-
- News
- Books
Featured Books
- pcb007 Magazine
Latest Issues
Current IssueSales: From Pitch to PO
From the first cold call to finally receiving that first purchase order, the July PCB007 Magazine breaks down some critical parts of the sales stack. To up your sales game, read on!
The Hole Truth: Via Integrity in an HDI World
From the drilled hole to registration across multiple sequential lamination cycles, to the quality of your copper plating, via reliability in an HDI world is becoming an ever-greater challenge. This month we look at “The Hole Truth,” from creating the “perfect” via to how you can assure via quality and reliability, the first time, every time.
In Pursuit of Perfection: Defect Reduction
For bare PCB board fabrication, defect reduction is a critical aspect of a company's bottom line profitability. In this issue, we examine how imaging, etching, and plating processes can provide information and insight into reducing defects and increasing yields.
- Articles
- Columns
- Links
- Media kit
||| MENU - pcb007 Magazine
Estimated reading time: 4 minutes
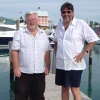
Burning Issues of Burn-in Boards Resolved Through New Technology
All manufacturers of burn-in boards struggle with high-current distribution problems, maximum finger-insertion thickness of .062, small-pitch copper wicking and CAF shorting problems, longevity at elevated temperatures, and thermal-cycle cracking of vias.
With the higher currents used for testing chips today, testing 40 microprocessors at 4 amps each, for example, would mean 160 amps to power the test board. A normal 1-oz. board requires 3-4 parallel layers, all acting as power and ground planes to provide that type of current. Extra layers drive up the board's cost and thickness and lower the reliability.
With currents as high as 400 amps, an engineer now has the ability to design one printed circuit board that can carry large currents and support the fine traces and features of the computer circuits needed to drive the high power. There is a varied arsenal of different heavy-copper technologies available to the engineer and designer to handle those tricky high-power, heat-sinking, burn-in board projects.
Some printed circuit companies manufacture multiple levels of heavy-copper printed circuit boards. "Multiple levels" means that on one layer, you can have 8 ounces of copper for the heavy tracks and 1 ounce of fine-featured traces for SMT circuitry, all interconnected and intertwined. In fact, up to 4 different copper thickness levels have been manufactured on one layer. The high-power circuits of today can contain from 1 to 8 layers with multiple levels of copper traces on those layers.
A few years ago, the notion that a printed circuit board could handle a large current in excess of 400 amps effectively was unheard of. Today, that reality not only exists but is flying in the skies every day, traveling our roads and running our power grids. Through years of research and experiments, heavy-copper technology slowly developed and perfected the high-power printed circuit board.
New methods have been developed and tested to create heavy-copper multilayers, buried copper, power circuits and multiple levels of copper on the same side. The result is an engineering system designed to handle just about any high-current situation imaginable. Typically, the heavy copper traces can be manufactured with 3-mil width per ounce of copper thickness.
The basic underlying principle is the ability to plate copper accurately up to 4 ounces thick when combined with the base starting copper. The combined heavy-copper traces allow large currents to be carried with little heat generated. Yes, the cost is higher for a heavy-copper printed circuit board, but so are the savings in other areas of the project--such as interconnect wires and assembly. What used to be attached mechanically off the circuit board through wire and terminal blocks and contained in large sheet-metal enclosures can now be conveniently located on the heavy-copper circuit board.
The most redeeming feature of the heavy-copper board is its ability to survive. It can withstand repeated over-current excursions, higher temperatures and repeated thermal cycling that would tear a normal printed circuit apart in a few cycles. The heavy copper circuit board can survive almost anything you can throw at it. Its ability to withstand high-level vibrations, such as those encountered on aircraft and space shuttles, has greatly impressed many design engineers at aircraft and aerospace vibration labs.
One drawback for the heavy-copper printed circuit has always been limited availability. Previously, printed circuit board shops would not even quote a double-sided board design over 3 ounces. A few facilities could scratch out an easy print-and-etch type of 4-oz. board, but nothing like the sophisticated heavy-copper circuits required today. Companies now are willing to fill that gap and will eagerly quote and produce your heavy-copper design.
A well-known problem with all printed circuit boards is thermal-cycle cracking of the plated through holes and vias. As temperatures cycle, the laminate expands and puts stress on the copper; eventually the copper work hardens, starts to crack and soon fails.
Sierra Proto Express experimented with a new approach to burn-in boards and now offers a super burn-in board. This new technology features a very high maximum operating temperature of 200* C with a Td of 360* C.
Although the super-board operating temperature is not as high as that of polyimide, most burn-in testing operates well below the 200* C mark. The super board has many other redeeming features that make its use beneficial.
To improve the thermal-cycling reliability of the burn-in boards, we utilize the new High.Rel high-reliability technology, so the burn-in boards exhibit superior thermal via cycle life of over 2000 cycles, compared with 300 cycles for a normal polyimide laminate.
We have also added heavy-copper technology to our burn-in boards with copper thicknesses of up to 8-oz. inner layers and 12-oz. outer layers. For more advanced boards, we also offer multilevels of copper, where the copper can be 8 ounces for the power section and 1 ounce for the signal traces, all on the same layer. The use of heavy-copper inner layers allows for thinner designs, fewer layers and better current distribution with less power-supply noise.
A new technology for burn-in boards is the thermal plane, where the inner layers are made with 4 to 8 ounces of copper to handle the higher current and to provide a highly conductive thermal heat-sinking plane. The thermal plane now replaces the metal-core board.
Our new super burn-in board is also lead-free compatible and certified.
Robert Tarzwell is director of R&D at Sierra Proto Express.
Ken Bahl is the CEO of Sierra Proto Express.
CLICK HERE to request additional info from Sierra Proto Express.
More Columns from Bob and Me
Controlled Impedance: A Real-World Look at the PCB SideBob and Me: The Key to Increasing Quality - Bribe Your Employees
Bob and Me: Tarzwell's First--and Last--Lean Meeting
Bob and Me: A PCB Potpourri
Bob and Me: Spacing is Irrelevant Below 270 Volts
PCB 101: Coefficient of Thermal Expansion
The Bleeding Edge: Serious as a Heart Attack
PCB101: Fabricating High-Voltage Boards