-
- News
- Books
Featured Books
- pcb007 Magazine
Latest Issues
Current IssueInventing the Future with SEL
Two years after launching its state-of-the-art PCB facility, SEL shares lessons in vision, execution, and innovation, plus insights from industry icons and technology leaders shaping the future of PCB fabrication.
Sales: From Pitch to PO
From the first cold call to finally receiving that first purchase order, the July PCB007 Magazine breaks down some critical parts of the sales stack. To up your sales game, read on!
The Hole Truth: Via Integrity in an HDI World
From the drilled hole to registration across multiple sequential lamination cycles, to the quality of your copper plating, via reliability in an HDI world is becoming an ever-greater challenge. This month we look at “The Hole Truth,” from creating the “perfect” via to how you can assure via quality and reliability, the first time, every time.
- Articles
- Columns
- Links
- Media kit
||| MENU - pcb007 Magazine
Estimated reading time: 2 minutes
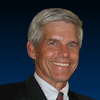
Unique Single-Sided Flexible Circuits
The number of iterations, sequences and combinations possible when manufacturing a flexible circuit can create unique product features to reduce hand assembly of wires, create switch contacts, or eliminate connectors. With minor alterations in basic processing steps such as through-hole generation, etching, plating, and stiffener bonding, a flex circuit applications engineer can often imagine and configure a dramatically different flexible circuit. Changes are generally adopted to achieve some in-use functional requirement such as dynamic flexing, space saving, shielding, or component registration.
Two such examples are back-bared circuits and sculptured flex.
Back-Bared Circuits: A back-bared circuit is essentially a single-sided circuit that has the copper exposed on both sides of the circuit, top and bottom. A single-sided circuit is defined as having a single layer of copper through the laminated dielectrics. Single-side circuits are thinner and require less material and processing steps than a double-sided (two copper layers) circuit. Double-sided circuits are used when the circuit density and layout cannot be routed on a single conductive layer, and when there are applications requiring ground, power planes or shielding as well as for dense surface mount assembly.
There are many cases where a single-sided circuit will fill the requirements, but access to the single copper layer is needed from both sides. A back-bared circuit is often the ideal solution. The exposed copper on the back side can have any of the usual surface treatments applied.
The construction of a back-bared circuit often is achieved by pre-punching or drilling before the dielectric film is laminated to the copper sheet. After laminating copper to the pre-drilled substrate dielectric, the circuit fabrication steps are very similar to a conventional single-sided circuit. The trick is that all the registration steps such as imaging and die cutting must align to the exposed pad features. An alternative process sequence for creating a back-bared pad can use a laser to selectively remove the dielectric film and create the substrate access opening. Cleaning of the copper is needed to remove residue accumulated from the ablation process.
Sculptured Flex: Sometimes, it is desirable to have one section of the flex circuit with very thick copper. This is often done to create finger shaped contacts that are soldered directly to a rigid printed circuit board. This is a way to integrate a connector into the flexcircuit. Other circuit regions need thin copper to accommodate flexing or space requirements. One way to accomplish this would be to create two different flexible circuits, one with thick copper, and then another with thin; however, this would probably require an added connector and comes with associated costs and reliability issues. A better way is to create one flexible circuit that has different copper thicknesses built into it. This is accomplished by differentially etching a thicker copper panel. Differential etching reduces the copper in some areas while leaving it thicker in others.
One can also combine back-bared techniques with selective etching and create a flexible circuit with unsupported fingers (see Eliminate Connectors with Sculptured Flex). Back-bared flex and selective etching provide a wide range of options for creating unique features on a flexible circuit. These features can be designed to meet the exact requirements of an individual application, while maintaining inherent advantages of seamless interconnection and flexibility.
Dave Becker is vice president of sales and marketing at All Flex Flexible Circuits LLC.
More Columns from All About Flex
All About Flex: Terms and ConditionsAll About Flex: ISO 9001 Basics
All About Flex: FAQs on UL Listings for Flexible Circuits
All About Flex: Avoiding Trace Fracturing in a Flexible Circuit
Polyimide vs. Silicone for Flexible Heaters
All About Flex: Copper Thickness Requirements for Flex Circuits
All About Flex: Copper Grain Direction
All About Flex: Options for Purchasing Flexible Heaters