Multek CTO Excited About the Challenges of the Fast-Moving Wearables Market
March 26, 2015 | Barry Matties, I-Connect007Estimated reading time: 9 minutes
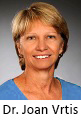
At IPC APEX EXPO 2015, held in San Diego, Calif. I had the opportunity to sit with Dr. Joan Vrtis to discuss the rapidly evolving wearables market, especially for medical, and the myriad questions that must be addressed. We also touched on Multek’s contribution to the wearables industry and what it sees as the main challenges to putting their circuits into various applications.
Barry Matties: Good morning, Joan. Why don't you start by telling me a little bit about what's that like being chief technology officer at Multek. I understand it is a recent position. Congratulations!
Dr. Joan Vrtis: Thank you very much. Multek is an industry leader in printed circuit technology, and the wholly owned subsidiary of Flextronics. As the chief technology officer, I’m looking at the wearable technology and how we can put our printed circuits into applications. So for Multek, it's really the solutions of what we can offer on the printed circuit side, whether it's a rigid circuit, a flex circuit, a rigid-flex and even things that can stretch and bend. We must be prepared for the broad markets we serve, specifically in the wearables. That's currently where I've been putting most of my effort.
Matties: Wearables is a fast-moving market, isn't it?
Vrtis: Yes, it is.
Matties: What is the state of the market as you see it, currently?
Vrtis: One of the things we've seen just recently is the expansion of the number of ideas as to what should be a wearable. How do we help translate these ideas to product and how do we market them? Some trends regarding wearables are in close proximity to the body, on the body and in the body. For example, the wristband type of technologies, such as activity band, watch, smart watch. Then there are the wearables on skin, which includes patch-like technologies used for authentication. Now, wearables ideas are growing, as inventors and companies look at putting electronics into a fabric. Can the button be used as the connection for the continuity of the circuit? Can the zipper be part of the solution to turn on and off the electronics if placed in a safety jacket? How do we integrate the components that go with that? We have to consider power, wireless, etc. And if you want something that's going to move—a gyroscope, or accelerometer—how do we put all of these components in and how do we select those components?
On the printed circuit side, historically we're used to circuit boards being like 2D structures, thus they would be flat, and then we would place the components on and go. But now we also have to take into account that they're going to bend and move. When it starts getting into the apparel side, do you make that cloth fabric your printed circuit substrate? Those are the things that people are coming to us with and saying, “Hey, can you guys do apparel?” But what does that mean? Are you going to wash it? There are a lot of questions to ask.
Matties: With the power technology in apparel and wearables, certainly washing must be a big issue.
Vrtis: Yes, it is a big issue, as is drying.
Matties: What's the craziest thing that someone has approached you with?
Vrtis: Let's see. I've had some very interesting requests for solutions with the printed circuit, but the craziest probably doesn’t need to be recorded here.
Matties: That’s okay; we can leave it to the imagination.
Vrtis: The important thing is that they needed all of the same components I have been talking about. They needed power and they needed some way to have this wireless to connect.
Matties: Let's talk about the market a little bit. What's the size of the market right now, the way you are seeing it?
Vrtis: Wow, it's in the billions! I’ve read eight billion is predicted in the next couple of years.
Matties: Where was that just a few years back?
Page 1 of 2
Testimonial
"In a year when every marketing dollar mattered, I chose to keep I-Connect007 in our 2025 plan. Their commitment to high-quality, insightful content aligns with Koh Young’s values and helps readers navigate a changing industry. "
Brent Fischthal - Koh YoungSuggested Items
How Good Design Enables Sustainable PCBs
08/21/2025 | Gerry Partida, Summit InterconnectSustainability has become a key focus for PCB companies seeking to reduce waste, conserve energy, and optimize resources. While many discussions on sustainability center around materials or energy-efficient processes, PCB design is an often overlooked factor that lies at the heart of manufacturing. Good design practices, especially those based on established IPC standards, play a central role in enabling sustainable PCB production. By ensuring designs are manufacturable and reliable, engineers can significantly reduce the environmental impact of their products.
50% Copper Tariffs, 100% Chip Uncertainty, and a Truce
08/19/2025 | Andy Shaughnessy, I-Connect007If you’re like me, tariffs were not on your radar screen until a few months ago, but now political rhetoric has turned to presidential action. Tariffs are front-page news with major developments coming directly from the Oval Office. These are not typical times. President Donald Trump campaigned on tariff reform, and he’s now busy revamping America’s tariff policy.
Global PCB Connections: Understanding the General Fabrication Process—A Designer’s Hidden Advantage
08/14/2025 | Markus Voeltz -- Column: Global PCB ConnectionsDesigners don’t need to become fabricators, but understanding the basics of PCB fabrication can save you time, money, and frustration. The more you understand what’s happening on the shop floor, the better you’ll be able to prevent downstream issues. As you move into more advanced designs like HDI, flex circuits, stacked vias, and embedded components, this foundational knowledge becomes even more critical. Remember: the fabricator is your partner.
MKS’ Atotech to Participate in IPCA Electronics Expo 2025
08/11/2025 | AtotechMKS Inc., a global provider of enabling technologies that transform our world, announced that its strategic brands ESI® (laser systems) and Atotech® (process chemicals, equipment, software, and services) will showcase their latest range of leading manufacturing solutions for printed circuit board (PCB) and package substrate manufacturing at the upcoming 17th IPCA Show to be held at Pragati Maidan, New Delhi from August 21-23, 2025.
MKS Showcases Next-generation PCB Manufacturing Solutions at the Thailand Electronics Circuit Asia 2025
08/06/2025 | MKS Instruments, Inc.MKS Inc, a global provider of enabling technologies that transform our world, today announced its participation in Thailand Electronics Circuit Asia 2025 (THECA 2025), taking place August 20–22 at BITEC in Bangkok.