-
- News
- Books
Featured Books
- pcb007 Magazine
Latest Issues
Current IssueSales: From Pitch to PO
From the first cold call to finally receiving that first purchase order, the July PCB007 Magazine breaks down some critical parts of the sales stack. To up your sales game, read on!
The Hole Truth: Via Integrity in an HDI World
From the drilled hole to registration across multiple sequential lamination cycles, to the quality of your copper plating, via reliability in an HDI world is becoming an ever-greater challenge. This month we look at “The Hole Truth,” from creating the “perfect” via to how you can assure via quality and reliability, the first time, every time.
In Pursuit of Perfection: Defect Reduction
For bare PCB board fabrication, defect reduction is a critical aspect of a company's bottom line profitability. In this issue, we examine how imaging, etching, and plating processes can provide information and insight into reducing defects and increasing yields.
- Articles
- Columns
- Links
- Media kit
||| MENU - pcb007 Magazine
Estimated reading time: 1 minute
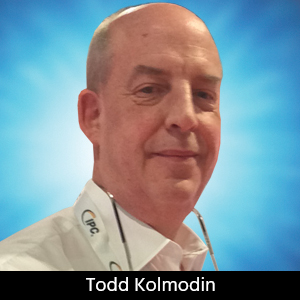
Flex and Rigid-Flex Circuit Testing: Challenges & Solutions
Although flex circuits are nothing new in today’s technology roadmap, the testing of unpopulated flexible circuits can be challenging. These circuits can be very thin, have challenging geometrical configurations and in some cases be a combination of rigid bare board and flex. There are basically three different methods available to test these challenging circuits: manual, fixture and flying probe.
Manual Test
Manual testing simply involves a digital volt meter (DVM) where the circuits are “rang out” by testing the continuity (opens) and discontinuity (shorts) of the individual nets. However many semi-affordable DVMs can only provide continuity measurements true to the IPC and MIL specifications as the resistance resolution for discontinuity (shorts) testing cannot test to the isolation requirements of the specifications.
Fixture Test
Flex circuits, in many cases, can be tested by the use of both dedicated (wired) and universal grid (pinned) fixtures. Both of these fixtures are desired when high volume is manufactured. However, the challenge is registering the product to the actual fixture. Some, but not all, flex circuits have mounting holes that can be used to register the circuit to the fixture, which makes the use of fixtures optimal for high volume.
Unfortunately, mounting holes may be non-plated and the repeatability of registration may be compromised. In other cases, there may be no mounting holes at all as the flex circuit is “clamped” to a connector, making fixture registration difficult. To overcome the challenge, “dams” or registration barriers may be designed into the fixtures so that the flex circuit may still repeatedly register to the fixture. This can be extremely difficult as many current flex circuits have extremely tight designs and very small landing pads (lans.) Mis-registration on these very small pads can result in “mouse biting” or full destruction of the pad itself, resulting in scrap.
Flying Probe Test
This method can be the most advantageous option for testing low to medium volumes. The first advantage is of course cost. The fixture is eliminated as well as the time taken to build it. With only front-end programming required, this is an excellent option for prototypes and small to medium batches.
Editor's Note: This article originally appeared in the June 2015 issue of The PCB Magazine.
More Columns from Testing Todd
Testing Todd: Why 4-wire Kelvin?Testing Todd: Why TDR?
Testing Todd: Positivity Boosts Employee Morale
Testing Todd: Preparing Employees for the Long Haul
Testing Todd: Where Can We Improve?
Testing Todd: Turning Into the Wind
Testing Todd: Coming Back to Life—Design Recovery
Testing Todd: Decision Time—Invest or Delegate?