-
- News
- Books
Featured Books
- smt007 Magazine
Latest Issues
Current IssueWhat's Your Sweet Spot?
Are you in a niche that’s growing or shrinking? Is it time to reassess and refocus? We spotlight companies thriving by redefining or reinforcing their niche. What are their insights?
Moving Forward With Confidence
In this issue, we focus on sales and quoting, workforce training, new IPC leadership in the U.S. and Canada, the effects of tariffs, CFX standards, and much more—all designed to provide perspective as you move through the cloud bank of today's shifting economic market.
Intelligent Test and Inspection
Are you ready to explore the cutting-edge advancements shaping the electronics manufacturing industry? The May 2025 issue of SMT007 Magazine is packed with insights, innovations, and expert perspectives that you won’t want to miss.
- Articles
- Columns
- Links
- Media kit
||| MENU - smt007 Magazine
Meaningful SPI Production Control Through Automatic Normalization
June 15, 2015 | MEKEstimated reading time: 3 minutes
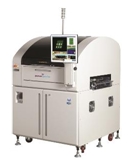
Automated pre-placement solder paste inspection (SPI) has established itself in SMT assembly as an essential tool for optimizing the process and reducing end of line defects. It’s been commonly accepted for many years that a majority of assembly defects can be traced back to print defects, and by using raw measurement data from printed PCBs for volume, area, height and offset, SPC histograms and control charts can quite readily be used to optimize the process.
Following optimization, SPI is used to detect print anomalies. However, the multitude of “normal” variables introduced from board characteristics, clamping methodologies, stencil variations and paste type force unacceptably wide tolerance settings. These board-wide good/bad tolerances can easily mount to +/- 50% or more. For most, this is unacceptable, because of course, with such wide tolerances production drift can be missed and important defects ignored.
Tolerances before and after Optimization are similar
Aperture Release
For example, stencil pattern variations cause differences between designed (expected) and actual solder release. For large apertures, release variation is generally negligible. Small apertures can account for up to 50% release variation or even more. Stencil thickness to aperture area ratio determines how close to 100% release efficiency is achievable. As pads get smaller and smaller, the area of the aperture wall approaches that of the pad area. In turn, the paste release efficiency is reduced as the adhesion forces from the walls approach that of the pad. Thus, different pad sizes across a board will exhibit different volume performance.
A common work-around for this is possible by selecting specific areas and setting tolerances for these apertures.
Though these custom tolerance settings may be individually easy to perform, they are time consuming and do not carry over to other PCB’s due to differences in design, manufacture and finish. These differences are common practice in just in time manufacturing:
1. Solder mask thickness variations; typical thickness 25 um +25/– 12um; Silk screen legends can add 12 um
2. Solder mask defined or non solder mask defined apertures
3. Gasketing effect variations
4. Solder pad finish
a. OSP and gold 0 %variation
b. HASL +/-20 um
5. Board Warpance:
These all create variations on the “zero reference height” point on each pad for measurement.
Mek Automated Normalization
Automated Normalization has been introduced by Mek SPI which directly addresses the excessive time required for board region based tolerance tightening. This unique 2 stage system allows the user to first optimize the printing process and then once the optimization has been completed, to automatically normalise the results and then set tighter tolerances to monitor product drift, enabling meaningful production control. The 5D measurement, combining 2D and 3D measurements ensures proper zero referencing, forming a solid base for accurate and repeatable measurements.
Tolerances after Normalization
The normalization extraction takes user selected average area, height and volume from several previous inspections when being set. Thus, an accurate representation of the capability of the print process is incorporated. If a process change, such as stencil or print settings need be made, the normalization extraction can be readily reset and then applied once again. www.marantz-electronics.com
About MEK (Marantz Electronics Ltd)
A former division of Marantz well known for its high quality Audio/Video products, MEK Japan (Marantz Electronics Kabushiki Kaisha), developed its first AOI system in 1994. Developed to inspect PCB assemblies for correct component placement and soldering, the company’s original AOI system was designed for use in Marantz factories. Proving to be a highly successful, cost-effective alternative to traditional human inspection, MEK developed its first generation commercial system in 1996. With a steadily growing installed base, MEK Japan and its European/American headquarters, MEK, have sold over 5000 units worldwide to date. Now well established as a leading force in AOI technologies, the company recently launched a 5D post-print SPI system which combines 3D and 2D image processing methodologies to deliver unprecedented defect detection. At the beginning of March 2014 the company opened US offices in Las Vegas.
Suggested Items
SHENMAO Strengthens Semiconductor Capabilities with Acquisition of PMTC
07/10/2025 | SHENMAOSHENMAO America, Inc. has announced the acquisition of Profound Material Technology Co., Ltd. (PMTC), a premier Taiwan-based manufacturer of high-performance solder balls for semiconductor packaging.
KYZEN to Highlight Understencil and PCB Cleaners at SMTA Querétaro Expo and Tech Forum
07/09/2025 | KYZEN'KYZEN, the global leader in innovative environmentally responsible cleaning chemistries, will exhibit at the SMTA Querétaro Expo & Tech Forum, scheduled to take place Thursday, July 24, at Centro de Congresos y Teatro Metropolitano de Querétaro.
Driving Innovation: Direct Imaging vs. Conventional Exposure
07/01/2025 | Simon Khesin -- Column: Driving InnovationMy first camera used Kodak film. I even experimented with developing photos in the bathroom, though I usually dropped the film off at a Kodak center and received the prints two weeks later, only to discover that some images were out of focus or poorly framed. Today, every smartphone contains a high-quality camera capable of producing stunning images instantly.
Hands-On Demos Now Available for Apollo Seiko’s EF and AF Selective Soldering Lines
06/30/2025 | Apollo SeikoApollo Seiko, a leading innovator in soldering technology, is excited to spotlight its expanded lineup of EF and AF Series Selective Soldering Systems, now available for live demonstrations in its newly dedicated demo room.
Indium Corporation Expert to Present on Automotive and Industrial Solder Bonding Solutions at Global Electronics Association Workshop
06/26/2025 | IndiumIndium Corporation Principal Engineer, Advanced Materials, Andy Mackie, Ph.D., MSc, will deliver a technical presentation on innovative solder bonding solutions for automotive and industrial applications at the Global Electronics A