iNEMI Managing Director: New, Disruptive Technology on the Horizon
May 28, 2015 | Barry Matties, I-Connect007Estimated reading time: 3 minutes
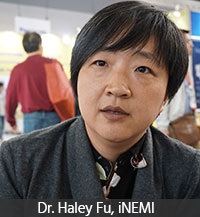
Dr. Haley Fu, managing director of Asia Pacific for iNEMI, gives her overview of the last eight years with iNEMI along with her opinion of what the most significant changes have been, globally and for the Asia market in particular.
Barry Matties: Dr. Fu, you are the managing director of Asia Pacific for iNEMI, and you have been with the organization for nearly eight years. Can you start by giving us an overview of the changes that you've seen in this industry? What things stand out the most?
Dr. Haley Fu: That's a difficult question to answer, but first of all in the global market, Korean companies, like Samsung, have been doing very well and Japanese electronics is probably down a bit. Even for China, some local companies like Xiaomi or Huawei have grown very fast and the market has changed quickly.
Several years ago there were huge changes for mobile phones at companies like HTC, and they grew quickly. Consumers of portable products are extremely dynamic, according to our recently released roadmap for portable and wireless devices. But for the next 10 years perhaps, the gross may reduce by 1-2%, which means maybe people won’t upgrade their product as fast as it evolves. Everybody has a smartphone, right? But some functions can be implemented by software and apps and don’t require a new phone. So many people will still change, but at a slower pace.
Matties: For example, here in Asia, it's not just that people are changing, but new users are coming up as well. That number has historically been very high, on an annual basis. Do you see that number declining as well for new users?
Fu: I think the numbers will increase, but maybe at a slower speed.
Matties: You were talking about things that people should be aware of right now. What is it that people should be aware of in this market?
Fu: For the technology side, there is some fundamental research work going on with materials and even some innovative new architecture based on these materials. Because the materials and the design of the components integrate so many functions, they pull and push the materials nearly to the limits of their properties. I think new, disruptive technology will be developed and that knowledge will be seen based on some fundamental research work on the material side.
Actually, this year, iNEMI started working with MIT on a program for using microphotonics in technical manufacturing. In the future, the PCB will probably adopt optical architectures instead of copper, because using copper for the trace means that the land space and the property will not satisfy the future high-speed data transport rate.
Matties: TTM is working on that, right? They were estimating it is still two or three years away.
Fu: Yes, that's true. It will require change everywhere, from the system architecture design to the materials and the manufacturing process; a lot of change needs to happen. It means that the industry has to develop a roadmap for how to get there. On the other hand, if we do it for high-volume manufacturing, there should be lower cost. The problem is that it's too expensive to develop. That's basically one trend that we will probably see in the future, but I don’t know how many years it will take.
Matties: What you are saying is that there is demand for change right now, with regard to the material needed for the application.
Fu: Yes, for both materials and the applications. The industry needs to get the supply chain in place to implement it.
Matties: That is all very interesting. Thank you for talking with us today.
RELATED CONTENT:
Optical Interconnects, a column from Karl Dietz
An Optical Update with TTM, by Barry Matties
Testimonial
"Our marketing partnership with I-Connect007 is already delivering. Just a day after our press release went live, we received a direct inquiry about our updated products!"
Rachael Temple - AlltematedSuggested Items
How Good Design Enables Sustainable PCBs
08/21/2025 | Gerry Partida, Summit InterconnectSustainability has become a key focus for PCB companies seeking to reduce waste, conserve energy, and optimize resources. While many discussions on sustainability center around materials or energy-efficient processes, PCB design is an often overlooked factor that lies at the heart of manufacturing. Good design practices, especially those based on established IPC standards, play a central role in enabling sustainable PCB production. By ensuring designs are manufacturable and reliable, engineers can significantly reduce the environmental impact of their products.
50% Copper Tariffs, 100% Chip Uncertainty, and a Truce
08/19/2025 | Andy Shaughnessy, I-Connect007If you’re like me, tariffs were not on your radar screen until a few months ago, but now political rhetoric has turned to presidential action. Tariffs are front-page news with major developments coming directly from the Oval Office. These are not typical times. President Donald Trump campaigned on tariff reform, and he’s now busy revamping America’s tariff policy.
Global PCB Connections: Understanding the General Fabrication Process—A Designer’s Hidden Advantage
08/14/2025 | Markus Voeltz -- Column: Global PCB ConnectionsDesigners don’t need to become fabricators, but understanding the basics of PCB fabrication can save you time, money, and frustration. The more you understand what’s happening on the shop floor, the better you’ll be able to prevent downstream issues. As you move into more advanced designs like HDI, flex circuits, stacked vias, and embedded components, this foundational knowledge becomes even more critical. Remember: the fabricator is your partner.
MKS’ Atotech to Participate in IPCA Electronics Expo 2025
08/11/2025 | AtotechMKS Inc., a global provider of enabling technologies that transform our world, announced that its strategic brands ESI® (laser systems) and Atotech® (process chemicals, equipment, software, and services) will showcase their latest range of leading manufacturing solutions for printed circuit board (PCB) and package substrate manufacturing at the upcoming 17th IPCA Show to be held at Pragati Maidan, New Delhi from August 21-23, 2025.
MKS Showcases Next-generation PCB Manufacturing Solutions at the Thailand Electronics Circuit Asia 2025
08/06/2025 | MKS Instruments, Inc.MKS Inc, a global provider of enabling technologies that transform our world, today announced its participation in Thailand Electronics Circuit Asia 2025 (THECA 2025), taking place August 20–22 at BITEC in Bangkok.