-
-
News
News Highlights
- Books
Featured Books
- pcb007 Magazine
Latest Issues
Current IssueSales: From Pitch to PO
From the first cold call to finally receiving that first purchase order, the July PCB007 Magazine breaks down some critical parts of the sales stack. To up your sales game, read on!
The Hole Truth: Via Integrity in an HDI World
From the drilled hole to registration across multiple sequential lamination cycles, to the quality of your copper plating, via reliability in an HDI world is becoming an ever-greater challenge. This month we look at “The Hole Truth,” from creating the “perfect” via to how you can assure via quality and reliability, the first time, every time.
In Pursuit of Perfection: Defect Reduction
For bare PCB board fabrication, defect reduction is a critical aspect of a company's bottom line profitability. In this issue, we examine how imaging, etching, and plating processes can provide information and insight into reducing defects and increasing yields.
- Articles
- Columns
- Links
- Media kit
||| MENU - pcb007 Magazine
Material Witness: Using Scaled Flow Data
September 16, 2015 | Chet GuilesEstimated reading time: 5 minutes
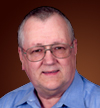
The IPC TM-650 Scaled Flow Test (2.4.38) uses three values to determine pressed thickness and flow of a given resin system: Ho (the theoretical value of a pressed sample assuming no air entrainment and no flow calculated from the weight of the test stackup), Hf (the actual final thickness per ply measured by micrometer after the flow test) and ΔH (the difference between Ho and Hf expressed in mils of thickness change).
Based on work done originally by Bartlett, Bloechele and Mazeika at Bell Labs in New Jersey [1] and discussed in relation to specific grades of epoxy prepreg by Del, Marx and Sallo of Fortin Laminating [2], scaled flow has long been used in the industry for characterizing epoxy prepregs used for manufacturing multilayer PWBs.
The scaled flow test depends on understanding the Integrated Flow Value for a prepreg system, which can be expressed as
Flow ~ C * (P/A) * Integral (1/η) (from time 0 to ∞)
Where: C is a constant for the particular resin system determined empirically
(P/A) is the ratio of pressure (psi) to area (in2)
Integral (1/η) is the integral of 1/viscosity (poise) taken over the melt, flow and cure cycle
The flow at any given moment is inversely proportional to the viscosity, so the integral takes into account the changing viscosity as the resin first melts and then starts to cure. The ΔH value of the scaled flow test is a measure of the integrated flow during the entire test, and as we will see, the flow of prepreg during MLB fabrication can be controlled by taking this ΔH value into consideration.
The basic scaled flow test uses either 10 plies 5.5” x 7” for heavier glass fabrics such as 2113, 2116, etc. or 18-20 plies for lightweight glass fabrics such as 106 and 1080. These stacks are designed to provide approximately equal masses of material regardless of glass style to normalize the test parameters. (A substantially heavier stack would heat up unevenly and more slowly, and a substantially lighter stack would heat up too fast and give doubtful results.)
The stack weights are used to calculate Ho based on the glass weight and density as well as the resin weight and density. The original scaled flow test was based on conventional FR-4 epoxy whose resin density was approximately 1.35. Nominal values of glass weight and density and resin weight and density are used for doing the calculation of Ho based on actual stack weight.
Resin systems whose density is not very near 1.35 do not quite fit into the official IPC test method because all the stack weight data used assumes epoxy resin of a standard 1.35 density. Any resin whose density varies from that value requires a new set of calculated weights for various stack-ups in order to provide precise data. This is especially true of filled systems whose resin density now includes a ceramic component as well as the organic resins themselves and may have densities higher than standard. For example, a filled polyimide resin whose density is 1.41 would appear to be pressing too thin if the Ho was calculated based on epoxy calculations at 1.35; and conversely, a polyimide system whose resin density was 1.30 (because of low or no Bromine content) would seem to be pressing too thick if calculations were performed based on a standard epoxy at density 1.35. I mention this because there is a tendency to use the IPC method as if the table of basis weights is gospel, while in fact it is only valid for resin systems whose density is that of standard FR-4.
Because our primary interest is in final pressed thickness, scaled flow testing provides a useful tool for making first order approximations of this critical value, and also provides a useful value (ΔH) for adjusting pressure to achieve desired levels of flow.
