Catching up with Winonics’ Mark Eazell
December 11, 2015 | Dan Beaulieu, D.B. Management GroupEstimated reading time: 8 minutes
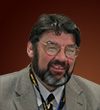
I have always thought of Winonics as one of the hidden gems of the North American PCB industry. Their well-equipped and well-laid-out facility in Brea, California is one of the more impressive looking PCB facilities in North America today.
Winonics is one of three PCB companies owned by JR Controls, the other two being Cosmotronic and Bench2Bench. I had the opportunity to talk with Mark Eazell, the general manager at Winonics, who also oversees the operation of all three JR Controls’ PCB companies.
Dan Beaulieu: Mark, tell me about Winonics.
Mark Eazell: Winonics Inc. is a part of the JR Controls Inc. family of circuit board fabrication facilities. JR Controls, located in Ontario, California, is owned by Rod Savage, who is the company president and chairman. Mr. Savage founded JR Controls in 1970 and has been involved with the circuit board industry since then. Mr. Savage started his career in the United States Air Force, so the company is recognized as a Veteran Owned Small Business.
Beaulieu: So you said there are a number of companies in JR Controls. Can you tell me about those please?
Eazell: Mr. Savage started in the industry in the late ‘60s and has owned a number of PCB manufacturing facilities over the years, starting with Winonics Fullerton (est. 1967), and including JR Controls (founded in 1970 as parent company). He acquired Cosmotronic in 2006 and then founded Bench2Bench in 2008. Those three PCB manufacturing companies, along with West Coast Enterprises, a PCB laminate and materials distributor, currently make up the JR Controls companies. He has also owned a number of other companies over the years, including Darby Circuits, Super-Tech, JR Utah, and Winonics Texas, all of which were consolidated into the companies we have today.
Beaulieu: Winonics is one very well-equipped facility. What are your capabilities?
Eazell: Winonics offers three mil lines and spaces, multilayer PCBs with 2–30+ layers, controlled impedance, stacked microvias, and via-filling. We also offer a wide variety of surface finishes (many of which are RoHS compliant) and a wide variety of base materials with UL approval, bromine-free, and high Tg. Winonics has a host of in-house processes including laser drilling, LDI imaging, lamination, via-fill, HASL, AG and ENIG finishes, CAD/CAM department, wet lab for cross-sections, and countless others, all internal at our facility. Having all of these processes in-house means a faster turn time and tighter controls. We also have two staggered shifts for manufacturing, allowing PCBs to move through the facility even faster.
Beaulieu: Mark, I am always interested in how people started in the industry. What is your story?
Eazell: In 1980, I started straight out of high school working for Mr. Savage at his Fullerton facility. I started at Winonics as an NC driller and worked my way up to programmer and finally drill room supervisor. I left in 1988 to pursue the dream of business ownership in the graphics and printing industry. On meeting with Mr. Savage in 1995, with much trepidation, I decided to sell my shares in that business and return to Winonics at the newly acquired Brea facility. I again started as a drill room supervisor, which in time was expanded to cover fabrication and AOI. Several years later, I was given the opportunity to move into procurement. In time, I was asked to handle shop operations and finally promoted to General Manager. Looking back, I still find it hard to believe it has been a total of 28 years working for Winonics. Time sure flies!
Beaulieu: I guess you made the right move when you came back then?
Eazell: Yes, I would say so.
Beaulieu: So what was the industry like when you started in 1980?
Eazell: Well, in the drill room at least, I remember being amazed at how small a 20-mil hole appeared. Also, how sophisticated bombsite programming and punched drill tape seemed to be. LOL. Amazing to think how far the industry has come with standard mechanical drilled holes now being 8–10 mils and even 6-mil in some cases. Not to mention the 4-mil and under laser microvias.
Beaulieu: What is Winonics forte—what are you good at?
Eazell: Winonics has provided an Alpha to Omega production model, meaning we provide engineering assistance, recommendations, and DFM and DRC for all multilayer PCBs we produce. We feel that quality electronics assemblies stem from quality PCBs, and the process starts with good planning and engineering. We excel at on-time delivery of a quality product.
Beaulieu: Mark, since there are actually three different PCB manufacturing companies that are part of the JR Controls organization, can you spend some time talking about each of them?
