-
- News
- Books
Featured Books
- smt007 Magazine
Latest Issues
Current IssueIntelligent Test and Inspection
Are you ready to explore the cutting-edge advancements shaping the electronics manufacturing industry? The May 2025 issue of SMT007 Magazine is packed with insights, innovations, and expert perspectives that you won’t want to miss.
Do You Have X-ray Vision?
Has X-ray’s time finally come in electronics manufacturing? Join us in this issue of SMT007 Magazine, where we answer this question and others to bring more efficiency to your bottom line.
IPC APEX EXPO 2025: A Preview
It’s that time again. If you’re going to Anaheim for IPC APEX EXPO 2025, we’ll see you there. In the meantime, consider this issue of SMT007 Magazine to be your golden ticket to planning the show.
- Articles
- Columns
Search Console
- Links
- Media kit
||| MENU - smt007 Magazine
Reliability Study of Bottom Terminated Components (Part 2)
July 8, 2015 | J. Nguyen, H. Marin, D. Geiger, A. Mohammed, and M. Kurwa, Flextronics InternationalEstimated reading time: 5 minutes
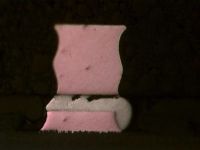
Failure Analysis after 1,000 thermal cycles
The components were cross sectioned after 1000 cycles. Minor cracks were observed for some BTC components. Cracks were typically initiated at the edge of the component at the component side. No crack was initiated at the void location.
Figure 1: Cross Section Images of BTC Component after 1000 Cycle.
Failure Analysis after 3,000 thermal cycles
The thermal cycle test was terminated after 3000 cycles. No failure was observed for the daisy chain components after 3000 cycles. Cracks were more pronounced at certain BTC components such as the QFN132, QFN52, QFN3550 and LGA1837 components. Most cracks were observed at the component side (Figure 2 and Figure 3).
Figure 2: Cross Section Images after 3000 Cycles for QFN52_ Non-Pre-tinned. Crack was usually seen at the component side.
Some cracks at the middle of the solder joint were also seen (Figure 4). Most of the cracks and the more severe cracks happened at the signal pins of the QFN components or when there was a large mismatch in pad design of the component. Thermal pads of QFNs and many LGA components with large pad sizes did not have major cracks after 3000 cycles.
Figure 3: Cross Section Images after 3000 Cycles for QFN88_ Pre-tinned Component. Cracks were seen at the component side and through the solder joint.
Figure 4: Cross Section Images of QFN Component After 3000 Cycles. Crack initiated at the solder joint, not at the void area.
Thermal Cycle Test Summary
There was no correlation between voiding amount at the thermal pad of the BTC and its solder joint thermal reliability. Crack were not initiated from the voids. There was a lack of evidence that voids in the thermal pads accelerated solder joint cracks.
BTC Thermal Modeling
In this study we evaluated the impact of solder voids in the thermal pad of the BTC. The experimentation was done by creating a BTC model and using a thermal simulator to evaluate the heat transfer to the ambient air and PCB. The model includes all single elements in a BTC like packaging mold material, copper pad frame, lead free solder, PCB and copper traces. Also, silicon dies with dimensions and power dissipation information are included. After validating the model by comparing the results with the thermal behavior from the component supplier several voiding conditions were created from 0% up to 98% voids by changing the thermal resistance of the tin based solder and reading the surface temperature of the package. Additional scenarios were created by changing the power dissipation of the package and plotting the results.
Component Selection
For thermal simulation, we used a DC to DC regulator QFN IR3837. This chip incorporates a PWM controller IC and two power Mosfets (control and synchronous FET). This device can operate at different currents and shows considerable power dissipation that facilitates the analysis of the impact of solder voiding.
Page 1 of 2
Suggested Items
KYZEN to Focus on Aqueous Cleaning and Stencil Cleaning at SMTA Juarez
05/20/2025 | KYZEN'KYZEN, the global leader in innovative environmentally responsible cleaning chemistries, will exhibit at the SMTA Juarez Expo and Tech Forum, scheduled to take place Thursday, June 5 at the Injectronics Convention Center in Ciudad Jarez, Chihuahua.
Koh Young Installs 24,000th Inspection System at Top 20 EMS
05/14/2025 | Koh YoungKoh Young, the global leader in True 3D measurement-based inspection and metrology solutions, proudly announces the installation of its 24,000th inspection system at a Top 20 Global EMS in Thailand.
Indium’s Karthik Vijay to Present on Dual Alloy Solder Paste Systems at SMTA’s Electronics in Harsh Environments Conference
05/06/2025 | Indium CorporationIndium Corporation Technical Manager, Europe, Africa, and the Middle East Karthik Vijay will deliver a technical presentation on dual alloy solder paste systems at SMTA’s Electronics in Harsh Environments Conference, May 20-22 in Amsterdam, Netherlands.
SolderKing Achieves the Prestigious King’s Award for Enterprise in International Trade
05/06/2025 | SolderKingSolderKing Assembly Materials Ltd, a leading British manufacturer of high-performance soldering materials and consumables, has been honoured with a King’s Award for Enterprise, one of the UK’s most respected business honours.
Knocking Down the Bone Pile: Gold Mitigation for Class 2 Electronics
05/07/2025 | Nash Bell -- Column: Knocking Down the Bone PileIn electronic assemblies, the integrity of connections between components is paramount for ensuring reliability and performance. Gold embrittlement and dissolution are two critical phenomena that can compromise this integrity. Gold embrittlement occurs when gold diffuses into solder joints or alloys, resulting in mechanical brittleness and an increased susceptibility to cracking. Conversely, gold dissolution involves the melting away of gold into solder or metal matrices, potentially altering the electrical and mechanical properties of the joint.