-
- News
- Books
Featured Books
- pcb007 Magazine
Latest Issues
Current IssueIn Pursuit of Perfection: Defect Reduction
For bare PCB board fabrication, defect reduction is a critical aspect of a company's bottom line profitability. In this issue, we examine how imaging, etching, and plating processes can provide information and insight into reducing defects and increasing yields.
Voices of the Industry
We take the pulse of the PCB industry by sharing insights from leading fabricators and suppliers in this month's issue. We've gathered their thoughts on the new U.S. administration, spending, the war in Ukraine, and their most pressing needs. It’s an eye-opening and enlightening look behind the curtain.
The Essential Guide to Surface Finishes
We go back to basics this month with a recount of a little history, and look forward to addressing the many challenges that high density, high frequency, adhesion, SI, and corrosion concerns for harsh environments bring to the fore. We compare and contrast surface finishes by type and application, take a hard look at the many iterations of gold plating, and address palladium as a surface finish.
- Articles
- Columns
Search Console
- Links
- Media kit
||| MENU - pcb007 Magazine
Estimated reading time: 1 minute
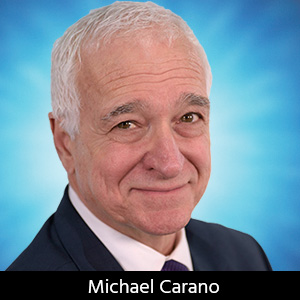
Contact Columnist Form
Achieving Fine Lines and Spaces, Part 2
Achieving high yields with fine lines and spaces requires a good understanding of surface preparation methods. These include pumice and chemical cleaning. In essence, the surface profile of roughness plays a role in resist adhesion.
Pumice vs. Chemical Cleaning
As someone who has frequently worked with PCB fabricators on a global basis, I must confess that surface preparation and imaging issues rank quite high on the list of yield loss. In previous columns, I have stressed the basic fundamentals. That is, understand what you are up against (which soils are on the surface, what are the interactions of the process parameters, etc.) in order to optimize yields. As stated previously, in order to minimize distortion and material stretching, mechanical methods of surface preparation are giving way to chemical cleaning. Copper foils and are also trending toward lower thicknesses in order to improve fine-line etching. Secondly, the need to improve impedance control with today’s high-speed electrical requirements is driving the implementation of low profile copper foil. These lower-profile foils are generally of a finer grain size, further impacting the ability to affect a surface topography sufficient to enhance photoresist adhesion. So let’s first review the importance of surface topography and photoresist adhesion.
Critical Surface Profile Parameters
I stated earlier that poor resist adhesion leading to defects such as opens or shorts, peeling and interfacial voids, are related to numerous issues including, surface preparation, characteristics of the copper foil, lamination parameters, and the formulation of the photoresist itself. There are other causes of poor adhesion that are directly attributable to other factors such as developing and exposure. These causes will be explored in a future column. With respect to surface topography, I already stated that the randomness of the copper topography after surface prep is more beneficial than a unidirectional one seen with mechanical scrubbing. Pumice, aluminum oxide, and chemical clean impart the random or multidirectional topography that we are concerned with. While that is a good thing, let’s take a close look at critical profile or topographical parameters.
Read the full column here.
Editor's Note: This column originally appeared in the December 2013 issue of The PCB Magazine.
More Columns from Trouble in Your Tank
Trouble in Your Tank: Yield Improvement and ReliabilityTrouble in Your Tank: Causes of Plating Voids, Pre-electroless Copper
Trouble in Your Tank: Organic Addition Agents in Electrolytic Copper Plating
Trouble in Your Tank: Interconnect Defect—The Three Degrees of Separation
Trouble in Your Tank: Things You Can Do for Better Wet Process Control
Trouble in Your Tank: Processes to Support IC Substrates and Advanced Packaging, Part 5
Trouble in Your Tank: Materials for PWB Fabrication—Drillability and Metallization
Trouble in Your Tank: Supporting IC Substrates and Advanced Packaging, Part 5