-
- News
- Books
Featured Books
- smt007 Magazine
Latest Issues
Current IssueSupply Chain Strategies
A successful brand is built on strong customer relationships—anchored by a well-orchestrated supply chain at its core. This month, we look at how managing your supply chain directly influences customer perception.
What's Your Sweet Spot?
Are you in a niche that’s growing or shrinking? Is it time to reassess and refocus? We spotlight companies thriving by redefining or reinforcing their niche. What are their insights?
Moving Forward With Confidence
In this issue, we focus on sales and quoting, workforce training, new IPC leadership in the U.S. and Canada, the effects of tariffs, CFX standards, and much more—all designed to provide perspective as you move through the cloud bank of today's shifting economic market.
- Articles
- Columns
- Links
- Media kit
||| MENU - smt007 Magazine
Moisture Sensitivity Concerns in PCBs for Lead-free Assemblies
January 20, 2013 | Ray Prasad ConsultingEstimated reading time: 5 minutes
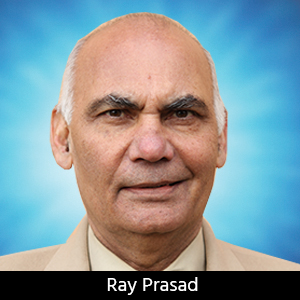
During the early stages of lead-free implementation, we were concerned with lead-free alloy selection and reliability issues. Now the majority of the industry is settled on SAC 305 alloy for reflow, although for some applications alternate alloys make sense. However, as I have discussed in my past columns, there is no complete unanimity about how to deal with mix of tin/lead and lead-free packages on the same board, copper dissolution during rework, or wave soldering of thru-hole components. Now a new issue has cropped up PCB delamination and moisture sensitivity and steps necessary to control them.
The focus of this column will be moisture sensitivity and moisture-sensitive PCB handling procedure. The key concern in PCB delamination is that moisture absorption between layers can impact PCB performance adversely. A little history is helpful before we delve into the PCB moisture sensitivity issues.
Moisture sensitivity concerns have been with us since the early days of high-volume SMT manufacturing in the mid 1980s. I chaired the first IPC document on handling of moisture-sensitive packages: IPC -786. This effort began in 1987 and the document was released within 18 months the fastest release of any IPC document, due to the urgent nature of the problem. Now that document has been replaced by J-STD-020 and J-STD-033. They deal with handling of moisture-sensitive packages, including guidelines for baking and bagging in desiccant bags to prevent delamination and cracks in component packages during reflow.
The component packages containing silicon are rated in eight categories from level 1 to 6, including levels 2a and 5a. Lower MSL rating is more desirable than higher MSL rating. For example, components rated as MSL 3 are allowed 168 hours of exposure time after the bags are unsealed. MSL ratings of 4 and 5 allow exposure times of 72 and 48 hours, respectively. Higher MSL rating, meaning shorter exposure time, requires much tighter production control on the factory floor. Therefore, the higher MSL rating is less desirable.
Back to PCB moisture sensitivity concerns. Some users recently discovered delamination in PCBs during lead-free reflow and lead-free rework. The root cause of delamination in PCBs during reflow and rework is poor controls on the curing and lamination process at PCB fabrication. Presence of moisture and higher peak reflow temperatures simply compound the problem.
One may disagree with the root cause, but the burden of solving this problem falls squarely on the PCB fabricator be it moisture or poor lamination process. For example, many users are asking the PCB supplier to bake and bag PCBs in desiccant bags, like component suppliers do for moisture-sensitive devices (MSDs). IPC now is supporting this effort; a new committee is in place to develop IPC 1601 that will deal with PCB moisture sensitivity issues. To quote the working draft of the IPC 1601, "The IPC 1601 guideline is intended to provide useful information on handling concerns, available packaging materials, environmental conditions, and possible storage methods for PCBs. The scope of coverage will be from the manufacture of the bare PCBs all the way to possible return of the bare PCB for warranty. As a guideline, this information is to be used with, and is secondary to, established requirements in such documents as the IPC-4550 series of documents (alternate final finishes). Effective use of this guideline is intended to prevent damage to and maintain reliability of PCBs."
This document is in its early stage. If you would like to get involved in this effort, this is the right time. Get in contact with John Perry at IPC if you have useful information to contribute or want simply to follow up the development of this important industry document.
The procedures for baking, bagging, and keeping track of exposure time on the factory floor are planned to be modeled after J-STD-020 and J-STD-033, but they will be different in many ways. For example, some of the surface finishes are more affected by baking than others and may have to be sent back to PCB suppliers for reconditioning. The document does plan to rate PCBs in different MSL categories as is the case for components. All the users have to do is monitor the floor exposure times in the factory as they do for moisture-sensitive components. This is not a trivial effort on the part of the PCB suppliers, since characterizing PCBs in different MSL categories, baking, and bagging with humidity indicator cards is a new process for them and will require investments.
While this industry effort is on its way, if you are already experiencing delamination problems, you don't have the time to wait until IPC-1601 is released. Development and release of a new document takes time. So ask your PCB suppliers to fix the root cause of the problem in their lamination process and then bake the PCBs and ship them in desiccant bags containing humidity indicator cards and guidelines for exposure time once the bags are unsealed. The humidity indicator cards turn pink when the moisture levels exceed the allowed exposure limits. Do keep in mind that if PCBs exceed exposure limits, you may have to rebake them, which may not be an option for some surface finishes.
The key concern in rebaking will be impact on solderability of surface finish. Some surface finishes are much more robust than others. For example, organic solderability preservative (OSP) and immersion silver (ImmAg) or tin (ImmSn) surface finishes may not do as well as electroless nickel immersion gold (ENIG) or hot air solder leveling (HASL) surface finishes. There are various IPC documents that provide guidelines for baking PCBs of different surface finishes. Some examples are IPC 6012, 6016, 4552, 4553, and IPC 4554. These documents provide baking guidelines, not what is being considered by IPC 1601, which is baking and bagging in desiccant bags before shipment.
If your PCB supplier is not willing to bake and bag PCBs, it may be wise for you to take a conservative approach and bake the PCBs yourself, particularly if you are experiencing PCB delamination. You can either bake only the boards needed for the day's production or bake all the PCBs, in which case you will have to bag them in desiccant bags and create guidelines for exposure time. This will require implementation of handling procedures similar to those for moisture-sensitive components. The focus should be on monitoring exposure time after the bag seal is broken, so that you do not have to rebake them again. Rebaking PCBs should be avoided it not only impacts solderability of the surface finish but may even require you to return them to the PCB supplier for reconditioning. These are expensive and time-consuming steps.