Flexible Circuit Materials for High-Temperature Applications
June 9, 2015 | Sidney Cox, DuPont Circuit and Packaging MaterialsEstimated reading time: 1 minute
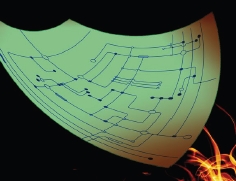
Abstract
Many opportunities exist for flexible circuits in high-temperature applications (automotive, military, aerospace, oil and gas). Flex circuits in these applications have been hindered by a lack of materials that can survive higher temperatures. Some materials, especially some thermoset adhesives, break down over time at higher temperature, becoming brittle or losing adhesion to copper. Polyimides tend to perform much better under high temperature.
The other issue is the lack of good test methods to verify that flex materials can survive higher temperatures. Several methods for testing copper clad laminates exist, but there are very few for coverlays and bondplies. We will discuss different test methods for measuring high-temperature capability including the new IPC service temperature test. We will also report on test results for various flexible materials and our recommendations for the best flexible materials for high temperature applications. This will include development work on new flex materials for high-temperature applications.
Introduction
More applications require flexible circuits that must survive high-temperature environments. These include automotive applications near the engine, oil and gas down-hole pumps, and aerospace applications near jet engines. There have been limited test methods to determine what temperatures flexible materials can survive.
The damage caused by high-temperature environments will mainly fall in three categories: loss of adhesion between copper and dielectric, loss of adhesion between dielectric layers, and embrittlement of the dielectric layers. At the highest temperatures the copper would also become brittle, but in most cases the flexible circuit dielectrics fail first. Thermoset adhesives seem to be most sensitive to embrittlement especially compared to polyimide films which are much more resistant to high temperatures.
Read the full article here.
Editor's Note: This article originally appeared in the June 2015 issue of The PCB Magazine.
Testimonial
"Advertising in PCB007 Magazine has been a great way to showcase our bare board testers to the right audience. The I-Connect007 team makes the process smooth and professional. We’re proud to be featured in such a trusted publication."
Klaus Koziol - atgSuggested Items
How Good Design Enables Sustainable PCBs
08/21/2025 | Gerry Partida, Summit InterconnectSustainability has become a key focus for PCB companies seeking to reduce waste, conserve energy, and optimize resources. While many discussions on sustainability center around materials or energy-efficient processes, PCB design is an often overlooked factor that lies at the heart of manufacturing. Good design practices, especially those based on established IPC standards, play a central role in enabling sustainable PCB production. By ensuring designs are manufacturable and reliable, engineers can significantly reduce the environmental impact of their products.
50% Copper Tariffs, 100% Chip Uncertainty, and a Truce
08/19/2025 | Andy Shaughnessy, I-Connect007If you’re like me, tariffs were not on your radar screen until a few months ago, but now political rhetoric has turned to presidential action. Tariffs are front-page news with major developments coming directly from the Oval Office. These are not typical times. President Donald Trump campaigned on tariff reform, and he’s now busy revamping America’s tariff policy.
Global PCB Connections: Understanding the General Fabrication Process—A Designer’s Hidden Advantage
08/14/2025 | Markus Voeltz -- Column: Global PCB ConnectionsDesigners don’t need to become fabricators, but understanding the basics of PCB fabrication can save you time, money, and frustration. The more you understand what’s happening on the shop floor, the better you’ll be able to prevent downstream issues. As you move into more advanced designs like HDI, flex circuits, stacked vias, and embedded components, this foundational knowledge becomes even more critical. Remember: the fabricator is your partner.
MKS’ Atotech to Participate in IPCA Electronics Expo 2025
08/11/2025 | AtotechMKS Inc., a global provider of enabling technologies that transform our world, announced that its strategic brands ESI® (laser systems) and Atotech® (process chemicals, equipment, software, and services) will showcase their latest range of leading manufacturing solutions for printed circuit board (PCB) and package substrate manufacturing at the upcoming 17th IPCA Show to be held at Pragati Maidan, New Delhi from August 21-23, 2025.
MKS Showcases Next-generation PCB Manufacturing Solutions at the Thailand Electronics Circuit Asia 2025
08/06/2025 | MKS Instruments, Inc.MKS Inc, a global provider of enabling technologies that transform our world, today announced its participation in Thailand Electronics Circuit Asia 2025 (THECA 2025), taking place August 20–22 at BITEC in Bangkok.