Estimated reading time: 6 minutes
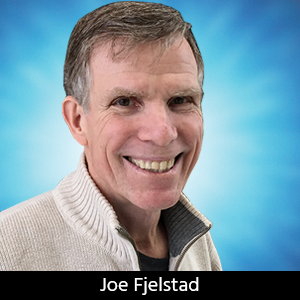
A Simple Approach to Flex Manufacture, Assembly
Flexible circuits top the list of versatile interconnection technologies. The advantages of flexible circuits have been enumerated countless times in electronic interconnection industry journals and technical proceedings.
Because of their versatility, flex circuits are ubiquitous. It is likely that the reader is the default owner of many flex circuits in various electronic products, from cell phones to computers to their cars. Unfortunately, flexibility, the single attribute that makes the technology so attractive, also makes them more difficult to build. In contrast to flex circuits, rigid board manufacture and assembly tasks are much easier because of the rigidity and intrinsic dimensional stability of the substrate.
Flex circuit manufacturers have thus had to develop and apply a range of new methods, equipment, fixtures and tools to help a flex circuit through the process from circuit construction circuit to component assembly. In most cases, the manufacturing solutions have gravitated towards those which allowed flex circuits to mimic their rigid cousins. Thus, with the exception of roll-to-roll processing, flexible circuits are commonly prepared and processed in ways that allow them to appear rigid to the process. Perhaps the most recognizable solution in this regard is the flex circuit stiffener, a piece of rigid material - either conductive or nonconductive, depending on design requirements - that is applied to a flexible circuit to make the circuit easier to handle and assemble with components.
A rigid-flex circuit can be an attractive alternative. Depending on the specifics of the design, a rigid-flex circuit can be fabricated in much the same manner as a standard multilayer circuit with some material changed and design and process modifications. While there can be a great deal of difference in design layout and complexity, in simplest terms a rigid-flex circuit is created by first fabricating a flexible circuit (normally with coverlayer) and then laminating the flex circuit into a structure incorporating rigid material caps. This paradigm has remained the status quo for the 40-plus years of rigid-flex circuit manufacture. It works well enough, but what if one could produce a circuit that was rigid throughout the entire manufacturing process and only become flexible in the final step?
To a certain degree, the idea of making a rigid circuit that could flex was explored in the 1980s with a material from Rogers Corporation called BendflexTM. Bendflex was a promising solution, but there were strict limits on bending, which if exceeded could fracture the copper circuits. While the material was not able to gain sufficient mind or market share to succeed, the basic premise and objectives of that effort were valid and worthy of pursuit.
Given the challenges of handling flexible base materials, a new holistic approach to flexible circuit manufacturing that encompasses both flex circuit manufacture and component assembly is in development. Following is a description of that prospective process which results in a product that is, in essence, a rigid-flex circuit of a new sort. The process is an extension of the manufacturing method that has come to be called the Occam Process, a process designed to simplify electronic manufacturing and assembly by eliminating solder from the overall process. In the process, copper electroplating and/or printed conductive circuit patterns are used to make the electronic interconnections, obviating the need for a high-temperature soldering step.
The process is relatively simple. First, fully tested packaged components and discrete devices are placed on a temporary of permanent carrier where they are fixed in place by means of a suitable adhesive or heat-releasable tacky material. It is important to use packaged components rather than bare die because they offer standard footprints for a given function. Because the circuit will have flexible or formable areas, any permanent carrier, if used, would desirably be comprised of a flexible material.
In accordance with traditional flex circuit design practices, components are excluded from the areas where flexing is to take place. The components are then encapsulated using a suitable material, which may include modified epoxies or various thermoplastics and applied using any established process including injection molding and various lamination methods. When the encapsulation process is complete, the assembly will appear to be a substantially rigid panel, a form familiar to all traditional PCB manufacturers.
The next step is to clean the component leads, which these days are typically copper beneath the finish. In the future, component leads will desirably be all copper to save the expense of applying an unnecessary solderable finish. With the component terminations exposed by vias, the assembly can now be plated using now-familiar build-up plating methods or, as mentioned earlier, by various printed conductor methods which are seeing greater interest.
As is common practice in flex circuit design, the number of circuit layers through the areas where flexing or bending is anticipated should be limited to 1 or 2 metal layers.
After completing the build-up of all required circuit layers and the addition of a final flexible top layer, the assembly can be functionally tested, if desired. On completion of testing, the assembly - comprising components and circuits - is flipped over and a suitable numerically controlled tool is used to remove materials from the areas which are to be flexed. Examples of such tools include lasers which can ablate material, or an end mill or router with cutting bits that have rounded cutting edges to provide an integral strain relief. The basic process steps are illustrated in Figure 1.
Figure 1. This illustrates a simplified process for fabricating flex circuits with encapsulated components. In sequence starting in the upper left corner, first, components are placed on a temporary or permanent carrier (temporary shown). Next, they are encapsulated and removed from the carrier. A flexible film or coating is applied to the component contact surface and access to component terminations is created. The assembly is then metalized, imaged and plated as required and provided with a top flexible film or coating. Final steps include a functional test and removal of materials from areas to be flexed.
Though some process details are missing, it should be clear that the total number of processing steps is significantly less than is required using more traditional manufacturing methods which involve first the manufacture of the flex or rigid-flex circuit followed by assembly. The method, as described, offers significant time and cost savings as well as worry-free compliance with RoHS requirements. Moreover, there are a number of special techniques available that are not possible using traditional manufacturing methods, including the integration of thermal management solutions such as heat spreaders. The final assembly can then be folded into a compact assembly or formed to fix easily into the desired shape. There are many other possibilities.
While the basic Occam process, on which this flexible circuit variation is predicated, is generally viewed as compelling by many knowledgeable printed circuit manufacturing technologists, the one compelling question most often asked is: "What about rework and repiar?" This question is best answered with another compelling question: "Why do you need to rework?"
The answer to the latter question is inevitably that because the soldering process is imperfect and shorts and opens are common defects and increasingly the high temperatures of lead free solders take a toll on the reliability of electronic components one must be prepared to rework an repair circuits. Unfortunately, as component lead pitches continue to shrink, the challenges grow exponentially more onerous and rework will become even more common, wasting time and valuable resources. By focusing on improving simpler processes, the economics of solderless assembly for both rigid and flexible circuits should prove out positively in the long run.
In summary, flex circuits - which are, by some estimates, a century-old technology - have proven their value. However, they are also an interconnection technology that could also benefit from some rethinking, especially with respect to the manufacturing processes used in their construction. Methods such as the ones described here are simpler and shorter and should find numerous applications as designers and manufacturers come to appreciate the benefits, especially in the light of the challenges facing the industry in the era a lead-free solder.
References
1. Occam White Paper at www.flexiblecircuittechnology.com2. Flexible Circuit Technology, 3rd Edition available at www.verdantelectronics.com
More Columns from Flexible Thinking
Flexible Thinking: The Key to a Successful Flex Circuit Design TransferFlexible Thinking: Flexible Circuit Technology—Looking Back and Forward
Flexible Thinking: Mind-tapping into January
Flexible Thinking: Another PCB Design Paradigm Shift in the Works
Flexible Thinking: Rules of Thumb—A Word to the Wise
Flexible Thinking: Musings on High Density Interconnections
Flexible Thinking: Integrated Passive Devices—Design Solutions With Many Benefits
Flexible Thinking: Mechatronics in a Flex World