All About Flex: Plated Through-holes in Flexible Circuits
October 29, 2015 | Dave Becker, All FlexEstimated reading time: 4 minutes
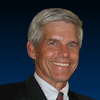
There is probably no more important feature than the plated through-hole (also called via or via hole) with regard to the reliability and integrity of a flexible circuit. The through-hole provides electrical connection between insulated layers and enables electrical functionality on double-sided and multilayer flexible circuits.
There are a number of methods that a flex circuit manufacturer may use when generating a via hole. For example, one can create through-holes on a panel with no circuit patterns defined, or one can insert the through-holes after the circuit traces have been imaged and etched. There are advantages and disadvantages for both situations, but the basics of creating a through-hole are the same.
The first step in via formation is to create a hole through the laminate. The hole can be created by mechanical drilling, laser drilling or punching. Once the hole has been drilled, an adhesive-based laminate will look similar to the diagram below:
Figure 1: Through-hole, side view.
Figure 1 depicts the case where a laminate consisting of copper foil, adhesive, dielectric, adhesive and copper foil are used. Adhesiveless laminates are also very popular and are produced with a variety of technologies that bond copper to dielectrics sans adhesive.
Electroplating is a process where metal ions are bonded to a metal surface. The process requires a voltage potential between a copper source (anode) and the plating target (copper circuit). Both the anode and copper circuit are immersed in a copper sulphate solution with an applied voltage potential. This promotes ion flow from the anode to the cathode (the circuit). Areas of a circuit panel with a voltage potential will get plated, so any part of a copper circuit that is electrically isolated will not get plated. Since copper layers are separated by dielectric materials, and there is no electrical charge going through the through-hole, electroplating between layers is not possible. In order to allow electroplating, a conductive “bridge” must be coated over the insulating layer.
The two most common methods for creating that conductive bridge are:
- Electroless copper plating
- Shadow plating
Page 1 of 4
Testimonial
"Advertising in PCB007 Magazine has been a great way to showcase our bare board testers to the right audience. The I-Connect007 team makes the process smooth and professional. We’re proud to be featured in such a trusted publication."
Klaus Koziol - atgSuggested Items
How Good Design Enables Sustainable PCBs
08/21/2025 | Gerry Partida, Summit InterconnectSustainability has become a key focus for PCB companies seeking to reduce waste, conserve energy, and optimize resources. While many discussions on sustainability center around materials or energy-efficient processes, PCB design is an often overlooked factor that lies at the heart of manufacturing. Good design practices, especially those based on established IPC standards, play a central role in enabling sustainable PCB production. By ensuring designs are manufacturable and reliable, engineers can significantly reduce the environmental impact of their products.
50% Copper Tariffs, 100% Chip Uncertainty, and a Truce
08/19/2025 | Andy Shaughnessy, I-Connect007If you’re like me, tariffs were not on your radar screen until a few months ago, but now political rhetoric has turned to presidential action. Tariffs are front-page news with major developments coming directly from the Oval Office. These are not typical times. President Donald Trump campaigned on tariff reform, and he’s now busy revamping America’s tariff policy.
Global PCB Connections: Understanding the General Fabrication Process—A Designer’s Hidden Advantage
08/14/2025 | Markus Voeltz -- Column: Global PCB ConnectionsDesigners don’t need to become fabricators, but understanding the basics of PCB fabrication can save you time, money, and frustration. The more you understand what’s happening on the shop floor, the better you’ll be able to prevent downstream issues. As you move into more advanced designs like HDI, flex circuits, stacked vias, and embedded components, this foundational knowledge becomes even more critical. Remember: the fabricator is your partner.
MKS’ Atotech to Participate in IPCA Electronics Expo 2025
08/11/2025 | AtotechMKS Inc., a global provider of enabling technologies that transform our world, announced that its strategic brands ESI® (laser systems) and Atotech® (process chemicals, equipment, software, and services) will showcase their latest range of leading manufacturing solutions for printed circuit board (PCB) and package substrate manufacturing at the upcoming 17th IPCA Show to be held at Pragati Maidan, New Delhi from August 21-23, 2025.
MKS Showcases Next-generation PCB Manufacturing Solutions at the Thailand Electronics Circuit Asia 2025
08/06/2025 | MKS Instruments, Inc.MKS Inc, a global provider of enabling technologies that transform our world, today announced its participation in Thailand Electronics Circuit Asia 2025 (THECA 2025), taking place August 20–22 at BITEC in Bangkok.