-
- News
- Books
Featured Books
- pcb007 Magazine
Latest Issues
Current IssueIn Pursuit of Perfection: Defect Reduction
For bare PCB board fabrication, defect reduction is a critical aspect of a company's bottom line profitability. In this issue, we examine how imaging, etching, and plating processes can provide information and insight into reducing defects and increasing yields.
Voices of the Industry
We take the pulse of the PCB industry by sharing insights from leading fabricators and suppliers in this month's issue. We've gathered their thoughts on the new U.S. administration, spending, the war in Ukraine, and their most pressing needs. It’s an eye-opening and enlightening look behind the curtain.
The Essential Guide to Surface Finishes
We go back to basics this month with a recount of a little history, and look forward to addressing the many challenges that high density, high frequency, adhesion, SI, and corrosion concerns for harsh environments bring to the fore. We compare and contrast surface finishes by type and application, take a hard look at the many iterations of gold plating, and address palladium as a surface finish.
- Articles
- Columns
Search Console
- Links
- Media kit
||| MENU - pcb007 Magazine
Estimated reading time: 1 minute
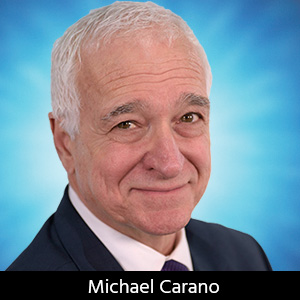
Contact Columnist Form
Trouble in Your Tank: PTH Voids: Getting to the Root Cause, Part 3
Critical Electroless Copper Pre-plate Preparation
Recognizing that the surface topography created after desmear is less than optimum (compared to lower-Tg materials), more attention must be directed to electroless copper pre-plate chemistry. First, ensuring sufficient coverage and distribution of the catalyst is a critical success factor. Basically, sufficient concentration of the palladium catalyst on the hole wall provides nucleation sites with which to initiate the deposition of copper. When a high surface topography is available, the catalyst is more readily able to adsorb onto the resin. However, the higher performance materials (as previously stated) are more chemically resistant to alkaline permanganate chemistry. Thus, there is less topography and by default, less catalyst adsorption.
To counter this effect, new cleaner/conditioners must be utilized to enhance catalyst adsorption. The key is to improve the flocculation of the catalyst to the hole wall as well as the adhesion (resin and glass) without building excessive thickness on the copper interconnects. Thus, the cleaner/conditioner acts as an adsorption modifier. These cationic polymers are believed to either change the charge density of the surface and/or provide chemical bonds for attracting the catalytic species. To further complicate the issue, the author believes that different types of surfactants are more beneficial than others with respect to adhesion of the plated copper. Why is this critical? This is critical, based on the fact that excessive copper thickness or too rapid of a plating deposition rate can lead to reduced adhesion. While the high plating rates may guarantee perfect void-free coverage, there is no guarantee that adhesion will not be compromised. It has been demonstrated over and over that a slow and even deposition rate will not only give excellent coverage of copper on the most difficult to metalize substrates, but will ensure better adhesion as well.
At the very outset, it was stated that achieving excellent adhesion on these substrates is made more difficult. Thus, providing an electroless process that promotes excellent coverage and adhesion is achievable. From a chemical standpoint, this means understanding the relationship between adhesion, plating rates and catalyst adsorption.
Editor's Note: This column originally appeared in the August 2013 issue of The PCB Magazine.
More Columns from Trouble in Your Tank
Trouble in Your Tank: Yield Improvement and ReliabilityTrouble in Your Tank: Causes of Plating Voids, Pre-electroless Copper
Trouble in Your Tank: Organic Addition Agents in Electrolytic Copper Plating
Trouble in Your Tank: Interconnect Defect—The Three Degrees of Separation
Trouble in Your Tank: Things You Can Do for Better Wet Process Control
Trouble in Your Tank: Processes to Support IC Substrates and Advanced Packaging, Part 5
Trouble in Your Tank: Materials for PWB Fabrication—Drillability and Metallization
Trouble in Your Tank: Supporting IC Substrates and Advanced Packaging, Part 5