication—Drillability and Metallization
Trouble in Your Tank: Supporting IC Substrates and Advanced Packaging, Part 5