-
- News
- Books
Featured Books
- pcb007 Magazine
Latest Issues
Current IssueInventing the Future with SEL
Two years after launching its state-of-the-art PCB facility, SEL shares lessons in vision, execution, and innovation, plus insights from industry icons and technology leaders shaping the future of PCB fabrication.
Sales: From Pitch to PO
From the first cold call to finally receiving that first purchase order, the July PCB007 Magazine breaks down some critical parts of the sales stack. To up your sales game, read on!
The Hole Truth: Via Integrity in an HDI World
From the drilled hole to registration across multiple sequential lamination cycles, to the quality of your copper plating, via reliability in an HDI world is becoming an ever-greater challenge. This month we look at “The Hole Truth,” from creating the “perfect” via to how you can assure via quality and reliability, the first time, every time.
- Articles
- Columns
- Links
- Media kit
||| MENU - pcb007 Magazine
Estimated reading time: 13 minutes
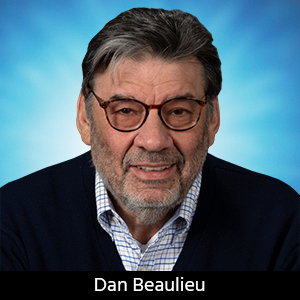
Conversations with...HSIO President Jim Rathburn
These are exciting times in our industry, as new technologies and processes are being developed by new companies. HSIO is one of these new companies. First, let’s talk about what HSIO is not. It is not a PCB company. This company does not build circuit boards, but, rather, invents and develops process technologies for the interconnect market. In other words, HSIO’s actual mission is to develop customer technologies to meet today’s challenges.
I sat down with the company’s founder and President Jim Rathburn to discuss the new LCP PCB process his company has developed. Fasten your seatbelt and take a ride into the future of the interconnect industry.
Dan Beaulieu: Jim, it's good to talk with you again. Tell our readers a little about yourself.
Jim Rathburn: Okay. Good talking to you as well, by the way. My background is mechanical engineering and manufacturing, with experience in the semiconductor and system hardware segments of the industry. I worked my way into the industry as a mechanical designer, and was fortunate to find a niche in the electrical interconnect industry that leveraged my manufacturing background. I founded a high-speed connector and socket company by the name of Gryphics, Inc. where we grew to the point of sale to Cascade Microtech in 2007. With the connector and socket business, we focused on high speed products used for test and development of packaged silicon, with Cascade focused on wafer level test.As our customers advanced to finer technology nodes, I found that even if the socket, connector, or wafer probe was tuned for high performance the circuit boards and packages mating with our products were becoming a signal integrity bottleneck. My role at HSIO is focused on improving that signal channel through the various circuits, connectors and components our customers use to develop, validate and deploy silicon to the market.
Beaulieu: So HSIO is basically a technology company that develops specific, purpose-driven technology for interconnect applications.
Rathburn: That's correct.
Beaulieu:: Wow, this is an entirely different approach to our business. Let’s talk about your company. What does HSIO stand for?
Rathburn: HSIO stands for High Speed Input Output. As the name implies, we are focused on high-speed applications and aim to be the company customers think of when they have a high-speed application.
Beaulieu: How did this company get started and what exactly do you do?
Rathburn: HSIO began operations in 2010 at a development facility located in Maple Grove, Minnesota. Our mission was to develop new, exciting, and proprietary technology to address high-density and high-speed interconnect challenges faced by our customers and the semiconductor industry. We interviewed the leading silicon companies and asked what challenges faced would benefit from new technology not restricted by legacy fabrication techniques, but would leverage conventional manufacturing processes. The common theme was next-generation silicon packaging will continue to increase performance and density requiring finer lines and spaces, with signal integrity through the entire interconnect channel of major concern, with vias becoming a problem. Another common theme was the silicon packaging density capability was advancing faster than the printed circuit capability used to produce the PCBs to which the chips were mounted. As chip packaging reduced terminal pitch, the PCB industry was struggling with routing density driven by the fine pitch packaging. Related to the routing density issues are the layer to layer vertical interconnect and via structures which have become a major issue with signal loss and production yield. We established a large IP portfolio focused on each interconnect point within the signal channel and invested significant resources towards developing high-speed, high-density printed circuit and connector technology in concert with our customers with production processes and cost in mind. We are now commercializing the technologies developed with significant support of our customer base.
Beaulieu: Tell us about your new technology, LCP PCB.
Rathburn: As I mentioned earlier, I found that no matter how good a signal passes through a socket or connector, the PCB technology was a problem with high frequency signals. The conventional PCB material set also became a limiting factor with regard to reducing line size and space and accurately matching impedance. In the connector industry, liquid crystal polymer has become the material of choice for high-density, high-speed products produced in high volume and is usually injection molded to create the insulator housings. For high-speed applications, inductance and capacitance, and impedance match are a big deal with shielding for cross talk has become a major challenge. Connector suppliers have transitioned to adding metal shielding techniques to reduce cross talk, and HSIO focused on ways to metalize the polymers in a selective manor along with altering the dielectric properties of the material set to tune impedance and reduce signal loss while improving cross talk issues. These principles were extended to printed circuits as well, focused on liquid dielectrics and LCP material which has several properties that are well suited to high-speed, high-density circuits in flexible and rigid forms. LCP has a low dielectric constant of 2.9 and is virtually impermeable to moisture. It is available in multiple melting temperatures, can be used in molded, film, or cast resin formats. It also can be filled with materials to alter the mechanical or electrical properties, and is stable at reflow temperatures. One interesting property that we focused on is LCP can be processed in a way where the material will fusion bond to itself. The ability to create thin dielectric layers in the 15 to 100 micron range with low constant value that can be fusion bonded to each other was a key to achieving a tight impedance profile matched well with fine lines and spaces in the 15-100 micron range. We combine various additive and subtractive processes to create the fine line circuitry, and fusion bond the layers together using the LCP material as the bonding agent as well as the dielectric separation. We also have some interesting ways leveraging the packaging world to create the vertical via interconnect from layer to layer with solid copper columns in the 20 to 100 micron range that grow from one metal layer to the next. Once the multilayer stack is fusion bonded, the vias and the circuits are completely surrounded by a near hermetic common dielectric constant with no glass weave, resulting in a very high-density matrix with excellent impedance match and low loss. To further the signal integrity all the way to the SMT surface, we create a final LCP surface with essentially metal defined pads where the LCP material serves as mask and conventional very “lossy” solder mask is eliminated. We have heard the term via-in-pad, while the process described results in a structure where the via-is-the-pad in some respects which reduces registration issues. Since LCP can be used as a flexible alternative to polyimide, the natural construction can be used as a very high speed flex circuit on its’ own. For multilayer rigid applications, we use rigid cores of conventional construction with high speed, very thin LCP “skins” for signal layers creating a hybrid high-density/low-density integration.
Beaulieu: I read your recent white paper on this technology and, I have to say, the benefits seem too good to be true. Talk about those lines and spacing below 50 micron. Is signal integrity beyond 40 GHZ to come next?
Page 1 of 4
More Columns from It's Only Common Sense
It’s Only Common Sense: Why Failure Is an Opportunity for GrowthIt’s Only Common Sense: Stop Chasing New Customers and Start Keeping the Ones You Have
It’s Only Common Sense: Sales as a Team Sport
It’s Only Common Sense: How to Win Back Lost Customers
It’s Only Common Sense: Knowing When to Walk Away
It’s Only Common Sense: Customer Service Is Sales in Disguise
It’s Only Common Sense: Your Guide to Better Time Management
It’s Only Common Sense: Selling to Today's Generation of Buyers