Estimated reading time: 5 minutes
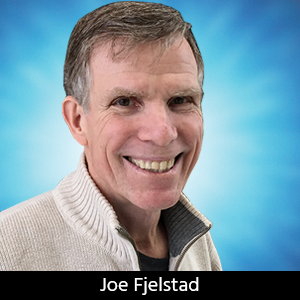
Something Old, Something New: Stretchable Circuits and Elastronics
The 3rd Flexible and Stretchable Circuit Conference will be held on November 15-17 in Berlin, Germany. The first of these conferences was held in 2007 in Leuven, Belgium and the second in Ghent, Belgium in 2009. The previous events have been impressive, with interesting and compelling presentations from both industry and academia on a topic that is on the rise in the world of electronics interconnection.
Interest in stretchable circuits has grown steadily in the last few years, propelled at least in part by the European Union’s funding of research in the area through initiatives such as STELLA, which ran from February 2006 to January 2010. There were 11 participants in the project, representing the electronics industry, academia and research institutes located in four EU countries and funded to the tune of over €13 million, with €7 million contributed by the European Commission. That jump-start yielded a number of interesting technology demonstrators. The mixture of stretchable substrates and electronic components and circuits has resulted in the coining of the term elastronics, which seems appropriate given the description.
The stretching of circuits to alternately increase and decrease the length of a circuit has proven to be useful for electronic products and assemblies for many years. The droop one sees in telephone wires is there for addressing the stretching and tensioning of the wires that occurs because of the changes in temperature they experience being out in the open. Similarly, service loops in flexible circuit assemblies serve to provide the benefits of stretching but without the stretch. In the past, stretching of a circuit has typically been accomplished by folding a flexible circuit in an accordion-like manner as shown in Figure 1. This type of circuit stretching is accomplished in an out-of-plane fashion which contrasts with most current efforts which seek to stretch the circuit in-plane and potentially in all directions. (X,Y and Z) at once.
Figure 1. Early version of a stretchable circuit design and application.
The resilience of constructions of the type is limited since the metals used (normally copper) will tend to plastically deform and thus they rely on the elasticity of the polymer to help the circuit return to shape (to what ever degree it can). More springy metals will reduce this tendency, but there are a number of electro-mechanical trade-offs that must be considered which such choices.
A number of applications over the years have successfully used this accordion method, including drawers containing electronics, which allows easier access for repairs, replacements or upgrades to the system. Thus the humorous bumper sticker “Play an accordion, go to jail. It’s the law” does not necessarily apply in the realm of flexible circuit design.
While out-of-plane stretching of circuit constructions may be useful in many applications, they are of limited value in other applications which require the stretching of circuits with a low (i.e., thinner) profile. In response to the anticipated need for thin stretchable circuits, (i.e., stretchable in-plane), there is now an evolving branch of electronic interconnections designed to resiliently interconnect electronic elements of every type, including components, such as printed circuits, that feature various electronic devices including integrated circuits; discrete devices such as capacitors and resistors; light-emitting components (e.g., LEDs), sensing devices that include micro-electromechanical systems (MEMS), etc.
The types of applications being explored for use with and/or enabling by stretchable circuits range from fashion and apparel to medical monitoring and diagnostic equipment. These are largely applications where the use of conventional flat rigid assembled PCBs becomes problematic because there is a need to comfortably integrate the circuit on a non-flat surface. Often wearable and implantable circuits (such as those for biomedical applications, sports and leisure, safety, etc.) require a degree of curvature in the assemblies because the circuit must follow the irregular shape and contours of the part onto or into which the circuit is integrated.
Ideally, the integration of the circuit should hamper the user’s activities minimally, if at all. One option to achieve this degree of comfort is the profound miniaturization of the circuit by using fine-pitch circuits, small components, 3D integration, etc. If, by applying this strategy, the circuit can be made on a small enough surface area (less than a few square centimeters for most wearable applications), it can still be implemented as a conventional rigid board. The lateral dimensions of the circuit should be small compared to the local bending radii of the non-flat surface at the point where the circuit is placed.
In cases where the miniaturization approach is not possible, the rigid board must be replaced by a mechanically flexible or stretchable version. A flat, flexible printed circuit, coming from a standard production line, can be deformed to a cylinder or a cone (as is often done in military applications), but such circuits cannot conform to a spherical or irregular surface. In contrast, a stretchable circuit provides a solution since it can be deformed from a flat surface to any shape, due to the presence of the stretchable interconnects.
In some cases, a circuit may be too complex to be sufficiently miniaturized. If this is the case, the large-area circuit can be split into several smaller area circuits. The sub-circuits are then joined by stretchable interconnections. This approach is similar to rigid-flex boards, where rigid PCB islands are interconnected by flexible printed circuits. Figure 2 shows a part of a fitness monitor, designed by Philips, that is worn on the wrist. The different electronic building blocks are realized on rigid PCB interposers that are subsequently mounted on a stretchable PCB, which is fabricated using stretchable copper board (SCB) technology.
Figure 2. Philips fitness monitor showing rigid interposers assembled on a stretchable interconnection substrate.
In summary, stretchable circuit technology and elastronics are poised to take on challenges than cannot be easily met by flexible circuit technology alone. Keep them in mind next time you find yourself in need of a little more “spring” in your design.
Note: This article was adapted from a section titled Stretchable Circuits, coauthored by Joseph Fjelstad and Professor Jan Vanfleteren, in Chapter 13 of the upcoming 4th Edition of "Flexible Circuit Technology."
Verdant Electronics Founder and President, Joseph (Joe) Fjelstad, is a four-decade veteran of the electronics industry and an international authority and innovator in the field of electronic interconnection and packaging technologies with more than 250 U.S. and international patents issued or pending. He is also the author of "Flexible Circuit Technology" and author, co-author or editor of several other books and more than 300 technical papers, articles and columns. To contact Joe, click here.
More Columns from Flexible Thinking
Flexible Thinking: The Key to a Successful Flex Circuit Design TransferFlexible Thinking: Flexible Circuit Technology—Looking Back and Forward
Flexible Thinking: Mind-tapping into January
Flexible Thinking: Another PCB Design Paradigm Shift in the Works
Flexible Thinking: Rules of Thumb—A Word to the Wise
Flexible Thinking: Musings on High Density Interconnections
Flexible Thinking: Integrated Passive Devices—Design Solutions With Many Benefits
Flexible Thinking: Mechatronics in a Flex World