-
- News
- Books
Featured Books
- pcb007 Magazine
Latest Issues
Current IssueSales: From Pitch to PO
From the first cold call to finally receiving that first purchase order, the July PCB007 Magazine breaks down some critical parts of the sales stack. To up your sales game, read on!
The Hole Truth: Via Integrity in an HDI World
From the drilled hole to registration across multiple sequential lamination cycles, to the quality of your copper plating, via reliability in an HDI world is becoming an ever-greater challenge. This month we look at “The Hole Truth,” from creating the “perfect” via to how you can assure via quality and reliability, the first time, every time.
In Pursuit of Perfection: Defect Reduction
For bare PCB board fabrication, defect reduction is a critical aspect of a company's bottom line profitability. In this issue, we examine how imaging, etching, and plating processes can provide information and insight into reducing defects and increasing yields.
- Articles
- Columns
- Links
- Media kit
||| MENU - pcb007 Magazine
Estimated reading time: 5 minutes
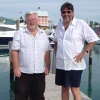
The Bleeding Edge: Carbon Nanotubes 101
The much-heralded and wondrous carbon nanotubes were discovered in 1991. Since then, many new applications have been reported by scientists who are attracted by the potentials of these very miniscule cylinders. Their potential to become the twenty-first century wonder materials has driven an entire industry with big budgets hoping to invent the next super product.
Carbon nanotubes are generally produced by three main techniques: Arc discharge, laser ablation and chemical vapor deposition. New methods being researched right now promise far more economic ways to produce nano particles.
In arc discharge, two carbon electrodes with a catalyst create an arc vapor discharge, and nanotubes grow outward from that carbon vapor. In laser ablation technology, a high-powered laser beam heats a volume of carbon in a methane or carbon monoxide gas. Chemical vapor deposition uses special gasses in plasma-like conditions to deposit carbon tubes directly to a surface. Laser ablation typically produces a smaller amount of cleaner nanotubes, whereas arc discharge methods generally produce large quantities of impure varying types of material. All methods are expensive to set up and run, producing only small amounts of carbon tubes at monumental prices.
The typical production batch of carbon nanotubes will have a quantity of low-conductivity particles as well as semi-conductive tubes and a small portion of highly conductive particles. The trick is to refine the production process to produce the highest percentage of the type of tube you require.
Carbon tubes are arranged into basic groups according to their wall characteristics: single-walled nanotubes (SWNTs), double-walled nanotubes (DWNTs) and multi-walled nanotubes (MWNTs). There are also subcategories that describe the size of the tube as well as extra features, such as bumps as well as the description of the type of fiber.
Carbon nanotubes of both single-walled and multi-walled varieties combine ultra-iniaturization with exceptionally high structural strength. Carbon tubes have very high surface areas (hundreds of square feet per gram), high melting temperatures (3,500°C) and high Young's modulus strength (1,000 gpa), for a strength 10,000 times that of steel. Some carbon tubes also feature high electrical conductivity of 1,000 s/cm, which is 20 times greater than copper, with corresponding very high thermal conductivity of 3,000 W/m°C or 10 times that of copper. All are highly desired properties.
It really is a matter of size; carbon nanotubes are 1 atom-thick sheets of graphite 125,000 times smaller than a human hair. The typical nano particle is a mere 25 hydrogen atoms wide--compare that to the dime in your pocket at 12,500,000 nanometers. Nanotubes range in diameter from less than one nanometer to about 40 nanometers.
Separating DWNTs from the SWNTs and MWNTs is the big trick. The problem lies with firing a metal in a hot gas to manufacture carbon tubes--you also make everything from carbon black (soot) to bucky balls and four to five different carbon tubes and every combination in between. A water bath can be used to separate the different tubes; each one with a different density. By varying the surface tension and density of the water bath, specific tube types will individually float up to be collected.
The carbon nanotube and its super properties are very desirable, but it also shows its bad side by being problematic for integration into our big world.
Carbon tubes tend to conduct only in one direction, and they don't mix well with metals or glues because of the non-wetting surface of the carbon. Carbon tubes do not conduct electrically well when combined in strings with other carbon nanotubes.
But the biggest showstopper is still price: Recent quotes for single-walled nanotubes are in the $20,000 per kg range, while multi-walled tubes sell for $10,000 per kg. Prices are starting to drop, but you have to be careful--you may wind up with a sizable quantity of undesirable carbon soot and metal. Many technologists have tried to incorporate carbon tubes into printing inks and metal castings only to find the tubes do not play well with others. Carbon nanotubes have a very high surface area. As the surface area increases, the static energy on the surface also increases--the static is so large compared to their size that the nanotubes want to clump together rather than stay dispersed.
Even though we read of the potential carbon nanotube inventions that scientists have created in their minds, in general nanotubes have yet to be incorporated into any everyday products. The simplest use is in reinforcing plastics. The carbon tubes' high static properties promote paint sticking and adds strength to the cast plastic material. The basic problem with utilizing nanotubes into electronics--in a PCB, as super-fine wires or as transistors on silicon--is the inability to arrange the tubes in such a way they electrically interconnect.
As a carbon tube passes current, there is little heat generated. In contrast, in typical normal copper wire, as the electrons pass through the wire they bump and dislodge other electrons. And all this bumping around creates friction and heat. The electrons in a carbon tube appear to flow right through, encountering little to bump into. Carbon nanotubes also have a different mechanism to transfer heat and do not exhibit the thermoelectric effect. This is a fundamental property of conductors by which a current flows because of a temperature difference between two points of contact. Carbon nanotubes are organic metals, which do not behave like ordinary metals. Most metals use electron flow, while carbon nanotubes are closer to the way diamonds move heat without electron flow.
The carbon nanotubes' higher current density does not lead to electro-migration and thermo-migration; it also produces just 1% of the heat produced by current flow in traditional metals, such as copper. The unique properties of carbon nanotubes will someday allow engineers to realize a host of smaller, faster and more powerful new devices that cannot exist today because of the limitations of conventional metals.
But America is in danger of losing this technical resource; there are many times more dollars being spent on nanotechnology research in Asia and Europe than in America.
For applications in PCBs, carbon nanotube traces offer less resistance than present copper conductors. In high-power circuits, carbon nanotube interconnects would reduce heat losses and require far less cooling than copper traces.
Like a metal wire, nanotubes grow hotter as electrical current is increased. At some point, even a nanotube will burn apart like an element in a blown fuse. The creation of an all-nano superconductor carbon tube sheet to replace the PCB's copper foil is a wish for another time. However, we are close to having nano-modified PCB copper foils, featuring a much lower resistance and greater current carrying capacity.
As research yields new nano applications in metal matrix and nano-modified organic glues, we can expect more powerful applications in PCB manufacturing. In the next five years, we can expect big changes in carbon nanotechnology for the electronic manufacturing industries.
Robert Tarzwell is president of DMR Ltd., a PCB technology and resources provider. He can be reached at bob@dmrpcb.com.
More Columns from Bob and Me
Controlled Impedance: A Real-World Look at the PCB SideBob and Me: The Key to Increasing Quality - Bribe Your Employees
Bob and Me: Tarzwell's First--and Last--Lean Meeting
Bob and Me: A PCB Potpourri
Bob and Me: Spacing is Irrelevant Below 270 Volts
PCB 101: Coefficient of Thermal Expansion
The Bleeding Edge: Serious as a Heart Attack
PCB101: Fabricating High-Voltage Boards