Eazell: Sure, let’s start with Winonics. Although Winonics was founded in 1967, the Brea facility was established in 1992 as a provider of rigid multilayer circuit boards, IPC 6012 class 2 & 3, serving the commercial marketplace. Winonics is ISO and AS9100C certified, UL 94VO, and ITAR registered.
Then there is Bench2Bench. While this Fullerton, California facility was founded in 1967, the Bench2Bench name was adopted in 2008. Bench2Bench (B2B) was founded on the idea that ultra-high-density interconnects require special expertise and handling, unique engineering considerations and close working relationships between customer and provider. The products built here are not your average PCBs, but are fully custom flex circuitry with ultra-fine features. These circuits can be used in a variety of applications, with special opportunities for use in the medical market. The process of revamping the Fullerton facility to accommodate this product mix has been quite extensive and required a complete overhaul of the existing 30,000 sq. ft. building. From the class 10,000 clean room with laser direct imaging, to the plasma etching equipment and laser drill, the facility and staff are ready to produce.
And finally, Cosmotronic was originally a family owned business started by its founder Said Cohen. Mr. Cohen made the difficult decision to sell Cosmotronic to Thayer Capital in 2001. Thayer subsequently sold the operation to its current owner, JR Controls Inc. in 2006. Cosmotronic is now part of a three-plant organization that specializes in providing a variety of printed circuit board solutions to a broad customer base. Cosmotronic continues to provide high-reliability rigid, rigid-flex and flex circuits to the defense/aerospace marketplace. They specialize in metal core, bonded heat sinks and heavy copper. They are ISO and AS9100C certified, ITAR registered and have just about every mil spec required to build complex circuits.
Beaulieu: Can you talk about the advantages of having three shops in one company?
Page 1 of 2
Testimonial
"Advertising in PCB007 Magazine has been a great way to showcase our bare board testers to the right audience. The I-Connect007 team makes the process smooth and professional. We’re proud to be featured in such a trusted publication."
Klaus Koziol - atgSuggested Items
How Good Design Enables Sustainable PCBs
08/21/2025 | Gerry Partida, Summit InterconnectSustainability has become a key focus for PCB companies seeking to reduce waste, conserve energy, and optimize resources. While many discussions on sustainability center around materials or energy-efficient processes, PCB design is an often overlooked factor that lies at the heart of manufacturing. Good design practices, especially those based on established IPC standards, play a central role in enabling sustainable PCB production. By ensuring designs are manufacturable and reliable, engineers can significantly reduce the environmental impact of their products.
50% Copper Tariffs, 100% Chip Uncertainty, and a Truce
08/19/2025 | Andy Shaughnessy, I-Connect007If you’re like me, tariffs were not on your radar screen until a few months ago, but now political rhetoric has turned to presidential action. Tariffs are front-page news with major developments coming directly from the Oval Office. These are not typical times. President Donald Trump campaigned on tariff reform, and he’s now busy revamping America’s tariff policy.
Global PCB Connections: Understanding the General Fabrication Process—A Designer’s Hidden Advantage
08/14/2025 | Markus Voeltz -- Column: Global PCB ConnectionsDesigners don’t need to become fabricators, but understanding the basics of PCB fabrication can save you time, money, and frustration. The more you understand what’s happening on the shop floor, the better you’ll be able to prevent downstream issues. As you move into more advanced designs like HDI, flex circuits, stacked vias, and embedded components, this foundational knowledge becomes even more critical. Remember: the fabricator is your partner.
MKS’ Atotech to Participate in IPCA Electronics Expo 2025
08/11/2025 | AtotechMKS Inc., a global provider of enabling technologies that transform our world, announced that its strategic brands ESI® (laser systems) and Atotech® (process chemicals, equipment, software, and services) will showcase their latest range of leading manufacturing solutions for printed circuit board (PCB) and package substrate manufacturing at the upcoming 17th IPCA Show to be held at Pragati Maidan, New Delhi from August 21-23, 2025.
MKS Showcases Next-generation PCB Manufacturing Solutions at the Thailand Electronics Circuit Asia 2025
08/06/2025 | MKS Instruments, Inc.MKS Inc, a global provider of enabling technologies that transform our world, today announced its participation in Thailand Electronics Circuit Asia 2025 (THECA 2025), taking place August 20–22 at BITEC in Bangkok.