-
-
News
News Highlights
- Books
Featured Books
- smt007 Magazine
Latest Issues
Current IssueIntelligent Test and Inspection
Are you ready to explore the cutting-edge advancements shaping the electronics manufacturing industry? The May 2025 issue of SMT007 Magazine is packed with insights, innovations, and expert perspectives that you won’t want to miss.
Do You Have X-ray Vision?
Has X-ray’s time finally come in electronics manufacturing? Join us in this issue of SMT007 Magazine, where we answer this question and others to bring more efficiency to your bottom line.
IPC APEX EXPO 2025: A Preview
It’s that time again. If you’re going to Anaheim for IPC APEX EXPO 2025, we’ll see you there. In the meantime, consider this issue of SMT007 Magazine to be your golden ticket to planning the show.
- Articles
- Columns
Search Console
- Links
- Media kit
||| MENU - smt007 Magazine
Nordson EFD Discusses Dispensing Technologies, Solder Reliability and Innovation
January 8, 2016 | Barry Matties and Stephen Las Marias, I-Connect007Estimated reading time: 7 minutes
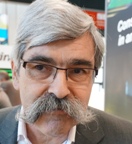
In an interview with I-Connect007, Philippe Mysson, business development manager for solder paste at Nordson EFD, discusses a host of solder-related issues, including reliability, the benefits of solder paste dispensing systems, challenges facing their customers and how Nordson EFD is helping to address those issues, and finally, latest trends driving innovation in solder alloys.
Barry Matties: Tell us a little bit about what you do at Nordson EFD.
Philippe Mysson: As a business development manager for solder paste in Europe. Basically, solder paste is a technical product, so we need to ship it off to all our sales team and help them select the right solder paste according to the requirements of the customer, because we can propose many different alloys with many different melting points and also many different type of flux. According to the specific needs of the customer, we gauge them and propose the right paste.
After that, there are two ways of applying the paste on the PCB. The first one is screen printing, in which a stencil with holes has paste pushed through it with a squeegee. We are the company that makes the dispensing system. We make solder paste, but our main products are for dispensing. It's a little bit different because you have to actually make one dot by one dot. The main difference with the stencil printing is that you are making hundreds of them at the same time, but it's not really flexible. You have to change the stencil according to the design of your PCB and so forth.
People are using dispensers for many different applications like connectors, components, and semiconductors. Dispensing paste is different than printing paste. You need to have specific flux because if you have, for example, a bubble inside, you will dispense air and no paste. When you have a big machine dispensing solder paste, and there is no more solder paste dispensing, you will have a problem. That's why you need to have a specific paste design for the dispensing application.
Matties: For the screen application, that's a very fast cycle time and great for high volume?
Mysson: Exactly.
Matties: For the dispensing, maybe for a high mix, low-volume application?
Mysson: Yes, that will be more of a niche application. I would say it's very application specific. The customer might have a specific product and wants to have a dedicated solution. His dispensing system would be chosen according to the reliabilities and the quantity of paste he wants to put on the product. We have to propose the right paste according to the requirement, so that can be a paste with a low melting point tolerance or a high melting point tolerance. The size of it can vary and the speed can vary. They can ask to have very high-speed dispensing, with around 80 dots per minute.
Matties: In the dispensing system, do you have built-in inspection for this or does that go in after, offline?
Mysson: The ideal situation is that you dispense, and you have a camera that is checking the amount of paste you are dispensing. After you have the reflow and need to check that the solder has been correctly melted. In summary if you put the right amount of paste and if you reflow it properly you will have a correct solder joint.
Matties: What sort of demands are your customers putting on you these days? Because there's a lot of paste on the market that they can choose from, and presumably they all achieve the end results.
Mysson: Yes, they just want a solution. They do not want anything to do with solder paste. They want to put it on the machine and forget it.
Matties: Are they looking for a solutions provider that has a quality product?
Mysson: Exactly. For example, people are asking about soldering flexible circuits for automotive applications but they are not experts in solder paste. We are there to help them select the right product. For example, for flexible components they will need to use a specific alloy with a low melting point so that they will not destroy the plastic, and so on. They are not specialists in solder paste. We are the specialists in solder paste and dispensing and we are there to help them find the right solution.
Stephen Las Marias: Philippe, we did a survey on reliability and one of the issues highlighted by our readers was solder joint reliability. I know you're a solder paste provider, but as a stakeholder in that supply chain, how do you make sure that your products can help your customers achieve the reliability that they're looking for?
Mysson: When we are manufacturing the paste, we have norms to respect. We are doing tests that check, for example, that the paste will not have corrosion during the life of the solder joint. The tests and reliability are different for each of our customers, depending on the application of their final product. Everything won’t need the same tests as automotive, for example, which asks for validation and thermal cycling tests. When it's a specific test that we are doing our job is to propose the right paste that we know will work for this particular application, because all tests can be different.
