Are There Advantages to Changing Your Registration System?
March 22, 2015 | Barry Matties, I-Connect007Estimated reading time: 9 minutes
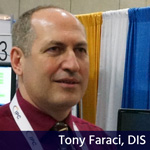
I recently had a conversation with DIS's Tony Faraci at IPC APEX EXPO 2015, to learn more about their pinless registration system. What was most interesting to me are the potential advantages a pinless system offers and if so, why the process has not been widely adopted.
Barry Matties: Hello, Tony. Thanks for sitting down with me today. Could you please tell us about the DIS pinless registration system?
Tony Faraci: Yes, thanks, Barry. What is happening with this type of a system, as opposed to a conventional pin lamination technology, is that we are optically aligning all the internal layers of a panel. Conventional wisdom used to be that you would post-etch punch all your cores and then pin. Now, you are eliminating that whole process. You are eliminating pinning, you're eliminating all of that punching and all of that pin tooling and now we are optically aligning all the layers and tack bonding them together.
By optically aligning, all those mechanical pin tolerances are eliminated, and of course you are not limited to certain panel sizes. The layers are aligned optically and then we use an induction bonding system that actually bonds the layers together. The advantage here is that the registration can be checked before lamination, which really can't be done with any type of pinning system.
You can kind of do it with a riveting system, let's say, or eyelets, but with this type of system, now you can check your registration before going into the lamination press, then you laminate the panel, come out, and now you can again check the registration of that panel. Having the data immediately before and after lamination can show what's happening inside the press.
Besides this valuable data set, this is also telling you what our system is doing. It's giving you an overall view at different points of the process which they've never been able to do before. You can kind of do it with a riveting system but you're not going to do such high layer counts and it will not be repeatable. So DIS pinless technology is the next step up from pin because it eliminates all those mechanical problems.
Matties: For those who already have a pin system in place, are there any special processes or changes that they have to make?
Faraci: It changes a little bit in the process. What you're doing is using similar targets like they do on a punching machine, but now they are adding these welding coupons. They are just a quarter-inch by three-quarter-inch solid copper pads at four points on the panel that we'll use to tack bond.
Where it really changes is the reduced handling and lay-up. The machine is basically an optical lay-up machine, so instead of handling the panel once at post-etch punch and then going through oxide or oxide alternative, where there is some more stretching of the layer, and then laying up on mechanical pins, where most of the bulk error is, we’re only handling it once, at optical lay-up.
We're not selling a product that's competing against the post-etch punch; it's a process change. It eliminates that pin-up process and instead is optically aligning the layers; this really is the biggest change.
It's a little bit different in the process, so there is a learning curve. But the benefit for the customer is great, because now they can start looking at what's happening in the press. Today, most high-end shops work with pins, so what do they do, they lay up a book and you don't know if there's a shift -did it happen at lay-up, did it happen in the press, did it happen at transport?
So, that's one of the biggest changes. Another product that we developed about six years ago was a multi-camera system that allows us to check the layers front to back, in order to figure out where the best fit positions are for that layer. That also works well with our systems, because that data gets captured and it goes into our alignment systems.
Matties: How does that benefit?
Faraci: Let's say a customer is running higher-end boards. They can, if they have an LDI process for example, print a 2D bar code on every layer, serialize the core, and then our multi-camera system can actually measure that core and capture the positional data. And of course it's tied to that serial number.
Then when it gets to our alignment machines, they read that barcode and they know the positional data of that core, based on the eight targets, and now we can process the panel. So it enables all our existing two-camera machines—for example, what they have at DSG—once customers buy this unit, they’re able to have it work like an eight-camera system. Or you could use it off line just to measure panels to make sure that the layers are within tolerance before you use them at lay-up.
Matties: So, with your system the border is now smaller?Page 1 of 2
Testimonial
"Advertising in PCB007 Magazine has been a great way to showcase our bare board testers to the right audience. The I-Connect007 team makes the process smooth and professional. We’re proud to be featured in such a trusted publication."
Klaus Koziol - atgSuggested Items
How Good Design Enables Sustainable PCBs
08/21/2025 | Gerry Partida, Summit InterconnectSustainability has become a key focus for PCB companies seeking to reduce waste, conserve energy, and optimize resources. While many discussions on sustainability center around materials or energy-efficient processes, PCB design is an often overlooked factor that lies at the heart of manufacturing. Good design practices, especially those based on established IPC standards, play a central role in enabling sustainable PCB production. By ensuring designs are manufacturable and reliable, engineers can significantly reduce the environmental impact of their products.
50% Copper Tariffs, 100% Chip Uncertainty, and a Truce
08/19/2025 | Andy Shaughnessy, I-Connect007If you’re like me, tariffs were not on your radar screen until a few months ago, but now political rhetoric has turned to presidential action. Tariffs are front-page news with major developments coming directly from the Oval Office. These are not typical times. President Donald Trump campaigned on tariff reform, and he’s now busy revamping America’s tariff policy.
Global PCB Connections: Understanding the General Fabrication Process—A Designer’s Hidden Advantage
08/14/2025 | Markus Voeltz -- Column: Global PCB ConnectionsDesigners don’t need to become fabricators, but understanding the basics of PCB fabrication can save you time, money, and frustration. The more you understand what’s happening on the shop floor, the better you’ll be able to prevent downstream issues. As you move into more advanced designs like HDI, flex circuits, stacked vias, and embedded components, this foundational knowledge becomes even more critical. Remember: the fabricator is your partner.
MKS’ Atotech to Participate in IPCA Electronics Expo 2025
08/11/2025 | AtotechMKS Inc., a global provider of enabling technologies that transform our world, announced that its strategic brands ESI® (laser systems) and Atotech® (process chemicals, equipment, software, and services) will showcase their latest range of leading manufacturing solutions for printed circuit board (PCB) and package substrate manufacturing at the upcoming 17th IPCA Show to be held at Pragati Maidan, New Delhi from August 21-23, 2025.
MKS Showcases Next-generation PCB Manufacturing Solutions at the Thailand Electronics Circuit Asia 2025
08/06/2025 | MKS Instruments, Inc.MKS Inc, a global provider of enabling technologies that transform our world, today announced its participation in Thailand Electronics Circuit Asia 2025 (THECA 2025), taking place August 20–22 at BITEC in Bangkok.