All About Flex: Flexible PCB: What’s in a Name?
November 12, 2015 | Dave Becker, All FlexEstimated reading time: 3 minutes
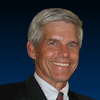
Flexible PCB is a common term that is synonymous with flexible circuits. While the term “PCB” is generally used to describe rigid printed circuitry, “flexible PCB” is a little contradictory because “boards” aren’t really flexible. Some companies, like All Flex, design and manufactures flexible PCBs, but not rigid PCBs.
There are many similarities between the two, but also significant differences.
Design
The shortest distance between two points is a straight line, so a circuit trace on a flex circuit should look like a circuit trace on a rigid circuit board, right? Actually there can be considerable differences between designing a rigid PCB and a flexible PCB. Because of the flexibility feature, there are unique issues affecting robustness. For example, since flex can bend, one needs to be sure that bending does not crack or break solders joints near a bend location. For this reason, design features like radiused corners and filleted pads are common on flexible circuits. Another issue is that the substrate used for flex is not as dimensionally stable vs. its rigid cousin. Allowances for dimensional changes may be required for flexible PCB design. Most PCB design software is tailored to rigid printed circuit materials and features. Tradeoffs occur when this same software is used to design flexible PCBs[1].
Fabrication
Rigid PCBs and flexible PCBs have very similar fabrication steps and often use the same equipment and equipment manufacturers. For example, photo imaging the base circuitry layer can use virtually identical technology. The differences arise because of the difference between handling a rigid board versus a flexible substrate. Some ultra-thin circuits are extremely flimsy and need special material handling systems. While a PCB is relatively easy to handle, a thin flexible circuit may need special clamping, fixturing or vacuum systems to hold it in place while processing. Some very high-volume flexible PCB manufactures process circuits in a continuous reel (reel-to-reel). Reel to reel processing uses significantly different material handling mechanisms vs. systems processing discrete panel sizes.
Tooling
Both PCBs and flexible PCBs use similar tooling such as CAD files, photo tools and electrical test fixtures. Perhaps the biggest difference is around the cutline definition. Flexible circuits provide unlimited configuration opportunities that often results in very odd shapes and sizes. Circuit boards often are rectangular or may have some notches or curved outlines routered. Because of this nuance, steel rule dies and hard tool dies are probably used more often for flexible PCBs than for boards, at least for ultra-high-volume applications. Laser definition of the circuit outline is also a common flex circuit process. Other differences in tooling involve fixturing that may be required to handle flexible substrates.
Coverlay/Covercoat
Flexible PCBs require different dielectric materials such as flexible photoimagable soldermask or laminated coverlay (also called coverfilm) vs. the non-flexible PCBs. This creates materials with unique properties and challenges. Materials need to bend and flex, with some applications requiring millions of cycles, without cracking or delaminating. Several design features need to be considered with dynamic flex applications, including: copper grain direction, circuit pattern layout, coverfilm thickness, and trace geometries. The most common flexible dielectric is laminated film dielectric bonded to the substrate with high temperature and pressure, a solution rarely used for rigid PCBs.
Applications
Flexible PCBs constitute about 10–15% of all PCBs produce globally, so there are far more applications that use hardboards than flex. The biggest advantage for flex is that it can reduce the size, weight and amount of hardware used for many electronic packages. It is best described as an “electronic interconnect packaging solution.” The concept of an “origami flex circuit” also comes to mind. If you have an application that requires multiple planes of interconnections, or there are active bending or flexing requirements for parts of the package, then a flexible PCB may be your best choice.
References
Dave Becker is vice president of sales and marketing at All Flex Flexible Circuits LLC.
Testimonial
"Our marketing partnership with I-Connect007 is already delivering. Just a day after our press release went live, we received a direct inquiry about our updated products!"
Rachael Temple - AlltematedSuggested Items
How Good Design Enables Sustainable PCBs
08/21/2025 | Gerry Partida, Summit InterconnectSustainability has become a key focus for PCB companies seeking to reduce waste, conserve energy, and optimize resources. While many discussions on sustainability center around materials or energy-efficient processes, PCB design is an often overlooked factor that lies at the heart of manufacturing. Good design practices, especially those based on established IPC standards, play a central role in enabling sustainable PCB production. By ensuring designs are manufacturable and reliable, engineers can significantly reduce the environmental impact of their products.
50% Copper Tariffs, 100% Chip Uncertainty, and a Truce
08/19/2025 | Andy Shaughnessy, I-Connect007If you’re like me, tariffs were not on your radar screen until a few months ago, but now political rhetoric has turned to presidential action. Tariffs are front-page news with major developments coming directly from the Oval Office. These are not typical times. President Donald Trump campaigned on tariff reform, and he’s now busy revamping America’s tariff policy.
Global PCB Connections: Understanding the General Fabrication Process—A Designer’s Hidden Advantage
08/14/2025 | Markus Voeltz -- Column: Global PCB ConnectionsDesigners don’t need to become fabricators, but understanding the basics of PCB fabrication can save you time, money, and frustration. The more you understand what’s happening on the shop floor, the better you’ll be able to prevent downstream issues. As you move into more advanced designs like HDI, flex circuits, stacked vias, and embedded components, this foundational knowledge becomes even more critical. Remember: the fabricator is your partner.
MKS’ Atotech to Participate in IPCA Electronics Expo 2025
08/11/2025 | AtotechMKS Inc., a global provider of enabling technologies that transform our world, announced that its strategic brands ESI® (laser systems) and Atotech® (process chemicals, equipment, software, and services) will showcase their latest range of leading manufacturing solutions for printed circuit board (PCB) and package substrate manufacturing at the upcoming 17th IPCA Show to be held at Pragati Maidan, New Delhi from August 21-23, 2025.
MKS Showcases Next-generation PCB Manufacturing Solutions at the Thailand Electronics Circuit Asia 2025
08/06/2025 | MKS Instruments, Inc.MKS Inc, a global provider of enabling technologies that transform our world, today announced its participation in Thailand Electronics Circuit Asia 2025 (THECA 2025), taking place August 20–22 at BITEC in Bangkok.