-
- News
- Books
Featured Books
- pcb007 Magazine
Latest Issues
Current IssueIn Pursuit of Perfection: Defect Reduction
For bare PCB board fabrication, defect reduction is a critical aspect of a company's bottom line profitability. In this issue, we examine how imaging, etching, and plating processes can provide information and insight into reducing defects and increasing yields.
Voices of the Industry
We take the pulse of the PCB industry by sharing insights from leading fabricators and suppliers in this month's issue. We've gathered their thoughts on the new U.S. administration, spending, the war in Ukraine, and their most pressing needs. It’s an eye-opening and enlightening look behind the curtain.
The Essential Guide to Surface Finishes
We go back to basics this month with a recount of a little history, and look forward to addressing the many challenges that high density, high frequency, adhesion, SI, and corrosion concerns for harsh environments bring to the fore. We compare and contrast surface finishes by type and application, take a hard look at the many iterations of gold plating, and address palladium as a surface finish.
- Articles
- Columns
Search Console
- Links
- Media kit
||| MENU - pcb007 Magazine
Estimated reading time: 2 minutes
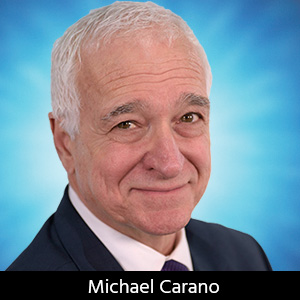
Contact Columnist Form
Fine Lines and Spaces, Part 3: Chemical Surface Preparation
The photoimaging process is one of the first steps in the PCB fabrication process. In order to ensure that the image of the circuitry conforms as close to the desired design as possible (i.e., lines and spaces), preparation of the copper foil surface is one of the critical success factors. Employing the optimum mix of surface cleaners and microetchants will provide a clean surface with sufficient area to promote dry film adhesion. The fabricator has numerous options and should determine the optimum process by accounting for the type of copper foil used, as well as the classes of soils to be removed.
Introduction
In the last two columns I discussed pumice and aluminum oxide surface preparation. Another technique that has gained significant market share is chemical surface preparation. In this case, only chemical processes such as acid cleaners and micro-etchants are employed. However, let’s first discuss the subject of the chromate conversion coating.
Chromate Conversion Coating
All copper foil and/or laminate producers process the foil through an anti-tarnish treatment that is based on chromic acid, which provides a hydrated chromate film that prevents oxidation of the copper surface. While preventing oxidation is necessary during storage, the chromate must be removed prior to micro-etching to avoid differential or step-etch during the micro-etching process. The step-etch will leave the copper surface with a non-uniform topography, which will invariably lead to less than optimum photoresist adhesion. The potential for resist to lock into some of the non-uniform areas on the foils is quite high mainly due to the extreme peaks and valleys in the surface profile. The best remedy to prevent this situation is to completely remove the chromate film.
In the past, tarnish resistance was accomplished by immersion of the copper foil into a solution containing chromate ions. Yates and other further improved upon this method with an electrolytic technique to enhance the oxidation resistance of the copper foil. Still, others improved upon this invention further with the introduction of zinc chromate.
One should never underestimate the tenacity of the chromate film. This is precisely why I recommend a strong mineral acid cleaning step prior to pumice, aluminum oxide or chemical microetching. It is much more effective to enhance the resist adhesion when a good chromate removal process is online prior to these additional processes.
Read the full column here.
Editor's Note: This article originally appeared in the January 2014 issue of The PCB Magazine.
More Columns from Trouble in Your Tank
Trouble in Your Tank: Yield Improvement and ReliabilityTrouble in Your Tank: Causes of Plating Voids, Pre-electroless Copper
Trouble in Your Tank: Organic Addition Agents in Electrolytic Copper Plating
Trouble in Your Tank: Interconnect Defect—The Three Degrees of Separation
Trouble in Your Tank: Things You Can Do for Better Wet Process Control
Trouble in Your Tank: Processes to Support IC Substrates and Advanced Packaging, Part 5
Trouble in Your Tank: Materials for PWB Fabrication—Drillability and Metallization
Trouble in Your Tank: Supporting IC Substrates and Advanced Packaging, Part 5