-
- News
- Books
Featured Books
- smt007 Magazine
Latest Issues
Current IssueSupply Chain Strategies
A successful brand is built on strong customer relationships—anchored by a well-orchestrated supply chain at its core. This month, we look at how managing your supply chain directly influences customer perception.
What's Your Sweet Spot?
Are you in a niche that’s growing or shrinking? Is it time to reassess and refocus? We spotlight companies thriving by redefining or reinforcing their niche. What are their insights?
Moving Forward With Confidence
In this issue, we focus on sales and quoting, workforce training, new IPC leadership in the U.S. and Canada, the effects of tariffs, CFX standards, and much more—all designed to provide perspective as you move through the cloud bank of today's shifting economic market.
- Articles
- Columns
- Links
- Media kit
||| MENU - smt007 Magazine
Estimated reading time: 4 minutes
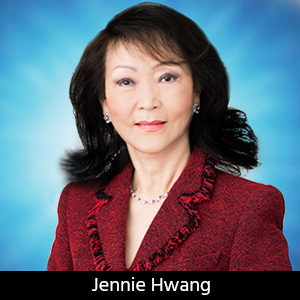
Reliability of Lead-Free System: Part I, Solder Joint Fatigue
Editor's Note: This column originally appeared in the August 2011 issue of SMT Magazine.Fatigue is one of the most likely culprits for material failure under cyclic or repeated stress conditions--regardless of metals, polymers or ceramics--due to the cumulative fatigue damage. Soft solder material, which has a low melting temperature customarily recognized as below 400°C (752°F), is particularly susceptible to fatigue.
When soft solder, tin-lead or lead-free are used as solder joints in electronic circuits, absent of any other failure causes, solder joint failure is often attributed to fatigue. In electronic applications, the solder fatigue damage may not be caused by mechanical loads, but rather by the temperature fluctuation as the result of in-circuit functions, power on-and-off and/or external environmental temperature exposure. These temperature changes inevitably generate cyclic thermal stresses in a thermal-expansion-coefficient mismatched system during the service life of electronic packages and assemblies, causing thermal fatigue (as opposed to mechanical fatigue).
Fatigue is a progressive and localized structural damage (atomic- and larger-scale levels) which occurs when the solder joint is subject to cyclic stresses (loads and unloads). When the stress exceeds a certain threshold, microscopic cracks will begin to form. This localized damage mechanism separates fatigue from creep behavior.
As the cyclic stress continues, a crack will propagate and eventually reach a critical size, and the solder joint will fracture. Generally, the fatigue process undergoes three stages: Crack initiation, crack propagation and fracture. For solder joints functioning as the electrical, thermal and mechanical interconnections in a circuitry, a mechanical fracture is generally not a practical criterion of failure. The electrical performance, as measured by resistance increase due to cracks, is used as a failure criterion. Electrical failure often precedes mechanical fracture. When in the presence of corrosive elements, a corrosion-enhanced fatigue could also occur.
Fatigue strength, correlating to fatigue life, is defined as the stress value at which a failure occurs after a given number of cycles. The fatigue strength depends not only on the specific solder alloy material, the extreme high temperature and the extreme low temperature, but also other factors: Surface defects, notches, holes, residual stress, voids, gas porosity and inclusions. All of these "imperfections or defects" could act as the stress concentration sites to initiate the localized damage under the fatigue environment. This is the reason why defects, such as voids or surface cracks, should not be categorically dismissed even when some test results do not reveal the performance difference between the presence and absence of such defects.
At the atomic level, the solder joint fatigue mechanism starts with dislocation movement and then forms slip band that nucleate short cracks. Micro-structurally, grain coarsening is often a result as observed under the SEM examination. Grain size is important to fatigue—the smaller, the better. When other defects exist, such as a surface defect, a defect rules.
Comparing a SAC lead-free solder joint with a SnPb solder joint, distinct intrinsic differences in their respective metallurgy determines their dislocation systems, microstructures and metallurgical phases, which, in turn, dominate the fatigue behavior and degradation mechanism in response to various service conditions and, thus, the fatigue life.
It should be noted that stresses acting upon solder joints in real-world applications are usually random in nature rather than "regularly" cyclic as the commonly used parameters in an accelerated temperature cycling (ATC) test. One challenge is to extrapolate from cyclic test data to the behavior under actual random stresses. Based on the underlying metallurgy, this challenge escalates in an SAC lead-free system in comparison with tin-lead eutectic. (Note: The SAC is a lead-free system and the lead-free is not always necessarily an SAC.)
In practical terms, a fatigue phenomenon involves chance, randomness and probability. This is why one simple ATC test is hardly able to lead to a conclusion. And it stands to reason that the test data should be in congruence with the principles of science and needs to be checked and balanced with the underlying scientific principles--in this case, the fundamental metallurgy and fracture mechanics. Yet that knowledge is not often exercised. (More discussion will be forthcoming in future publications of this column.)
Additionally, most soft solders, even under ambient temperatures (298 ± 5°K), reach a homologous temperature well beyond 0.5. Therefore, creep behavior is also expected to occur, which complicates the overall degradation behavior and failure mechanism as the creep and fatigue processes operate interactively.
About the Author: Dr. Hwang, a pioneer and long-standing contributor to SMT manufacturing since its inception as well as to the lead-free development, has helped improve production yield and solved challenging reliability issues. Among her many awards and honors, she has been inducted into the WIT International Hall of Fame, elected to the National Academy of Engineering and named an R&D-Stars-to-Watch. Having held senior executive positions with Lockheed Martin Corporation, Sherwin Williams Co., SCM Corporation and IEM Corporation, she is currently CEO of H-Technologies Group providing business, technology and manufacturing solutions. She is a member of the U.S. Commerce Department's Export Council, and serves on the board of Fortune 500 NYSE companies and civic and university boards. She is the author of 300+ publications and several textbooks and an international speaker and author on trade, business, education and social issues. Contact her at (216) 577-3284; e-mail JennieHwang@aol.com.
Dr. Hwang will present two workshops, "BTC Assembly – Material, Process, Reliability" and "BGA/CSP/WLP Reliability in Packaging and Assembly," at the SMTA International Conference, October 17, 2011, in Fort Worth, Texas.
More Columns from SMT Perspectives and Prospects
SMT Perspectives and Prospects: Warren Buffett’s Perpetual Wisdom, Part 2SMT Perspectives and Prospects: Warren Buffett’s Perpetual Wisdom, Part 1
SMT Perspectives and Prospects: Artificial Intelligence, Part 5: Brain, Mind, Intelligence
SMT Perspectives and Prospects: Artificial Intelligence, Part 4—Prompt Engineering
SMT Perspectives and Prospects: The AI Era, Part 3: LLMs, SLMs, and Foundation Models
SMT Perspectives and Prospects: A Dose of Wisdom
SMT Prospects and Perspectives: AI Opportunities, Challenges, and Possibilities, Part 1
SMT Perspectives and Prospects: Critical Materials—A Compelling Case, Part 3