-
- News
- Books
Featured Books
- smt007 Magazine
Latest Issues
Current IssueWhat's Your Sweet Spot?
Are you in a niche that’s growing or shrinking? Is it time to reassess and refocus? We spotlight companies thriving by redefining or reinforcing their niche. What are their insights?
Moving Forward With Confidence
In this issue, we focus on sales and quoting, workforce training, new IPC leadership in the U.S. and Canada, the effects of tariffs, CFX standards, and much more—all designed to provide perspective as you move through the cloud bank of today's shifting economic market.
Intelligent Test and Inspection
Are you ready to explore the cutting-edge advancements shaping the electronics manufacturing industry? The May 2025 issue of SMT007 Magazine is packed with insights, innovations, and expert perspectives that you won’t want to miss.
- Articles
- Columns
- Links
- Media kit
||| MENU - smt007 Magazine
Technologies to Enable Quick-Turn PCB Assemblies
October 21, 2015 | Khurrum Dhanji, Imagineering Inc.Estimated reading time: 2 minutes
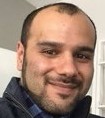
Many new and unique processes enable quick-turn assembly in 24 hours rather than days. Latest innovations include state-of-the-art machines, such as the stencil-less jet printer, and a proprietary PCB assembly turnkey quote system that gives customers a quote in minutes—not in days or weeks—and a fully assembled prototype PCB in 24 hours, after receipt of all materials. Multi-day lead times for PCB assembly are a thing of the past as a few advanced thinking assemblers have worked hard to remove the time-related road blocks, enabling quick prototype assembly.
New software such as Instant PCBA Quotes Online allows you to receive a guaranteed quote in minutes. The second major time-related hurdle to be eliminated was the cost of buying and waiting for the solder paste stencil to be manufactured and delivered. A new disruptive technology, the advanced solder paste inkjet, is an in-line soldermask printer that allows instant changes between assembly jobs. Full and instant 3D printing of different thicknesses of solder paste, improved start-to-delivery time for prototype PCB assembly, and significantly improved soldering quality eliminates 90% percent of the rework time.
With reduced product development times, the electronic manufacturer’s requirement for PCB assembly is 24 hours, enabling continued rapid development of a new product that will not stall at the final stage.
Stencil-less Jet Printing
For many years, stencil printing has been the standard and durable method of depositing solder paste on surface mount assembly PCBs, but difficulties often significantly slowed down a change from one product to another in the assembly operation, as well as added cost. A significant challenge in newer, smaller electronics assembly is the huge difference of size among components. Therefore, trying to apply the right amount of solder paste for each component with one stencil is difficult.
The biggest problem is how to produce quick-turn prototypes without disrupting series production that is already running in the line.
Product changeover requires time-consuming tweaks to the stencil printing process, while unnecessarily shutting down an expensive assembly line to change the product. The inability of the stencil’s technology to vary solder paste volume by part, on the run, remains the biggest impact on the soldering quality.
Solder paste parameter optimizing after set up can take considerable time away from production. Frequent changeovers create a bottleneck in assembly speed. Stencil manufacturing and lead time, as well as occasional replacement, add to the delays. Each PCB design and design change requires a new stencil. Thus, stencil costs and two- to three-day time delays can happen with multiple rev changes. Stencil-free jet printing technology has been developed to meet the demand for greater flexibility in modern electronics production, significantly improving the throughput speed. The CAD data (or Gerber data) for a particular PCB, compiled off-line, is sent to the ink jet printer for instant printing.
Suggested Items
Driving Innovation: Direct Imaging vs. Conventional Exposure
07/01/2025 | Simon Khesin -- Column: Driving InnovationMy first camera used Kodak film. I even experimented with developing photos in the bathroom, though I usually dropped the film off at a Kodak center and received the prints two weeks later, only to discover that some images were out of focus or poorly framed. Today, every smartphone contains a high-quality camera capable of producing stunning images instantly.
Hands-On Demos Now Available for Apollo Seiko’s EF and AF Selective Soldering Lines
06/30/2025 | Apollo SeikoApollo Seiko, a leading innovator in soldering technology, is excited to spotlight its expanded lineup of EF and AF Series Selective Soldering Systems, now available for live demonstrations in its newly dedicated demo room.
Indium Corporation Expert to Present on Automotive and Industrial Solder Bonding Solutions at Global Electronics Association Workshop
06/26/2025 | IndiumIndium Corporation Principal Engineer, Advanced Materials, Andy Mackie, Ph.D., MSc, will deliver a technical presentation on innovative solder bonding solutions for automotive and industrial applications at the Global Electronics A
Fresh PCB Concepts: Assembly Challenges with Micro Components and Standard Solder Mask Practices
06/26/2025 | Team NCAB -- Column: Fresh PCB ConceptsMicro components have redefined what is possible in PCB design. With package sizes like 01005 and 0201 becoming more common in high-density layouts, designers are now expected to pack more performance into smaller spaces than ever before. While these advancements support miniaturization and functionality, they introduce new assembly challenges, particularly with traditional solder mask and legend application processes.
Knocking Down the Bone Pile: Tin Whisker Mitigation in Aerospace Applications, Part 3
06/25/2025 | Nash Bell -- Column: Knocking Down the Bone PileTin whiskers are slender, hair-like metallic growths that can develop on the surface of tin-plated electronic components. Typically measuring a few micrometers in diameter and growing several millimeters in length, they form through an electrochemical process influenced by environmental factors such as temperature variations, mechanical or compressive stress, and the aging of solder alloys.