-
-
News
News Highlights
- Books
Featured Books
- smt007 Magazine
Latest Issues
Current IssueWhat's Your Sweet Spot?
Are you in a niche that’s growing or shrinking? Is it time to reassess and refocus? We spotlight companies thriving by redefining or reinforcing their niche. What are their insights?
Moving Forward With Confidence
In this issue, we focus on sales and quoting, workforce training, new IPC leadership in the U.S. and Canada, the effects of tariffs, CFX standards, and much more—all designed to provide perspective as you move through the cloud bank of today's shifting economic market.
Intelligent Test and Inspection
Are you ready to explore the cutting-edge advancements shaping the electronics manufacturing industry? The May 2025 issue of SMT007 Magazine is packed with insights, innovations, and expert perspectives that you won’t want to miss.
- Articles
- Columns
- Links
- Media kit
||| MENU - smt007 Magazine
Alpha Talks Challenges of Solder Recycling
December 22, 2015 | Patty Goldman, I-Connect007Estimated reading time: 13 minutes
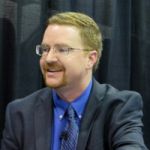
I had the opportunity to meet and chat with Jason Fullerton, a customer technical support engineer with Alpha. We talked about his presentation on recycling solder and why doing this in-house is not a good idea. We also talked about the new, smaller particle solder pastes and about Alpha’s recycling program that must really benefit their customers.
Patty Goldman: I understand you presented a paper here at SMTAI. Perhaps you want to start with a little bit about your company or yourself and give us a little overview here.
Jason Fullerton: Sure, Alpha is one of the world's leading manufacturers and distributors of electronics interconnect materials. We specialize in solder and solder alloys and other chemicals used in the interconnect field, fluxes, materials like that.
I am a customer tech support engineer. My territory is the United States and Canada. I work with our customers on the application side. I help them use their materials properly, help them optimize their processes for used materials, and help them select new materials for new products or to update the products they're currently using. My background is a manufacturing engineer in the industry, so I once actually did the jobs that my customers do.
Goldman: That's nice.
Fullerton: I have experience with their jobs so I can help them more by consulting to our entire customer base. We essentially have engineers that are there to help them use their materials and run their processes as efficiently as possible.
Goldman: Because if they do well, you do well.
Fullerton: Exactly. They do well, they buy more of our materials and we do well. Everybody's happy.
Goldman: Everybody's happy. So you presented a paper that had to do with recycling?
Fullerton: Yes. The paper was comparing the properties of commercially available solder—which is controlled by pretty stringent specifications on purity and content—versus materials that result from a user recovery process. There is equipment on the market that can take their waste product from a user’s wave solder equipment, process that through another piece of equipment and the result is some waste and some metal bar that these users will now put back into their solder machines, that they’ll remelt and use again.
Goldman: So they've reduced their waste.
Fullerton: Well, they do; but the material that they're putting back into the machine is not the same as commercially available solder. It doesn't have the same level of purity. It has more contaminants. Dross inclusion is the biggest one that we have found.
Dross and oxides are formed when metals react with the oxygen around it, and that's a waste product the user can't use anymore. They'll take this material off. They'll squeeze it under heat and pressure in this piece of equipment. Then they'll get a bar. Well, this bar has pretty high dross content. We did a benchmark study some years back and we found that even the worst commercially available solder had less than 1% dross inclusion by weight in tin-lead solder. The alloy that we studied, the product of this recycling process, had about 12.4% dross by weight. That's an order of magnitude higher. Dross is not solder, it's pure waste. For every eight pounds of bar that came out of this machine, only seven pounds of it was actually useful metal. The other pound was useless and a waste product that's a contaminant in the solder process.
Goldman: Now suppose somebody tries to use that bar. What kind of problems do they have?
Fullerton: That's one of things we covered in the paper. One of the biggest issues is that with that level of dross content being put back into the solder machine, which can manifest as dross pumped up through the solder weight and then contacts the board. That can cause bridging in certain areas. It can also build up inside the hardware and inside the machine. Every six months or so, wave solder users have to take hundreds of pounds of hardware out and scrape them off. It's almost like taking barnacles off of a ship, having to scrape off all this dross. If they're putting more dross in than the raw material, they're going to get more buildup more quickly on the equipment.
