-
- News
- Books
Featured Books
- pcb007 Magazine
Latest Issues
Current IssueInventing the Future with SEL
Two years after launching its state-of-the-art PCB facility, SEL shares lessons in vision, execution, and innovation, plus insights from industry icons and technology leaders shaping the future of PCB fabrication.
Sales: From Pitch to PO
From the first cold call to finally receiving that first purchase order, the July PCB007 Magazine breaks down some critical parts of the sales stack. To up your sales game, read on!
The Hole Truth: Via Integrity in an HDI World
From the drilled hole to registration across multiple sequential lamination cycles, to the quality of your copper plating, via reliability in an HDI world is becoming an ever-greater challenge. This month we look at “The Hole Truth,” from creating the “perfect” via to how you can assure via quality and reliability, the first time, every time.
- Articles
- Columns
- Links
- Media kit
||| MENU - pcb007 Magazine
Estimated reading time: 2 minutes
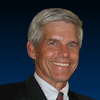
High-Temperature Performance Flexible Circuits
Markets requiring thermal exposure at elevated temperatures include down-hole oil drilling, semiconductor processing, medical diagnostics and a multitude of military/aerospace requirements. But a limitation of flexible circuitry has been performance at extremely high temperatures. For purposes of this discussion, the definition of “extremely high” is temperatures that exceed 150–200°C on a continuous basis or 288°C on an intermittent basis[1]. The flexible circuit industry has made inroads improving this product feature with recent developments and significantly improved high-temperature performance, which is being accomplished with new material constructions requiring some unique fabrication processing.
The adhesive system used to bond the various layers in a flexible circuit is normally considered the weakest link when parts are exposed to high temperature or a harsh chemical environment. This weakness has driven adoption of adhesiveless base laminate technology (the word “laminate” remains an industry term but is a bit misguiding when describing adhesiveless structures as they are not generally produced with a laminating process). Multiple methods for creating an adhesiveless base laminate substrates have become common (copper sputtering, vacuum deposition, cast polyimide) and provide improved performance in both extreme thermal and chemical environments.
But the most frequently used “top side” flexible circuit insulation is generally another layer of polyimide film commonly called coverlay or coverfilm. This layer of film is coated with an uncured adhesive and positioned onto the etched circuitry pattern and then permanently fastened during a temperature/pressure lamination cycle in a platen press. Consequently, an adhesive has been reintroduced into the circuit composite, despite removing the adhesive in the base substrate. Another top side dielectric used in the world of flexible printed circuits is a photo-imaged soldermask, but this material often becomes brittle at elevated temperatures, and can fracture or flake off when bent or folded.
New coverlay adhesive systems have been developed to withstand higher temperatures than 200°C. These coverlay adhesive systems, in combination with adhesiveless laminates, offer options for creating new flexible circuit composites suitable for high-temperature environments. This can require fabrication process technology that is not common within many printed circuit factories. Alternative material handling techniques may also be required. The flex-circuit industry has begun to commercialize this product capability for applications requiring performance at continuous operating temperatures of 250°C. Product development will continue in support of a growing marketplace demand for higher temperature applications.
The new set of high-temperature constructions pose few limitations; however, applications are unique and testing within a simulated end use environment is always a good discipline. A variety of constructions meeting UL flammability requirements are available, with many of the chemical and mechanical properties of these new constructions similar to the existing polyimide constructions used in military and commercial applications. While some of the many material constructions used for flexible circuit fabrication may have slightly different flexibility properties, the flex properties of the new materials are similar to traditional laminates.
With high-temperature applications continuing to grow in demand, materials and processes required to support these challenging applications are becoming available. Fabricators are stocking the materials required to provide quick-turn delivery and support adoption in high-performance applications. Be careful when you pick-up that flex circuit…you might get burned.
References
1. IPC TMM 2.4.13.1 solder float test for thermal stress of laminates.
Dave Becker is vice president of sales and marketing at All Flex Flexible Circuits LLC.
More Columns from All About Flex
All About Flex: Terms and ConditionsAll About Flex: ISO 9001 Basics
All About Flex: FAQs on UL Listings for Flexible Circuits
All About Flex: Avoiding Trace Fracturing in a Flexible Circuit
Polyimide vs. Silicone for Flexible Heaters
All About Flex: Copper Thickness Requirements for Flex Circuits
All About Flex: Copper Grain Direction
All About Flex: Options for Purchasing Flexible Heaters