-
- News
- Books
Featured Books
- smt007 Magazine
Latest Issues
Current IssueWhat's Your Sweet Spot?
Are you in a niche that’s growing or shrinking? Is it time to reassess and refocus? We spotlight companies thriving by redefining or reinforcing their niche. What are their insights?
Moving Forward With Confidence
In this issue, we focus on sales and quoting, workforce training, new IPC leadership in the U.S. and Canada, the effects of tariffs, CFX standards, and much more—all designed to provide perspective as you move through the cloud bank of today's shifting economic market.
Intelligent Test and Inspection
Are you ready to explore the cutting-edge advancements shaping the electronics manufacturing industry? The May 2025 issue of SMT007 Magazine is packed with insights, innovations, and expert perspectives that you won’t want to miss.
- Articles
- Columns
- Links
- Media kit
||| MENU - smt007 Magazine
Estimated reading time: 5 minutes
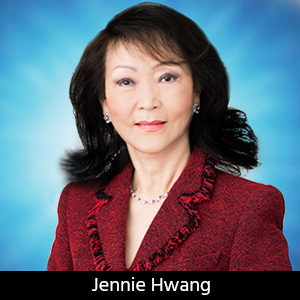
SMT Perspectives and Prospects: SAC System, A Revisit
Editor's Note: This article originally appeared in the February 2013 issue of SMT Magazine.
In compliance with the RoHS Directive initiated by the European Commission and later deployed globally, SAC305 (Sn3.0Ag0.5Cu) of SnAgCu (SAC) system has been used as a lead-free solder interconnection alloy for both second-level interconnection (e.g., IC packages) and the third-level interconnection (PCB board assembly) since the implementation of lead-free electronics.
Before the adoption of SAC305, other alloy systems outside SAC have been used (e.g., by lead-free pioneering Japanese electronics manufacturers in late 1990s). For a specific performance or other purposes, different alloys outside the SAC system have also been used in conjunction with SAC305 at OEMs’ discretion. Nonetheless, SAC system has become widely known and the most prevalent alloy system.
After a 10-year run, it is an opportune time to revisit SAC305, assessing its track record and its future.
SAC System
In addition to SAC305, the alloys within the SAC system have extended to various compositions during the past three years--some are far away from the composition of SAC305. Two approaches exist: One is adding doping elements to SAC305 with minor dosage shift in Ag or Cu or both; the other is reducing Ag content with minor shift of Cu content.
Compositions with Cu at 0.5 to 0.7% cover the range of Ag from 0.3 to 4.0%. Due to the near-eutectic nature of SAC305 (and SAC387, SAC405), the reduction of Ag from 3.0% results in an increase in melting temperature. The following table provides compositional examples and corresponding melting ranges (solidus and liquidus temperatures) in reference to SnCu eutectic, SnAg eutectic, and SnPb eutectic.Performance Within SAC System: Expected Versus Actual
What is the performance track record of SAC305 and what is the impact of changing to the compositions containing the reduced Ag content? Relative to performance, the manufacturing process in making solder interconnections and the resulting solder joints’ mechanical properties are two primary areas to be assessed.
SAC305 has performed to expectations, delivering satisfactory solder interconnections for most, but not all, application designs and service conditions, but with anticipated performance deficiencies. Specific deficiencies include the undesirable brittleness relative to SnPb counterpart and the potential occurrence of solder joint surface cracks.
One straightforward remedy to alleviate the brittleness of SAC305 is to reduce the Ag content, which consequently has lead to the introduction of low-Ag SAC alloy compositions. The compositions with reduced Ag content from the near-eutectic SAC305 result in an increased liquidus temperature. The increased liquidus temperature requires an increased process temperature in making interconnections at the package or board assembly level. Is the increase in process temperature a disadvantage? Yes, by any practical measures--all materials and components used in the assembly must have a higher temperature tolerance level in sync with the process temperature required.