It can increase the effort in maintenance. It can increase the frequency of this maintenance being required. This maintenance is pretty arduous. It's a 4–8 hour task to do this kind of maintenance. You want to put it off as long as you can. Adding this material with this contaminant level in there may increase the frequency of those, and that can be a significant problem for users.
Goldman: What's the outcome of this?
Fullerton: We found that the dross was a pretty significant problem. We actually saw another issue where we looked at the actual metal content of the bar. There are pretty strict specifications on the purity of the solder we sell to our customers. The alloy that comes out of this process, in some cases meets the specification, but they're very close to the specification limits. This can cause the users to dilute the tin, for example, in their solder machines, which eventually could make the machine alloy go out of specification itself.
Goldman: So it's not quite right. The recycled bars are not at the optimum levels or they all have different metal contents.
Fullerton: Right, this bar and that bar are not the same thing but the user treats them like they are the same thing. That's what we want to raise the awareness of. Now the alternative is why we have the incentive to write a paper like this. The alternative is that major solder manufacturers already have recycling and reclamation services.
In fact, we actually have a booth here just for reclamation services, separate from our main corporate booth. We'll take the dross from the user and we'll pay them for that material. We'll process the material and break it down into the units of tin and lead and silver and copper. We’ll use those pure materials and make new alloy and sell that as a pure alloy again.
Goldman: That really cleans it up.
Fullerton: We provide our customers with certification that the material is recycled—not put in a landfill, for example. It helps ensure they can comply with their environmental regulations by tracking and reducing their waste output in their processes. We will pay the customers for what is essentially useless waste to them. Some companies take it for free. Some companies actually charge users to take this material away. We'll pay them for it and take it away and prove to their environmental regulators that we safely transferred it back into new product or back into another circuit board.
Goldman: That should be important to your customers.
Fullerton: Absolutely. It's important to our customers. It's important to us too, because it's a way we can prevent having to use ore. It's a way for us to insulate ourselves from conflict mineral issues by using recycled materials as part of our raw material set. We have to take less from the environment, and from the world. There’s less risk of damaging the environment through the mining of these minerals that we use.
Page 1 of 3
Suggested Items
Knocking Down the Bone Pile: Addressing End-of-life Component Solderability Issues, Part 4
07/15/2025 | Nash Bell -- Column: Knocking Down the Bone PileIn 1983, the Department of Defense identified that over 40% of military electronic system failures in the field were electrical, with approximately 50% attributed to poor solder connections. Investigations revealed that plated finishes, typically nickel or tin, were porous and non-intermetallic.
SHENMAO Strengthens Semiconductor Capabilities with Acquisition of PMTC
07/10/2025 | SHENMAOSHENMAO America, Inc. has announced the acquisition of Profound Material Technology Co., Ltd. (PMTC), a premier Taiwan-based manufacturer of high-performance solder balls for semiconductor packaging.
KYZEN to Highlight Understencil and PCB Cleaners at SMTA Querétaro Expo and Tech Forum
07/09/2025 | KYZEN'KYZEN, the global leader in innovative environmentally responsible cleaning chemistries, will exhibit at the SMTA Querétaro Expo & Tech Forum, scheduled to take place Thursday, July 24, at Centro de Congresos y Teatro Metropolitano de Querétaro.
Driving Innovation: Direct Imaging vs. Conventional Exposure
07/01/2025 | Simon Khesin -- Column: Driving InnovationMy first camera used Kodak film. I even experimented with developing photos in the bathroom, though I usually dropped the film off at a Kodak center and received the prints two weeks later, only to discover that some images were out of focus or poorly framed. Today, every smartphone contains a high-quality camera capable of producing stunning images instantly.
Hands-On Demos Now Available for Apollo Seiko’s EF and AF Selective Soldering Lines
06/30/2025 | Apollo SeikoApollo Seiko, a leading innovator in soldering technology, is excited to spotlight its expanded lineup of EF and AF Series Selective Soldering Systems, now available for live demonstrations in its newly dedicated demo room.