-
- News
- Books
Featured Books
- smt007 Magazine
Latest Issues
Current IssueSupply Chain Strategies
A successful brand is built on strong customer relationships—anchored by a well-orchestrated supply chain at its core. This month, we look at how managing your supply chain directly influences customer perception.
What's Your Sweet Spot?
Are you in a niche that’s growing or shrinking? Is it time to reassess and refocus? We spotlight companies thriving by redefining or reinforcing their niche. What are their insights?
Moving Forward With Confidence
In this issue, we focus on sales and quoting, workforce training, new IPC leadership in the U.S. and Canada, the effects of tariffs, CFX standards, and much more—all designed to provide perspective as you move through the cloud bank of today's shifting economic market.
- Articles
- Columns
- Links
- Media kit
||| MENU - smt007 Magazine
Selecting a Reflow Oven, Part 2
September 2, 2015 | Robert Voigt, DDM NovastarEstimated reading time: 2 minutes
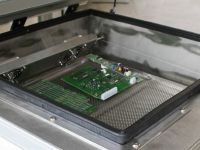
In this follow-up to Part 1, which focused on selecting and evaluating a basic reflow oven configuration for a circuit board assembly environment, we’ll address heating technologies, methods of board transportation, and inerting systems.
Heating Technologies
Regardless of the technology used for heating boards, the primary objective is to control the thermal profile to prevent undesirable conditions, such as:
• Tombstoning: a condition that causes the component to stand up due to micro-explosions in the solder
• Delamination of the substrate (a partial separation of the layers of circuit board material, similar to blisters)
• Poor adhesion/contact: caused by over-heating and under-heating
Typically, there are three main methods used for reflow oven heating. They are:
1. Vapor phase
2. Infrared
3. Convection
Vapor Phase
Vapor phase is a simple and very reliable method of soldering. Complex components and assemblies can be done in a small process window, but this comes at a cost, so understand the process and what is involved before making a purchase decision.
Vapor phase heating is performed in a batch process using a special liquid with a very particular vaporization temperature of 240°F, ensuring that materials are never overheated and damaged. Parts are placed in a single chamber above a liquid bath, which is then heated to create a vapor at the perfect melting point of solder. The board is enveloped in the vapor to accomplish the soak and reflow over time, and the chamber temperature is reduced to condense the vapor back into the liquid bath. The parts are then removed and replaced with a new board (or set of boards).
Infrared (IR)
IR systems were widely used throughout the 1990s because they were relatively inexpensive to buy and operate. IR heating can be used in either batch or continuous conveyorized units. While still available for specialized applications, IR heating is affected by the color of the target components, so different colored components absorb heat at different rates and can produce different heating profiles, not entirely desirable.
Today, IR heating is often used for special applications where heat ramp rates need to go quickly with very little soak time. The direct heating technique of IR makes modulation and control very difficult. Factors that can be used to vary the heating profile include distance, speed and heat intensity. For these reasons, IR is not often used in low- to medium-volume production environments which need to accommodate a wide range of board configurations and heat profiles.
Convection
Convection heating is the most widely used method for reflowing circuit boards today. In this system, air is circulated throughout one or more chambers (or zones), either vertically or horizontally, to surround the entire board assembly with even, uniform heat. Each zone in a multi-zone oven retains its own heat profile very reliably. Both the vertical and horizontal methods of heat distribution share the same end result—even heat around the boards.
A plenum heat distribution system typically directs air vertically from above and below toward the board surfaces. They often require preheating plenums to condition the air temperature before heating the board, but directing airflow from two different directions (top and bottom) allows the user to adjust heat settings independently and with good control to create a very precise profile. This type of system is usually more complicated to build and thus more expensive than a horizontal convection type.
Editor's Note: This article originally appeared in the September 2015 issue of SMT Magazine.
Testimonial
"In a year when every marketing dollar mattered, I chose to keep I-Connect007 in our 2025 plan. Their commitment to high-quality, insightful content aligns with Koh Young’s values and helps readers navigate a changing industry. "
Brent Fischthal - Koh YoungSuggested Items
Indium Promotes Huang to Senior Manager, Marketing Communications
08/28/2025 | Indium CorporationWith its commitment to innovation and growth through employee development, Indium Corporation announces the promotion of Jingya Huang to Senior Manager, Marketing Communications, to continue to lead the company’s branding and promotional efforts.
Rehm Academy Expands Its Training Program
08/28/2025 | Rehm Thermal SystemsThe demands on modern industrial companies and employees continue to rise, and therefore, the topic of further education is becoming increasingly important today.
MacDermid Alpha Awarded for Innovation: Driving Process Optimization and Efficiency with Major Indian EMS Provider
08/28/2025 | MacDermid Alpha Electronics SolutionsMacDermid Alpha Electronics Solutions, a leading global supplier of integrated materials for the electronics industry, is recognized by one of India’s top EMS providers, Syrma SGS, with an award for innovation that advanced process optimization, enhanced operational efficiency, and yield gains.
Integrated Solutions for Board-level Reliability: A Smarter Path Forward
08/27/2025 | Alan Gardner, MacDermid Alpha Electronics SolutionsIn today’s electronics manufacturing landscape, reliability is no longer just a benchmark but a business imperative. As industries such as automotive, aerospace, and high-performance computing (HPC) push the boundaries of innovation, the demand for dependable board-level performance under extreme conditions has never been greater.
ZESTRON Expands Capabilities with Addition of the EPS by i-Tech AG 75 Pallet Cleaning System
08/26/2025 | ZESTRONZESTRON, the global leader in high-precision cleaning solutions and services, is excited to announce the addition of a new capability in its Technical Center in Manassas, VA: