-
- News
- Books
Featured Books
- pcb007 Magazine
Latest Issues
Current IssueInventing the Future with SEL
Two years after launching its state-of-the-art PCB facility, SEL shares lessons in vision, execution, and innovation, plus insights from industry icons and technology leaders shaping the future of PCB fabrication.
Sales: From Pitch to PO
From the first cold call to finally receiving that first purchase order, the July PCB007 Magazine breaks down some critical parts of the sales stack. To up your sales game, read on!
The Hole Truth: Via Integrity in an HDI World
From the drilled hole to registration across multiple sequential lamination cycles, to the quality of your copper plating, via reliability in an HDI world is becoming an ever-greater challenge. This month we look at “The Hole Truth,” from creating the “perfect” via to how you can assure via quality and reliability, the first time, every time.
- Articles
- Columns
- Links
- Media kit
||| MENU - pcb007 Magazine
Estimated reading time: 2 minutes
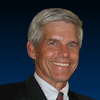
Flexible PCBs and Connectors
While a well-designed flexible circuit will eliminate many connectors, ultimately most need to connect to something. Probably the most common entity that a flex circuit connects to is a rigid printed circuit board, but cable harnesses, polyester membrane switches, and even other flex circuits are also possible connection partners.
The connection is usually done by a hardware device with the purpose of providing both electrical and mechanical connection. The connection must interface to both entities, although the specific mode of connection may be different. For example, a connector may have posts that insert into the vias on a circuit board, while simple insertion may be used for a flex tail with zero insertion force (ZIF) connection. There are thousands of different types of connectors for just about every conceivable combination of pitch, connection angle, material, number of connection points, and type of connection. There are companies that will design and fabricate custom connectors for your exact needs.
Some of the criteria in considering a type of connector include the following:
- Base metals, including plating
- Substrate and conductor thickness
- Number of connection points
- Density of connection
- Current requirements
- Military, aerospace, automotive or medical specifications
- Environment
- Mechanical strength requirements
- Field use
- Cost considerations
The thousands of different types of connectors often can be categorized as some of the following types:
- Zero Insertion Force (ZIF). ZIF connectors require very little force for initial insertion; there is usually a latch, slide or lever that clamps down on the traces to provide a durable, robust connection. ZIF connectors allow a circuit to be inserted and removed multiple times with very little mechanical wear on the traces.
- Mechanical Crimp: A mechanical crimping connector physically pierces through the dielectric and conductor to make a connection.
- Solder Attached: This includes both through-hole connectors and surface mount connectors. The connector mates to pads or vias in the flexible circuit and is soldered for the electrical-mechanical connection. This type of connector includes circular connectors, D Subminiature connectors, pin and socket connectors.
- Z-Axis: A z-axis connector is made out of a special isomeric material that conducts electrical current in only one direction. Z-axis connectors come in strips and do not need special a configuration to match the conductor pitch of the traces.
- Insertion connectors: Unlike ZIF, these insertion devices require a fair amount of force to insert and will significantly scratch or mar the conductor surface if pulled out. These connectors are low-cost and effective for single insertion applications.
- Sculptured (unsupported): Copper traces extend out to provide termination points. Sculptured circuits essentially have the terminals fabricated right into the flex. Selective plating and etching are used to “beef up” the terminal finger.
There are a number of reliable connector suppliers that can help you with your connector requirements. Your flex circuit supplier may also be able to advise you on the best choices for connector hardware to meet your requirements.
Dave Becker is vice president of sales and marketing at All Flex Flexible Circuits LLC.
More Columns from All About Flex
All About Flex: Terms and ConditionsAll About Flex: ISO 9001 Basics
All About Flex: FAQs on UL Listings for Flexible Circuits
All About Flex: Avoiding Trace Fracturing in a Flexible Circuit
Polyimide vs. Silicone for Flexible Heaters
All About Flex: Copper Thickness Requirements for Flex Circuits
All About Flex: Copper Grain Direction
All About Flex: Options for Purchasing Flexible Heaters