Challenge to Classic Theory of "Organic" Solar Cells Could Improve Efficiency
August 18, 2015 | Purdue UniversityEstimated reading time: 4 minutes
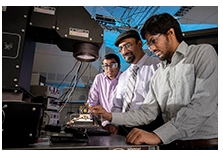
New research findings contradict a fundamental assumption about the functioning of "organic" solar cells made of low-cost plastics, suggesting a new strategy for creating inexpensive solar technology.
Commercialization of organic solar cells has been hindered by inefficiencies, but the findings point toward a potential path to create a new class of solar technology able to compete with standard silicon cells.
"These solar cells could provide a huge cost advantage over silicon," said Muhammad Ashraful Alam, Purdue University's Jai N. Gupta Professor of Electrical and Computer Engineering.
Plastic solar cells might be manufactured using a roll-to-roll process similar to newspaper printing.
"This has been the hope for the last 20-25 years," said Bryan Boudouris, an assistant professor of chemical engineering.
Because organic solar cells are flexible they could find new applications that are unsuitable for rigid silicon cells such as photovoltaics integrated into buildings, and they have the potential to be lower-cost and less energy-intensive to manufacture than silicon devices. However, a critical bottleneck has prevented development of organic solar cells efficient enough to compete with silicon solar technology.
"Now it appears there is no fundamental reason why organic cells have to be less efficient than silicon," Alam said.
"Biswajit had the courage, conviction, and persistence to do a series of difficult experiments, and he was ably supported at various stages by doctoral students Aditya Baradwaj and Ryyan Khan," Alam said.
The paper was authored by Ray, Baradwaj, Khan, Boudouris and Alam.
The primary bottleneck to more efficient organic solar cells is rooted in the fundamental workings of the organic photovoltaic technology. As the semiconducting material is illuminated with light, electrons move from one energy level to another. Due to the atomic structure, the electrons in the semiconductor occupy a region of energy called the "valence band" while the material is in the dark. But shining light on the material causes the electrons to absorb energy, elevating them into a region of higher energy called the "conduction band." As the electrons move to the conduction band they leave behind "holes" in the valance band, generating so-called electron-hole pairs in the plastic solar cells called excitons.
"Because the electron is negatively charged and the hole is positively charged, they like each other so much that they orbit around each other," Ray said. "You have to keep these two separated or they will recombine and you will not generate current."
This "charge separation" is maintained by inserting numerous structures called bulk heterojunctions, a design that has been a challenge to manufacture in a high-speed, large-scale and reproducible manner.
"You can think of these heterojunctions almost like knives cutting through the material to separate the electrons and holes," Alam said. "These heterojunctions have to be distributed throughout so that no matter where the electron-hole pair is generated you can cut them."
This requirement limits the efficiency of organic solar cells, a bottleneck established by research more than two decades ago. However, Ray showed through detailed computational modeling that a fundamental assumption about the organic solar cells was incorrect, eliminating the need for heterojunctions.
"He kept saying he didn't need to invoke excitons in order to explain many of the experimental results," Alam said. "It turns out that the original experiment was misinterpreted."
This misinterpretation arises from the design of organic cells. The cells have two metal contacts, one on top and one on the bottom of the device, and each is made of different types of metal. Because of this configuration, incoming sunlight generates an electric field concentrated at the bottom of the cell, which allows the electron-hole pairs to readily recombine. Ray proposed flipping the contacts so that the electric field forms at the top of the cell instead of at the bottom, allowing for better charge separation.
"He inverted the structure and explained that the inefficiency is taking place because the electron-hole pairs are not staying separated," Alam said.
Simulations showed flipping the configuration allowed for better charge separation and higher efficiency, and then laboratory experiments by Ray, Baradwaj and Khan validated the new concept.
The findings also suggest the design of organic solar cells can be simplified, representing a major potential innovation, Ray said. Whereas conventional organic solar cells are made by mixing two types of polymers, the new design requires only one polymer.
"Currently, you have to design the solar cells according to how well two organic materials mix together in order to produce these numerous heterojunctions," Boudouris said. "But if you only needed one polymer instead of two, the manufacturability on the large scale could be very much improved, so this is an exciting development."
Findings also suggest that producing the cells out of purer polymers could result in more efficient solar cells, and the research likely will lead to a better understanding of the physics of how organic solar cells operate, Alam said.
Much of the experimental work was performed in the Purdue Solar Energy Utilization Laboratory, formed with funds from the National Science Foundation, which allows specialists from different fields to collaborate. The research is ongoing, and Khan will continue to work on a new class of solar cells that do not require bulk heterojunctions.
The research was funded by the U.S. Department of Energy through DOE’s Center for Re-Defining Photovoltaic Efficiency through Molecule Scale Control, the National Science Foundation’s Network for Computational Nanotechnology, and the U.S. Air Force Office of Scientific Research.
Suggested Items
Digital Twin Concept in Copper Electroplating Process Performance
07/11/2025 | Aga Franczak, Robrecht Belis, Elsyca N.V.PCB manufacturing involves transforming a design into a physical board while meeting specific requirements. Understanding these design specifications is crucial, as they directly impact the PCB's fabrication process, performance, and yield rate. One key design specification is copper thieving—the addition of “dummy” pads across the surface that are plated along with the features designed on the outer layers. The purpose of the process is to provide a uniform distribution of copper across the outer layers to make the plating current density and plating in the holes more uniform.
Meet the Author Podcast: Martyn Gaudion Unpacks the Secrets of High-Speed PCB Design
07/10/2025 | I-Connect007In this special Meet the Author episode of the On the Line with… podcast, Nolan Johnson sits down with Martyn Gaudion, signal integrity expert, managing director of Polar Instruments, and three-time author in I-Connect007’s popular The Printed Circuit Designer’s Guide to... series.
Showing Some Constraint: Design007 Magazine July 2025
07/10/2025 | I-Connect007 Editorial TeamA robust design constraint strategy balances dozens of electrical and manufacturing trade-offs. This month, we focus on design constraints—the requirements, challenges, and best practices for setting up the right constraint strategy.
Elementary, Mr. Watson: Rein in Your Design Constraints
07/10/2025 | John Watson -- Column: Elementary, Mr. WatsonI remember the long hours spent at the light table, carefully laying down black tape to shape each trace, cutting and aligning pads with surgical precision on sheets of Mylar. I often went home with nicks on my fingers from the X-Acto knives and bits of tape all over me. It was as much an art form as it was an engineering task—tactile and methodical, requiring the patience of a sculptor. A lot has changed in PCB design over the years.
TTCI Joins Printed Circuit Engineering Association to Strengthen Design-to-Test Collaboration and Workforce Development
07/09/2025 | The Test Connection Inc.The Test Connection Inc. (TTCI), a leading provider of electronic test and manufacturing solutions, is proud to announce its membership in the Printed Circuit Engineering Association (PCEA), further expanding the company’s efforts to support cross-functional collaboration, industry standards, and technical education in the printed circuit design and manufacturing community.