Estimated reading time: 7 minutes
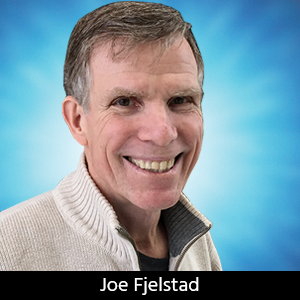
Flexible Thinking: An Alternative Approach to Rigid-Flex Assembly
Of all the electronic interconnection technologies available, flexible circuits are certainly among the most useful. The advantages of the flexible circuit technology have been recounted numerous times in electronic interconnection industry journals and technical proceedings. Flexible circuits are ubiquitous and it is safe to venture that the reader possesses many of them buried inside the many electronic products they own, from cell phones and MP3 players to laptops, automobiles and beyond.
Still, the fundamental attribute that makes the flexible circuit option so attractive (i.e., flexibility) is also the attribute which makes them more difficult to build. As a result, flex circuit manufacturers and assemblers have had to develop and apply a range of new methods and tools to help them get through the process from circuit manufacture to component assembly.
In contrast, the rigid board manufacturer's task is much easier, both in terms of circuit manufacture and component assembly. Realizing this, flexible circuit manufacturers have developed, over the years, many special tools, fixtures and methods. And equipment makers have developed special machines for handling, processing and assembling these highly desirable interconnection products.
For the most part, the solutions that have been developed have fundamentally revolved around methods that allowed flex circuits to mimic their rigid cousins. Thus, with the exception of roll-to-roll processing, flexible circuits are commonly prepared and processed in ways that allow them to appear rigid to the process. The most basic of these solutions is the stiffener, a piece of rigid material, either conductive or nonconductive depending on design requirements. For a standard flexible circuit, the benefits mostly serve the circuit assembler during processing as the flex circuit manufacturer applies the stiffener as one of the final steps.
In contrast to standard flex circuits, rigid-flex circuits can be fabricated in much the same manner as a standard multilayer circuit with some very important process modifications. Depending on the specifics and complexities of the design, the designer needs to assure by design that the flexible areas will flex when the circuit is removed from the panel on which it has been fabricated. This fundamental approach has remained a constant for the 40-plus years of rigid-flex history.
But is there a better way? What if one could produce a circuit that was rigid throughout the entire manufacturing process and only become flexible in the final step? In other words, what if one could make a rigid circuit assembly, flex?
To a degree, this was tried in the 1980s with a material called Bendflex introduced by Rogers Corporation, but there were strict limits on bending that needed to be accounted for and unfortunately the material was not able to gain mind or market share. Still, the basic premise and objectives of that effort remain valid and worthy of pursuit.
With this premise, the following is a description of a prospective process for manufacturing a rigid-flex circuit of a different sort. The process is an extension of concepts based on what has come to be known internationally as the Occam Process, a process designed to simplify electronic manufacturing and assembly by eliminating solder from the overall process.
In place of solder, copper electroplating is used to make the electronic interconnections. Lead-free alloys can require processing at temperatures approaching 260ºC. Such elevated temperatures can damage both electronic components and the substrates on to which they are mounted.
The new patent-pending process is relatively simple. First, tested and burned-in low-profile component (preferably land grid array devices and dual and quad non-leaded devices and various discrete and/or integrated passive) devices are placed on a temporary or permanent carrier where they are fixed in place by means of a suitable adhesive and/or heat-releasable tacky material. The devices will ideally have a copper finish, which will make them less expensive and eliminate one thermal excursion. Also, it will allow them to be lower-profile, because a solder termination often represents half of the height of a surface-mounted component.Because the circuit will have flexible or formable areas, any permanent carrier, if used in the design, would desirably be composed of a flexible material. In accordance with standard flex circuit design practices, components are excluded from the areas where flexing is to take place. The components are then encapsulated using a suitable material, which may include modified epoxies or various thermoplastics.
