-
- News
- Books
Featured Books
- smt007 Magazine
Latest Issues
Current IssueSpotlight on India
We invite you on a virtual tour of India’s thriving ecosystem, guided by the Global Electronics Association’s India office staff, who share their insights into the region’s growth and opportunities.
Supply Chain Strategies
A successful brand is built on strong customer relationships—anchored by a well-orchestrated supply chain at its core. This month, we look at how managing your supply chain directly influences customer perception.
What's Your Sweet Spot?
Are you in a niche that’s growing or shrinking? Is it time to reassess and refocus? We spotlight companies thriving by redefining or reinforcing their niche. What are their insights?
- Articles
- Columns
- Links
- Media kit
||| MENU - smt007 Magazine
A New Method for Reworking SMT Components
September 29, 2010 | Bob Wettermann, BEST Inc.Estimated reading time: 6 minutes
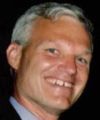
When reworking more complex SMT components, such as finer-pitch SMT connectors, area array devices and ultra-fine-pitch surface mount devices, the most common methods of rework--using either metal stencils or hand soldering--have a few shortcomings. Figure 1: Reworked fine-pitch QFP.The most significant problems incurred with the metal stencil printing rework method include the lack of coplanarity between the stencil and PCB, insuring that the stencil does not move during the printing process, the large space taken up by the metal stencil/fixturing system and the stencil cleaning process. These problems all result in a decrease in first pass yields and increase the time required to rework a device site. Hand soldering methods rely on the skill set of the operator and are, therefore, inconsistent and time-consuming. These methods are not economical in the higher labor cost countries and are difficult to use in space-constrained PCB layouts.A recently developed new stenciling process overcomes these deficiencies, resulting in better first pass yields and faster rework times--all while simplifying the rework process.Problems with Metal Stencil Rework Printing ProcessCoplanarity
One of the problems in using metal rework stencils is the lack of coplanarity between the metal stencil and the PCB. Without intimate contact between the metal stencil and the PCB, in all areas in and around the areas to be printed, poor print quality will result. Solder paste can "bleed" or leach underneath the stencil if it is not perfectly coplanar and in intimate contact with the board area being reworked. Some users will tape or fixture the edges of the rework stencil to the board as it may "fold up" along the edges during cleaning of the stencils--increasing the time required for reworking a location.Holding Alignment
Typical rework stencils require taping or special fixturing to position and hold them in place during the printing process to assure alignment. This takes up additional real estate on the PCB, which, in some cases, is unavailable. In addition, the metal fixturing systems carry with them a one-time cost, making them a pricey alternative if little rework of a given device type is required. Any taping required to hold down the metal stencil requires extra processing time for each and every board location being reworked. This operation in itself is highly operator-dependent, thereby impacting the yield.SpaceMetal stencils take up a significant amount of real estate relative to the area being reworked which makes this method a less than practical option for rework in some locations. Between the supporting fixtures and the peripheral areas of the stencil required for taping down the stencil, metal stencils, in many cases, are just too large for the rework area. Couple this with the space constraints of shrinking PCB real estate and the time for an alternate method of printing has come.Cleaning Impacts and Cleaning TimeThe cleaning of metal rework stencils leads to not only the deformation of the stencil, but it also consumes the rework technicians' time. When cleaning metal rework stencils and the associated fixtures, care must be taken to avoid deforming the stencils and fixtures. In addition, the aforementioned problems of damaged stencils can occur when proper handling techniques are not used. The lack of metal stencil coplanarity causes poor paste print release, as there is the lack of a gasketing effect. In addition, solder paste can spill out over the sides of damaged metal stencils--contaminating the circuit board. The yield impact of damaged stencils and metal stencils requiring cleaning between every print increases the processing time.Problems with Hand Soldering Rework ProcessThere are some deficiencies in using a hand soldering rework process for some of the more complex, high-density electronic components. First, the lack in consistent solder volumes and consistent hand soldering uniformity makes this a less desirous process--especially if several boards end up being scrapped. For some of the very fine-pitched parts in high-density areas, a high degree of rework technician skill is required which limits the throughput. In addition, nearby components can become damaged if the technician is not careful when placing the soldering iron. Lastly, hand soldering is not a cost-effective option in some cases, as it can be very time consuming.New Method Solves Many ProblemsIn this new rework printing method, a single-use specialty Mylar stencil with a "sticky tack" backing is used to simplify the process. The stencil can increase yields and is able to get in to the smaller areas required in some situations.This method consists of the same basic steps as the existing metal rework stencil printing process, albeit with some refinements. This emulates the original manufacturing process and assures consistent paste volume deposition and uniform solder joints for increased reliability. The process is outlined below:Figure 2: Peeling, single-use Mylar stencil from Liner.After site preparation, the stencil is peeled off its liner material, aligned over the pads and pressed into position. With the softness of the "stick back" adhesive, the stencil can be maneuvered back and forth until the final, micro adjustments for alignment are made.
Figure 3: Stencil is aligned over site and tacky adhesive allows for final adjustment onto PCB.Next, solder paste is rolled into the apertures. Multiple passes, allowed by the fact that the stencil is temporarily stuck to the PCB, allow for consistent paste volume to fill the apertures. The flexibility of the material along with the adhesive backing allows for the stencil to work well in and around board locations which may be warped. The border around the stencil (if room allows) acts as the masking tape eliminating the need for this extra step in the metal rework stencil printing process.
Figure 4: Rolling solder paste into stencil aperatures.Next, the stencil can be peeled off, resulting in a very consistent print volume. The stencil is designed to be discarded thereby bypassing the cleaning process and all of the problems mentioned previously.
Figure 5: Stencil being peeled off the PCB.Lastly, the device can be placed onto the printed areas, reflowed, cleaned and inspected per inspection criteria.This new rework stencil method solves several of the major problems associated with the metal rework stencil printing process. Since these stencils are a single-use item no cleaning is required. This eliminates the cost it takes to clean the stencil--allowing for the rework technician to have a higher throughput. In addition, since the metal stencil cleaning process (which invariably leads to the deformation of the stencil) is eliminated, a major cause of poor print quality is eliminated. Since no holding fixtures are required when using these stencils, and fold up tabs may be integrated into the design of the stencil to eliminate the need for nearby taping, they can be used in very small spaces. The challenge of holding the stencil onto the board during the printing process is overcome via the "sticky tack" adhesive system.The stencil's softness allows the rework technician to slide around the stencil for fine, micro-adjustments over the site to be reworked. This same adhesive insures coplanarity between the stencil and the PCB--even a warped PCB site. The newly developed adhesive-backed, single-use rework stencil overcomes many of the problems users have experienced in working with metal rework stencils, while still assuring that, unlike the hand soldering process, the process is a consistent rework method emulating the original manufacturing process as closely as possible.A video of the process can be seen here.
Bob Wettermann is an electrical engineer and has extensive experience in marketing and design. He holds several patents in the fields of surface science, factory automation products and SMT rework products/processes. He is a member of IPC and SMT.