-
- News
- Books
Featured Books
- smt007 Magazine
Latest Issues
Current IssueIntelligent Test and Inspection
Are you ready to explore the cutting-edge advancements shaping the electronics manufacturing industry? The May 2025 issue of SMT007 Magazine is packed with insights, innovations, and expert perspectives that you won’t want to miss.
Do You Have X-ray Vision?
Has X-ray’s time finally come in electronics manufacturing? Join us in this issue of SMT007 Magazine, where we answer this question and others to bring more efficiency to your bottom line.
IPC APEX EXPO 2025: A Preview
It’s that time again. If you’re going to Anaheim for IPC APEX EXPO 2025, we’ll see you there. In the meantime, consider this issue of SMT007 Magazine to be your golden ticket to planning the show.
- Articles
- Columns
Search Console
- Links
- Media kit
||| MENU - smt007 Magazine
How to Select an Automatic Pick-and-Place Machine
April 15, 2015 | Robert Voigt, DDM NovastarEstimated reading time: 2 minutes
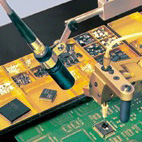
This is the third in a series of articles designed to help buyers analyze and select SMT equipment for PCB assembly, and examines automatic pick-and-place machines, the most complex component in a circuit assembly operation. Because of this complexity, the next few columns will address different functions in this process.
Automatic pick-and-place machines are much more common than manual or semiautomatic machines, but they also have the greatest range of capabilities and cost. This column will focus on features and capabilities and include some cautions regarding reliability of low-cost machines, including:
• Production volume ranges (CPH)
• Accuracy and repeatability specs
• Pick-up and centering methods
In future columns, I will address size, machine accuracy, encoders, feeders and mechanical positioning methods.
When starting your evaluation process, there are two defining factors to keep in mind, which determine what category fits your machine needs. The No. 1 principal factor is components per hour (CPH), and the secondary factor is machine capability.
Production Volume
As in the previous column, it’s constructive to start by addressing production ranges for various types of machines, since this is the No. 1 factor in your evaluation process. For purposes of comparison, since all circuit boards vary in size and complexity, we talk about volumes in terms of components per hour, or CPH. The following table offers a general guideline of machine categories defined by their CPH.
Machine Capabilities
This is the second defining factor in helping choose the correct auto pick-and-place machine for your needs. Here, we will only be talking about two aspects of machine capability: accuracy and repeatability, and pick-and-place centering methods.
Accuracy and Repeatability
For production machines, we typically recommend looking for a machine with accuracy of +/- .0001” and down to fine pitch capability of 12 mil on a repeated basis. Less expensive machines often don’t meet this spec. Most low-cost machines will also not come standard with a computer or software which could help with the repeatability aspects if not the accuracy. While some may offer enhanced technology, most do not.
Pick-and-place Centering Methods
There are four methods for pick-up and placement:
1. No centering mechanism
2. Mechanical (jaws)
3. Laser centering
4. Vision centering
Method 1: No centering mechanism other than relying on the component’s pick-up point for placement. In other words, the part is not physically centered after being picked up by the tool head, and if it’s picked off-center on the tool, it will be off-center when placed on the board. Obviously, this is not a very accurate placement method because there is no definable tolerance. You can expect to find this method used by hobbyists or instructors, but certainly not in any type of precision production environment. There are not many options available either, and long-term reliability is questionable.
• Pros: Low cost
• Cons: Low accuracy, repeatability and long-term reliability, no options, or spare parts
• Size range: No definable tolerances
Editor's Note: This article originally appeared in the March issue of SMT Magazine.
Suggested Items
Localized Automation Becomes a Tariff Storm Safe Haven, but U.S. Smart Factory Build-Out Costs Far Exceed China’s
05/09/2025 | TrendForceTrendForce’s latest “Human-Machine Technology Report” points out that although the 90-day delay on the U.S. reciprocal tariffs announced by the Trump administration in early April 2025 offers temporary relief, it has already triggered lasting shifts in global manufacturing and supply chain strategies.
NXP Unveils Third-Generation Imaging Radar Processors for Level 2+ to 4 Autonomous Driving
05/09/2025 | NXP SemiconductorNXP Semiconductors N.V. unveiled its new S32R47 imaging radar processors in 16 nm FinFET technology, building on NXP’s proven expertise in the imaging radar space.
Dan’s Biz Bookshelf: ‘Growth Hacker Marketing’
05/08/2025 | Dan Beaulieu -- Column: Dan's Biz BookshelfSometimes, a book comes along that challenges everything you thought you knew about your profession. For those in marketing, PR, or advertising, Ryan Holiday’s "Growth Hacker Marketing: A Primer on the Future of PR, Marketing, and Advertising" is that book. It’s a powerful manifesto for a new era of marketing.
Panel Driver IC Price Decline Slows in 1H25; Gold Prices, China Subsidies, and U.S.-China Tariffs Emerge as Key Variables
04/28/2025 | TrendForceTrendForce’s latest investigation finds that China’s subsidy policies and rising concerns over reciprocal tariffs are reshaping brand strategies in the panel market, indirectly influencing price trends for panel driver ICs.
New IDTechEx Report Examines How QLC SSDs Are Disrupting the HDD Storage Market
04/24/2025 | PRNewswireFor enterprises, data storage is not just a technical challenge but a financial one. The new report from market intelligence firm IDTechEx, "Emerging Memory and Storage Technology 2025-2035: Markets, Trends, Forecasts", provides an in-depth analysis of the evolving storage landscape and its impact on cost, efficiency, and scalability.