Figure 1: This graphic depicts a simplified process for fabricating integrated rigid-flex circuits with encapsulated components in rigid sections. Components are placed on a temporary or permanent carrier (temporary shown), then encapsulated and removed. Next a flexible film or coating is applied and openings for component terminations are created. The assembly is next metalized, imaged and plated as required, and provided with a top flexible film or coating. Final steps include functional test and removal of materials from areas to be flexed by methods such as machining.
When the initial processing is complete, the assembly will appear to be a substantially rigid panel, a form familiar to all traditional PCB manufacturers. The next step is to clean the component leads, which these days are typically copper beneath the finish. With the exposed copper terminations, the assembly can now be plated using now-familiar build-up plating methods. Again, as is common practice in flex circuit design, the number of circuit layers through the areas where flexing or bending is anticipated should be limited to 1 or 2 metal layers. After completing the build-up of all required circuit layers and the addition of a final flexible top layer, the assembly can be functionally tested.
On completion of testing, the assembly--comprising components and circuits--is flipped over. Then a suitable numerically-controlled tool, such as a laser, end mill or router bit with rounded cutting edges to provide an integral strain relief, is used to remove and thin material in the areas where flexibility is required. The basic process steps are illustrated in Figure 1.As can be seen in Figure 1, depending on the design needs, the total number of processing steps can be significantly less than traditional methods used in the manufacture and assembly of either flex or rigid-flex circuits. This offers significant cost and time savings overall, and worry-free compliance with RoHS requirements.
Moreover, a number of special techniques can be used that are not possible with traditional manufacturing methods, including the integration of thermal management solutions such as heat spreaders. The final assembly can then be folded into a compact assembly or formed to fit easily into the desired shape.
There are many other possibilities and admittedly the process as described here may not be suitable for all rigid-flex needs, but it does not need to be. It only needs to solve specific problems where it can be applied.
While the Occam process is generally viewed as compelling by a great number knowledgeable printed circuit manufacturing technologists, the one recurring question that is most often asked is: "What about rework?" This question is perhaps best met by another question. That question is, "Why do you need to rework?" The well understood answer to this pointed question is that the soldering process is imperfect and shorts and opens are common defects. This is especially true as component lead pitches continue to shrink. Here the challenges to yield grow increasingly onerous with each pitch reduction and cleaning beneath components gets ever more difficult.
In addition, the high temperatures required for most commonly used lead-free solders are taking an increasing toll on the reliability of electronic components during assembly. (To assure full disclosure, there are some lower melting-point lead-free solders but they tend to be expensive and/or of limited application.)As a result of the two primary factors just reviewed, many in manufacturing have resigned themselves to believing that rework is required for soldering and unfortunately, even using today's best manufacturing methods, they are right. However, by focusing on improving simpler processes, the economics of solderless assembly should prove out positively in the long run because of the fewer manufacturing steps and the reduced materials requirements.
In summary, flex circuits are, by some estimates, a century-old technology and they have fully proven their value and place in the pantheon of electronic interconnections. However, they are also an interconnection technology which could benefit from some rethinking relative to their manufacture. Alternative methods such as the one just described, being simpler and shorter, should find numerous applications as designers and manufacturers come to appreciate the benefits, especially in the light of the challenges facing the industry in the era a lead-free solder.
Verdant Electronics Founder and President Joe Fjelstad is a four-decade veteran of the electronics industry and an international authority and innovator in the field of electronic interconnection and packaging technologies with more than 250 U.S. and international patents issued or pending. He is also the author of "Flexible Circuit Technology" and author, co-author or editor of several other books and more than 300 technical papers, articles and columns. To contact Joe, click here.
More Columns from Flexible Thinking
Flexible Thinking: The Key to a Successful Flex Circuit Design TransferFlexible Thinking: Flexible Circuit Technology—Looking Back and Forward
Flexible Thinking: Mind-tapping into January
Flexible Thinking: Another PCB Design Paradigm Shift in the Works
Flexible Thinking: Rules of Thumb—A Word to the Wise
Flexible Thinking: Musings on High Density Interconnections
Flexible Thinking: Integrated Passive Devices—Design Solutions With Many Benefits
Flexible Thinking: Mechatronics in a Flex World