-
-
News
News Highlights
- Books
Featured Books
- smt007 Magazine
Latest Issues
Current IssueIntelligent Test and Inspection
Are you ready to explore the cutting-edge advancements shaping the electronics manufacturing industry? The May 2025 issue of SMT007 Magazine is packed with insights, innovations, and expert perspectives that you won’t want to miss.
Do You Have X-ray Vision?
Has X-ray’s time finally come in electronics manufacturing? Join us in this issue of SMT007 Magazine, where we answer this question and others to bring more efficiency to your bottom line.
IPC APEX EXPO 2025: A Preview
It’s that time again. If you’re going to Anaheim for IPC APEX EXPO 2025, we’ll see you there. In the meantime, consider this issue of SMT007 Magazine to be your golden ticket to planning the show.
- Articles
- Columns
Search Console
- Links
- Media kit
||| MENU - smt007 Magazine
Lost in the System: How Traceability can Solve the Problem of Counterfeit Materials
January 15, 2016 | Michael Ford, Mentor Graphics Valor DivisionEstimated reading time: 3 minutes
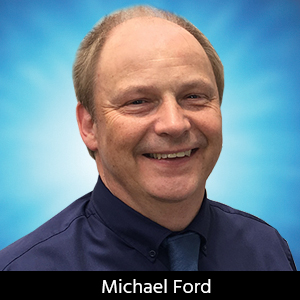
The word "counterfeit" encompasses a wide range of activities that are happening continuously in an "underground” SMT supply chain. The risks and potential effects resulting from the use of counterfeit materials can be huge, threatening human life, as well as the success of any company in the electronics industry. Word on the street is that the occurrence of counterfeit materials is growing rapidly, which means, at some point, a critical mass will be reached. The best managers and engineers among us must surely realize that now is the time to get proactive on this issue before a serious compelling event occurs. Let's play detective and investigate this dark side of manufacturing to try and find out what exactly can be done.
The classic plot of any detective story is the task of discovering the motive, means, and opportunity for the crime. In business, the motive is focused on the financial aspects of materials supply. After all, materials generally are 80–90% of the cost of a finished product. As manufacturing costs decrease, the material costs become more significant. For example, shaving a cent or two off the cost of material in each product can be significant when scaled up to the level of materials used in high-volume consumer products. At the other end of the scale, many individual materials have a high enough value to be a target for counterfeiting even when used in lower volumes.
As well as the physical properties of the materials, test and qualification processes add value to a material, differentiating it from otherwise identical materials. In critical applications, materials that have not been through prescribed testing or have not been handled in an approved way are disqualified from use.
Motivation
As a result of these pressures, the motivation to reduce material costs can encompass:
• Vendor cloning: There are many choices of materials manufacturers, and some have better quality or consistent products, which are also more expensive. The golden rule is to select the level of quality needed at the lowest price available. Substituting lower cost materials in volume, however, can make a considerable financial difference.
• Test failures: In testing materials during manufacture, some will inevitably fail. Electrical properties may fall outside of control parameters, or stress testing may reveal weaknesses. These failures create an opportunity for individual materials, groups of materials, or even a whole batch of materials to be scrapped or re-packaged as cheaper versions. This may not represent a huge cost to the original manufacturer, but the opportunity to make some extra money could be a significant motivation to anyone else involved in disposal or recycling.
• Trial materials: Materials made during the setting up of manufacturing processes, or samples generated, could also be intercepted in the disposal process and re-sold.
• Dirty materials: It is not only in the material manufacture and supply-chain process that counterfeit materials can be introduced. Spoilage generated during assembly production can also be inappropriately used. For example, materials that have been rejected by the SMT processes and discarded may be gathered up and recycled back into the machine at a later time. The handling of these materials outside of the supply-chain rules introduces risk of contamination from dirt and water. In many situations, refurbishing materials is acceptable, but in a situation where an acute shortage of materials happens at the end of a production run because of unexpectedly high spoilage can be a great motivator to simply pick up discarded materials and put them in a tray for re-use. These are also counterfeit because they deviate from the approved supply procedure.
• “Garage” materials: Some materials are made specifically with the intent to replace authorized materials. The classic situation is an entrepreneur who buys an out-dated manufacturing process that he sets up in a garage to churn out materials made with substandard raw materials, often without testing. The intent is simply to make the materials as cheaply as possible and then find a way to introduce them as genuine materials in the supply chain.
Editor's Note: This article originally appeared in the January 2016 issue of SMT Magazine.
Suggested Items
Electroninks Acquires Complete UTDots Advanced Materials Nanoinks Portfolio and IP
05/19/2025 | ElectroninksElectroninks, the leader in metal organic decomposition (MOD) inks for additive manufacturing and advanced semiconductor packaging, announced it has officially completed its full acquisition of UTDots products and IP into its portfolio, further expanding its offerings in digital printing for high-performance applications.
Future-proofing Electronics: ChemFORWARD Works Toward Collaboration for Safer Chemistry
05/19/2025 | Rachel Simon, ChemFORWARDThe electronics industry is facing a critical juncture. As consumer demand for sustainable products rises and regulatory pressures intensify, companies must prioritize the safety of their products and processes. This means not only complying with evolving chemical restrictions but also proactively seeking safer alternatives.
From DuPont to Qnity: A Bold Move in Electronics Materials
05/14/2025 | Marcy LaRont, I-Connect007DuPont has announced the intended spinoff of a public independent electronics company, Qnity, which will serve as a solutions provider to the semiconductor and electronics industries to enhance competitiveness and innovation in advanced computing, smart technologies, and connectivity. In this interview, Jon Kemp, Qnity CEO-elect and current president of DuPont’s Electronics business, shares his insights on the strategic separation from DuPont.
SMC Korea 2025 to Spotlight Next-Generation Memory and Materials Innovation amid AI Boom
05/13/2025 | SEMIThe Strategic Materials Conference (SMC) Korea 2025 is set to convene on May 14 at the Suwon Convention Center in Gyeonggi-do, South Korea, bringing together leading experts and innovators to highlight the critical role of materials innovation in addressing the performance, efficiency, and scalability requirements of AI-enabled semiconductor devices.
SEMI Applauds New Bill to Clarify Tax Credit Eligibility for Critical Semiconductor Suppliers Under U.S. CHIPS Act
05/12/2025 | SEMISEMI, the industry association serving the global semiconductor and electronics design and manufacturing supply chain, announced support of the Strengthening Essential Manufacturing and Industrial Investment Act (SEMI Investment Act), which clarifies that critical materials suppliers to semiconductor manufacturers are eligible for the Advanced Manufacturing Investment Tax Credit (“Section 48D”) created by the United States CHIPS and Science Act.