This relationship can be expressed roughly as:
P = k * (1/ ΔH) * A * [√(W)/ √(L)]
Where: k is a constant based on the resin system and units (~1 for conventional polyimide systems)
(1/ ΔH) is the reciprocal of the ΔH value from the scaled flow test
A is the area of the MLB being pressed
[√(W)/ √(L)] is a “shape factor” using the ratio of the square roots of the width and length
An 18 x 12 lamination size with a k of 1.0 gives the following data. As you can see in Figure 1, at ΔH 0.5 the laminating pressure is about 350 psi, which can be adjusted as needed for a particular design, or reduced somewhat if vacuum lamination is used, and so forth. The point is that with a normal range of ΔH = 0.4 to 0.8 you can quickly see how to adjust pressure to compensate for any flow issues. At very low values of ΔH, the pressure requirement to achieve adequate flow will rise rapidly – as might be the case with out of date prepreg, or low-flow prepreg if flow and fill becomes critical.
Figure 1: Graph showing laminating pressure vs ΔH value for polyimide.
The use of scaled flow has another hidden benefit for thickness control. By using a weight standard rather than a traditional resin content test, any variation in the basis weight of the glass fabric is minimized. Because the density of resin is roughly half that of glass, any change in glass weight will require about double that increase to keep resin content “in spec,” which can result in too thick a pressed thickness per ply. Conversely, if the glass basis weight runs low, reducing resin to achieve the “spec percentage” can result in a laminate that will press too thin.
With pressed ply thickness critical to electrical properties such as impedance (Zo) and to overall board thickness, use of a scaled flow standard based on weight and ΔH results in a tighter control of thickness than would otherwise be achieved. Now some might say this is a small difference, and it may well be in most cases, but when you are building 15-25 layer MLBs, with two or more pieces of prepreg between each inner layer detail, tolerance variations can add up quickly.
Arlon is using a scaled flow method internally to control weights and flows for its lamination grade prepregs with the result that in the past year we have made significant improvements in laminate thickness variability. In newer products such as filled laminates and prepregs, scaled flow would be the material specification of choice for calling our thickness and flow.
Hoping that this brief overview will help those of you who have not been using scaled flow for many years to appreciate the benefits this method can confer. With summer 2015 behind us, this is the Material Witness wishing all a Happy Autumn!
Chet Guiles is a consultant for Arlon Electronic Materials.
Testimonial
"Our marketing partnership with I-Connect007 is already delivering. Just a day after our press release went live, we received a direct inquiry about our updated products!"
Rachael Temple - AlltematedSuggested Items
Creating Connections in Mexico
07/30/2025 | Michelle Te, Community MagazineA concerted effort by the Global Electronics Association—Mexico team over the past year has created inroads for the Global Electronics Association (formerly IPC) with leading electronics companies, government offices, and academic institutions in Mexico. “Our goal is to bring more awareness to what the Global Electronics Association is and what it offers,” says Lorena Villanueva, senior director. “We also aim to increase our membership. Of 3,200 members of the Global Electronics Association, only 180 are in Mexico.”
Powering Progress: Summer 2025 Community Magazine Now Available
07/22/2025 | Community MagazineIn the new Summer 2025 edition of Community Magazine, members of the Global Electronics Association demonstrate what progress really looks like—through innovation on the factory floor, influence on public policy, and investment in the next generation of engineers.
TRI to Exhibit at SMTA Queretaro Expo 2025
07/16/2025 | TRITest Research, Inc. (TRI), the leading provider of test and inspection systems for the electronics manufacturing industry, is pleased to announce plans to exhibit at the SMTA Querétaro Expo 2025, scheduled to take place on July 24, 2025, at the Querétaro Centro de Congresos y Teatro Metropolitano.
Global PCB Connections: Let the Spec Fit the Board, Not Just the Brand
07/17/2025 | Jerome Larez -- Column: Global PCB ConnectionsIf you’ve ever seen an excellent PCB quote delayed, or worse, go cold because of a single line on the fab print, you’re not alone. Often, that line reads something like, “Use 370HR only,” or “IT-180A required.” These and other brand-name materials are proven performers, but unless your design needs that specific resin system (say, for RF performance, thermal reliability, or stringent CAF resistance), you may inadvertently be holding your job hostage.
IPC Hall of Fame Spotlight Series: Highlighting Lionel Fullwood
07/15/2025 | Dan Feinberg, I-Connect007Many IPC members who have contributed significantly to IPC and our industry have been awarded the IPC Raymond E. Pritchard Hall of Fame (HOF) Award. Though many early HOF members have passed away and are unknown to today’s IPC membership, their contributions still resonate. This special series on IPC Hall of Fame members provides a reminder of who was honored and why. As a bonus, for those who are still around, we get to find out what these talented individuals are up to today.