The test will not be the same for LED, semiconductor, and automotive connectors. For automotive connectors it will be important to test and double check to be sure that in the car you will not destroy your solder joint. For solar panels, it will be an environmental test to be sure that the panel will not be destroyed after ten years on the roof.
Our advantage is that we have a wide view of the market, so when somebody's coming from automotive, we know which paste is working well for that application and we can propose it. After that, it’s the job of our customer to make the appropriate test, validate our paste, and validate the final product. We are not validating the product for them. We are proposing a paste according to our norm and our tests. It's up to the customer to make the test and check that the final product is a well processed application. However, we work in cooperation with their technical staff and follow them through the process of checking the test, and so on. We are supporting them in this process.
Las Marias: One of the trends that I am seeing in solder paste development is that first we became lead free, and now some customers are requesting no-silver or low-silver solutions, because of cost. What is your comment on that, and what strategies are you employing in your product development?
Mysson: Of course, the cost of silver is something like $450 per kilo, so if you have 3% silver, just the cost of the silver will represent $13.50. Yes, we are proposing some low content silver alloys. Also, we are proposing a totally silver-free alloy which is tin copper, and is 99.3% tin and 0.7% copper. This will be popular especially in places like Russia, for example, where any alloy that has more than 2% of silver is considered like jewelry, and they tax it like jewelry, so it's rarely possible to sell solder paste with more than 2% silver. That's why we are proposing the tin copper alloy, because there is no silver inside.
Las Marias: What will be the advantages or disadvantages if you're proposing a different type of alloy in their applications?
Mysson: The first thing is the melting point of the alloy. After that, it has some mechanical strength for the different requirements of the customer. We need to know exactly what the customer wants to do. Of course if it's not an issue, we can propose silver because it will have better mechanical strength and so on. For example, our Tin Bismuth alloy, which is a low melting point alloy, is used to solder on plastic or film and so on, but the mechanical strength was not big enough, so now we put some small amount of silver inside, 0.4%, to have better mechanical strength. Again, it all depends of the requirements of our customer.
Las Marias: Can you tell us some of the latest process developments that are impacting the development of solder paste other than screen printing and dispensing?
Mysson: Now it's jetting— people want to go to jet and decrease the size of the jets. Now the challenge is to have smaller and smaller products, so now we are talking about 300 micron dots for one or two millimeters. We need to use a very small powder, type six or type seven. It's the future to decrease the size of the product. The second challenge will be the flux itself, because now the people are asking to have halide free fluxes, so it's more difficult to wet and to solder correctly with flux, which has no more halides inside. It's another challenge. We are obliged to have very small dots so with this specific low tolerance solder paste, the wetting will be not so good. These are two big challenges that we are seeing.
Las Marias: It's a constantly developing market.
Mysson: It is, and the products are changing very quickly. In the past you had big products, and now we have very small ones. You can imagine the solder joints inside are becoming smaller and smaller.
Matties: Thank you very much for your time, Philippe.
Mysson: Thank you.
Suggested Items
KYZEN to Focus on Aqueous Cleaning and Stencil Cleaning at SMTA Juarez
05/20/2025 | KYZEN'KYZEN, the global leader in innovative environmentally responsible cleaning chemistries, will exhibit at the SMTA Juarez Expo and Tech Forum, scheduled to take place Thursday, June 5 at the Injectronics Convention Center in Ciudad Jarez, Chihuahua.
Koh Young Installs 24,000th Inspection System at Top 20 EMS
05/14/2025 | Koh YoungKoh Young, the global leader in True 3D measurement-based inspection and metrology solutions, proudly announces the installation of its 24,000th inspection system at a Top 20 Global EMS in Thailand.
Indium’s Karthik Vijay to Present on Dual Alloy Solder Paste Systems at SMTA’s Electronics in Harsh Environments Conference
05/06/2025 | Indium CorporationIndium Corporation Technical Manager, Europe, Africa, and the Middle East Karthik Vijay will deliver a technical presentation on dual alloy solder paste systems at SMTA’s Electronics in Harsh Environments Conference, May 20-22 in Amsterdam, Netherlands.
SolderKing Achieves the Prestigious King’s Award for Enterprise in International Trade
05/06/2025 | SolderKingSolderKing Assembly Materials Ltd, a leading British manufacturer of high-performance soldering materials and consumables, has been honoured with a King’s Award for Enterprise, one of the UK’s most respected business honours.
Knocking Down the Bone Pile: Gold Mitigation for Class 2 Electronics
05/07/2025 | Nash Bell -- Column: Knocking Down the Bone PileIn electronic assemblies, the integrity of connections between components is paramount for ensuring reliability and performance. Gold embrittlement and dissolution are two critical phenomena that can compromise this integrity. Gold embrittlement occurs when gold diffuses into solder joints or alloys, resulting in mechanical brittleness and an increased susceptibility to cracking. Conversely, gold dissolution involves the melting away of gold into solder or metal matrices, potentially altering the electrical and mechanical properties of the joint.