-
- News
- Books
Featured Books
- smt007 Magazine
Latest Issues
Current IssueSupply Chain Strategies
A successful brand is built on strong customer relationships—anchored by a well-orchestrated supply chain at its core. This month, we look at how managing your supply chain directly influences customer perception.
What's Your Sweet Spot?
Are you in a niche that’s growing or shrinking? Is it time to reassess and refocus? We spotlight companies thriving by redefining or reinforcing their niche. What are their insights?
Moving Forward With Confidence
In this issue, we focus on sales and quoting, workforce training, new IPC leadership in the U.S. and Canada, the effects of tariffs, CFX standards, and much more—all designed to provide perspective as you move through the cloud bank of today's shifting economic market.
- Articles
- Columns
- Links
- Media kit
||| MENU - smt007 Magazine
Estimated reading time: 4 minutes
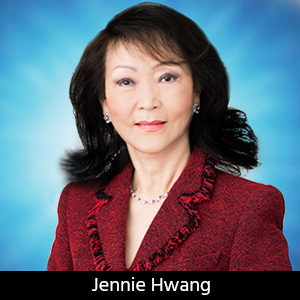
SMT Perspectives and Prospects: Can Microstructure Indicate a Good Solder Joint? Part IV
Editor's Note: This column originally appeared in the November 2012 issue of SMT Magazine.Continuing on the subject of solder joint microstructure, this month I would like to highlight the role of the phase diagram in microstructure, as a useful correlation between a solder joint microstructure and a phase diagram can be deduced. Once the phase diagram of a solder alloy is available, the characteristics of its microstructure can be derived. Focusing on applications for the packaging and assembly industry, the characteristics that are most relevant to solder joint performance are the eutectic behavior, solid solution, and intermetallic compounds, as well as the corresponding temperatures of formation of each of these characteristics.
Basics of Phase Diagram
When adding one element (solute) into another (solvent), the resulting alloy falls in one of the four following systems with the presence or absence of solid solution and/or intermetallic compounds:
- System with complete miscibility in solder and liquid states, such as CuNi, as shown in Figure 1.
- System with complete miscibility in liquid state and partial miscibility in solid state, as shown in Figure 2 of SnPb.
- System with complete miscibility in liquid state and no miscibility in solid state, e.g., AuSi.
- System containing intermetallic phases, e.g., SnAg, SnAu, as shown in Figures 3 and 4, respectively.
Figure 1: CuNi phase diagram. Figure 2: SnPb phase diagram.
Figure 3: SnAg phase diagram.
Figure 4: SnAu phase diagram. A solid solution will be formed when two elements having mutual solubility are mixed together. The crystal structure of the solvent remains unchanged and the mixture remains in a single homogenous phase. Thermodynamically, a metallurgical phase is a macroscopically homogenous and physically distinct portion of an alloy that has a given chemical composition and structure. Solid solution generally follows Hume-Rothery rules. Substitutional solid solutions are expected to form if the solute and solvent have:
- Similar atomic radii (15% or less difference);
- The same crystal structure;
- Similar electronegativities; and
- Similar valency.
Cu and Ni are mutually soluble at all concentrations, having unlimited solid solution creating a single phase alloy.
Sn and Pb have limited or partial solid solubility and SnPb does not meet the requirements of Hume-Rothery rules, resulting in a “two-phase alloy"--tin-rich phase and Pb-rich phase. In a system having more than one phase, each phase will have a unique chemical composition and will be different from the overall composition.
When an intermetallic compound (IMC) is formed, it is accompanied by a new crystal structure. The melting temperature of an intermetallic compound is always higher than the melting temperature of each element from which the IMC comes. SnAg and SnCu systems contain intermetallic compounds, so it is a SnAgCu (SAC) system. This is a main distinction between SAC solder and SnPb solder.
Construction of a Phase Diagram
A phase diagram shows the relationship among metallurgical phases, temperature, and composition. A two-dimensional, two-element phase diagram is expressed in a plot of relative amount of each element--in weight percent, atomic percent, or mole percent--at the horizontal axis and the temperature at the vertical axis.
Techniques to establish a phase diagram include the measurements of cooling curves or using other equipment and analysis: Differential scanning calorimetric, thermomechanical analysis, differential thermal analysis, metallography/petrography, energy-dispersive X-ray spectroscopy, X-ray diffraction and transmission electron microscopy. It is not a simple task to obtain a high-quality phase diagram; it is often quite time-consuming.
Usefulness of Phase Diagram
A phase diagram of an alloy system depicts the presence and absence of eutectic properties, solid solution, and intermetallic compounds. For a given alloy composition, a phase diagram can tell us the solidus temperature, the temperature at which the alloy is solid and at which liquefaction begins, and liquidus temperature, the temperature at which the alloy has become completely liquid. It can also reveal the maximum extent to which one element can diffuse into another at a given temperature.
Characteristics in the presence of phases, chemical composition of phases at a temperature of interest, and the amount of phases at a particular temperature can be obtained from the phase diagram of an alloy. When the temperature changes phase diagrams provide data and/or a hint about the likely development of microstructure and evolution of microstructure.
As examples, for the SnAg eutectic alloy, Sn grains and Ag3Sn precipitates are primary characteristics in microstructure. For the SnAgCu system, Sn grains, Ag3Sn precipitates and Cu6Sn5 precipitates are the primary characteristic phases.
Within an alloy system, the composition dependency of microstructure can also be revealed.
Does phase diagram have limitations? Yes, due primarily to the fact that phase diagrams are equilibrium diagrams. The rate of transformation is unaccountable. Nonetheless, much useful information can immensely facilitate the anticipation of microstructural characteristics which, in turn, helps predict solder joint mechanical behavior.
Dr. Hwang will present a lecture on “Preventing Assembly Defects and Failures” at IPC APEX EXPO, February 18, 2012, in San Diego, California.
Dr. Hwang, a pioneer and longstanding contributor to SMT manufacturing since its inception as well as to the lead-free development, has helped improve production yield and solved challenging reliability issues. Among her many awards and honors, she has been inducted into the WIT International Hall of Fame, elected to the National Academy of Engineering and named an R&D Stars to Watch. Having held senior executive positions with Lockheed Martin Corporation, Sherwin Williams Co., SCM Corporation and IEM Corporation, she is currently CEO of H-Technologies Group providing business, technology and manufacturing solutions. She is a member of the U.S. Commerce Department’s Export Council, and serves on the board of Fortune 500 NYSE companies and civic and university boards. She is the author of 300+ publications and several textbooks and an international speaker and author on trade, business, education and social issues. Contact her at (216) 577-3284; e-mail JennieHwang@aol.com.
More Columns from SMT Perspectives and Prospects
SMT Perspectives and Prospects: Warren Buffett’s Perpetual Wisdom, Part 1SMT Perspectives and Prospects: Artificial Intelligence, Part 5: Brain, Mind, Intelligence
SMT Perspectives and Prospects: Artificial Intelligence, Part 4—Prompt Engineering
SMT Perspectives and Prospects: The AI Era, Part 3: LLMs, SLMs, and Foundation Models
SMT Perspectives and Prospects: A Dose of Wisdom
SMT Prospects and Perspectives: AI Opportunities, Challenges, and Possibilities, Part 1
SMT Perspectives and Prospects: Critical Materials—A Compelling Case, Part 3
SMT Prospects and Perspectives: AI—A Prelude to Opportunities, Challenges and Possibilities