-
-
News
News Highlights
- Books
Featured Books
- smt007 Magazine
Latest Issues
Current IssueIntelligent Test and Inspection
Are you ready to explore the cutting-edge advancements shaping the electronics manufacturing industry? The May 2025 issue of SMT007 Magazine is packed with insights, innovations, and expert perspectives that you won’t want to miss.
Do You Have X-ray Vision?
Has X-ray’s time finally come in electronics manufacturing? Join us in this issue of SMT007 Magazine, where we answer this question and others to bring more efficiency to your bottom line.
IPC APEX EXPO 2025: A Preview
It’s that time again. If you’re going to Anaheim for IPC APEX EXPO 2025, we’ll see you there. In the meantime, consider this issue of SMT007 Magazine to be your golden ticket to planning the show.
- Articles
- Columns
Search Console
- Links
- Media kit
||| MENU - smt007 Magazine
Process Improvements for Cycle Time Reduction
October 28, 2015 | Stephen Las Marias, I-Connect007Estimated reading time: 3 minutes
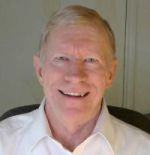
One of the issues highlighted in I-Connect007’s Cycle Time Reduction survey for SMT Magazine this month was how automation can help reduce cycle times.
To help answer this, industry veteran Randall Williams, a mechanical automation engineer at B&P Automation Inc., explained the importance of reducing cycle time, key metrics to look for when planning for improvement processes in assembly lines, best practices to consider, and how automation can help electronics manufacturers improve their production.
Stephen Las Marias: How do you define cycle time, and from your experience in the electronics assembly industry, what are the biggest bottlenecks in assembly lines that contribute to longer cycle times?
Randall Williams: Every company calculates cycle time differently. Ours is simple: value addition/time required to add that value. I do not calculate visual inspection as part of that time because I normally work with automation that includes machine vision in milliseconds— not significant time added. Example: inserting chemicals into wells of the product/amount of time required to perform that function.
Bottlenecks fall into three categories: inattentive/ inadequately trained operators; equipment requiring human interaction to keep it running or long time cycle programs; and incorrectly designed process sequencing. The latter is where most of my time is spent. I can usually re-order the process sequence to reduce bottlenecks. Part of that effort is typically spent in designing or locating different equipment to perform a function. Product burn-in or cure is a good example. Taking that step out of the process flow and making it a feeder line is sometimes the answer.
Las Marias: How important is reducing cycle time?
Williams: CT reduction is always a large benefit to a manufacturer. My experience has shown that reduction of in-process inventory has the greatest impact on the bottom line. The faster you can get product to the customer, the lower your cost per unit. With CT reduction, you can plan for larger start quantities in a given time frame, allowing better pricing on raw materials with those increased quantities.
Las Marias: From your experience as a consultant to electronics assembly manufacturers, can you please give some examples as to how you were able to help reduce the cycle time of a particular process or project? What were the main challenges here, and what tools or strategies did you implement to help shorten the cycle times of these processes?
Williams: I was working at a medical product manufacturer some years ago and part of a team that was tasked with this challenge. We determined that an automated single room production line, single unit lot, continuous flow with infrequent product changes was the answer. So that was what we worked on for about two years. My portion was the material handling, robotics/machine vision and computer integration designs. Some of the process steps would benefit from existing equipment vendors, while others had to be designed as a unique item.
The latter was the challenge. Finding a vendor with the basic process capabilities and design strength to put those together took significant time on the front end of the project. Most of our manpower was directed in that effort for two equipment items.
The remaining designs were much more straightforward—taking off-the-shelf equipment items and placing them in combination—and performing the integration required much less effort. We were able to reduce the process time from three days to about six hours. Each step was reduced to less than 50% of the former CT. We were asked to duplicate this line in other parts of the world. Some of the ‘non-value adding’ steps performed previously were eliminated.
We were fortunate to have garnered management support before the projected started, making approvals much easier. The other success factor that was significant was transparency. I see so many companies that encourage territorialism—secrecy between departments. We were able to get great ideas sharing design concepts in brainstorming sessions with other non-related departments.
Editor's Note: This article originally appeared in the October 2015 issue of SMT Magazine.