As to mechanical properties of resulting solder joints, the yield strength, tensile strength, and creep resistance are expected to decrease with the reduction of Ag content. Within the ranges of Ag and Cu contents of this discussion, the fatigue resistance, which often involves more complex mechanisms, is also expected to decrease with the reduction of Ag content barring any extraneous factors.
Testing measurements coincide well with the expectations. For the effect of Ag content, at a range of 0.5 to 1.5% Cu, tests showed that yield strength and tensile strength increase almost linearly with Ag up to 4.1%; but its plasticity increases with decreasing Ag [1].
Despite some publications presented, the metallurgical principle stands. Test results show that the reduced Ag did not exhibit any downward performance. Lower strength is associated with lower Ag content. Apparently the reduced metal cost of the low-Ag compositions is an upside.
Relative Performance of SAC System Versus Non-SAC
What are the strengths and weaknesses of SAC system in comparison with non-SAC system for SMT applications? One appealing characteristic of SAC is its stability in relation to minor variations from the eutectic composition. Using the melting temperature as an example, the melting temperature of a near-eutectic composition is found to be not sensitive to the variation of Ag or Cu in the range of 0.5 to 1.5% Cu and Ag 3.0 to 4.1% Ag. Additionally, a good correlation exists between the mechanical properties and Ag content and Cu content, respectively.
Focusing on process requirements, it should be noted that the lowest melting temperature that the SAC system can achieve is 217°C. A superior system to SAC needs to carry a lower melting temperature than that of SAC305--desirably at a liquidus temperature between 183°C to 210°C. To achieve this lower liquidus temperature, it will have to resort to a quaternary alloy system.
Further, the intrinsic wetting ability of SAC system does not measure up to that of SnPb or SnCu. With SAC305’s high liqiudus temperature, the tendency to use a process temperature below the desired temperature often leads to a marginal process, which aggravates the SAC305’s lower wetting ability. In production, a marginal process should be avoided since it often causes production defects.
Reference:
1. Dr. Jennie S. Hwang, “Environment-friendly Electronics - Lead-free Technology,” Chapter 8, Electrochemical Publications, Great Britain, ISBN-0 901 150 401.
Dr. Hwang, a pioneer and longstanding contributor to SMT manufacturing since its inception as well as to the lead-free development, has helped improve production yield and solved challenging reliability issues. Among her many awards and honors, she has been inducted into the WIT International Hall of Fame, elected to the National Academy of Engineering and named an R&D Stars to Watch. Having held senior executive positions with Lockheed Martin Corporation, Sherwin Williams Co., SCM Corporation and IEM Corporation, she is currently CEO of H-Technologies Group providing business, technology and manufacturing solutions. She is a member of the U.S. Commerce Department’s Export Council, and serves on the board of Fortune 500 NYSE companies and civic and university boards. She is the author of 350+ publications and several textbooks and an international speaker and author on trade, business, education and social issues. Her formal education includes four academic degrees, as well as the Harvard Business School Executive Program and Columbia University Corporate Governance Program. Contact her at (216) 577-3284; e-mail JennieHwang@aol.com.
More Columns from SMT Perspectives and Prospects
SMT Perspectives and Prospects: Artificial Intelligence, Part 5: Brain, Mind, IntelligenceSMT Perspectives and Prospects: Artificial Intelligence, Part 4—Prompt Engineering
SMT Perspectives and Prospects: The AI Era, Part 3: LLMs, SLMs, and Foundation Models
SMT Perspectives and Prospects: A Dose of Wisdom
SMT Prospects and Perspectives: AI Opportunities, Challenges, and Possibilities, Part 1
SMT Perspectives and Prospects: Critical Materials—A Compelling Case, Part 3
SMT Prospects and Perspectives: AI—A Prelude to Opportunities, Challenges and Possibilities
SMT Perspectives and Prospects: Pearls of Wisdom