Happy’s Essential Skills: The Need for Total Quality Control (Six Sigma and Statistical Tools), Part 2
February 3, 2016 | Happy HoldenEstimated reading time: 8 minutes
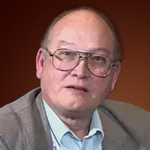
To read part one of this series, click here.
Six Sigma
Six Sigma is a disciplined, data-driven approach and methodology for eliminating defects (driving toward six standard deviations between the mean and the nearest specification limit) in any process—from manufacturing to transactional, and from product to service.
The statistical representation of Six Sigma describes quantitatively how a process is performing. To achieve Six Sigma, a process must not produce more than 3.4 defects per million opportunities. A Six Sigma defect is defined as anything outside of customer specifications. A Six Sigma opportunity is then the total quantity of chances for a defect.
The fundamental objective of the Six Sigma methodology is the implementation of a measurement-based strategy that focuses on process improvement and variation reduction through the application of Six Sigma improvement projects. This can be accomplished through two Six Sigma sub-methodologies: Business Process Management Systems (BPMS) and Six Sigma Improvement Methodologies: DMAIC and DMADV (Figure 1).
The Six Sigma DMAIC process (define, measure, analyze, improve, control) is an improvement system for existing business processes falling below specification and looking for incremental improvement. The Six Sigma DMADV process (define, measure, analyze, design, verify) is an improvement system used to develop new processes, products, or defining customer needs at Six Sigma quality levels. It is also called Design for Six Sigma (DFSS). It can also be employed if a current process requires more than just incremental improvement. Both Six Sigma processes are executed by Six Sigma Green Belts and Six Sigma Black Belts, and are overseen by Six Sigma Master Black Belts.
According to the Six Sigma Academy, black belts save companies approximately $230,000 per project and can complete four to six projects per year. General Electric, one of the most successful companies implementing Six Sigma, has estimated benefits on the order of $10 billion during the first five years of implementation. GE first began Six Sigma in 1995 after Motorola and Allied Signal blazed the Six Sigma trail. Since then, thousands of companies around the world have discovered the far-reaching benefits of Six Sigma.
Many frameworks exist for implementing the Six Sigma methodology. Six Sigma consultants all over the world have developed proprietary methodologies for implementing Six Sigma quality, based on the similar change management philosophies and applications of tools. A partial list of 18 framework and methodologies are listed here. Eight will be detailed in this and future columns in this magazine. Additionally, I have include 37 tools and templates in this column and seven more will be detailed in the future. Definitions and examples of all are available at the Six Sigma website[1].
Frameworks and Methodologies
- Balanced Scorecard
- Benchmarking*
- Business Process Management (BPM)*
- Design for Six Sigma (DFSS)*
- DMAIC
- Harada Method
- Hoshin Kanri
- Innovation
- Kaizen
- Lean*
- Metrics*
- Plan, Do, Check, Act*
- Project Management*
- Robust Design/Taguchi Method
- Theory of Constraints
- Total Quality Management (TQM)*
- VOC/Customer Focus
- Work-out
Figure 1: Six-Sigma process improvement through the DMAIC and DMADV methods (also called an affinity diagram): define, measure, analyze, improve/design, control/verify.
Six Sigma Tools & Templates[1]
- 5 Whys
- 5S
- Affinity Diagram/KJ Analysis*
- Analysis of Variance (ANOVA)
- Analytic Hierarchy Process (AHP)
- Brainstorming*
- Calculators
- Capability Indices/Process Capability
- Cause & Effect (fishbone)
- Control Charts
- Design of Experiments (DOE)*
- FMEA*
- Graphical Analysis Charts
- Hypothesis Testing
- Kanban
- Kano Analysis
- Measurement Systems Analysis (MSA)/Gage R&R
- Normality
- Pareto
- Poka Yoke
- Process Mapping
- Project Charter
- Pugh Matrix
- QFD/House of Quality*
- RACI Diagram
- Regression*
- Risk Management
- SIPOC/COPIS
- Sampling/Data
- Simulation
- Software
- Statistical Analysis*
- Surveys
- Templates
- Value Stream Mapping
- Variation
- Wizards
Statistical Methods
The Need for Statistical Tools
The discussion of quality and customer satisfaction show how important yields are to printed circuit boards. Any loss goes to the bottom line. So what are some of the tools to help improve process yields? Process control comes to mind. Chemical processes have always been difficult to control in printed circuits. These uncontrolled factors can always creep into our processes.
All process control is a feedback loop of some sort. Nevertheless, the element that I want to focus on is the control block, or more precisely, the human decisions that make up process control.
Process Control
The first link in process control is the human link. The high-level objectives are to:
- Reduce variations
- Increase first pass yields
- Reduce repair and rework
- Improve quality and reliability
- Improve workmanship
The process control tools and methods that a person may have to work with have been listed already. Of particular importance for the engineer are the statistical tools, as seen in Figure 2. Traditionally, statistical tools have been rather cumbersome and not easy to learn. I have good news: You can now get a good statistics training from the Web, at everyone’s favorite price— free.
Even if your company has good statistical software available, like mine did with Minitab, it is only available as long as you work there. By downloading the NIST/SEMATECH e-Handbook of Statistical Methods[2] and the software Dataplot, you have an equally good tool at home that can travel with you wherever you may work. Your next job may not have any statistical tools!
Page 1 of 2
Suggested Items
Knocking Down the Bone Pile: Addressing End-of-life Component Solderability Issues, Part 4
07/15/2025 | Nash Bell -- Column: Knocking Down the Bone PileIn 1983, the Department of Defense identified that over 40% of military electronic system failures in the field were electrical, with approximately 50% attributed to poor solder connections. Investigations revealed that plated finishes, typically nickel or tin, were porous and non-intermetallic.
Digital Twin Concept in Copper Electroplating Process Performance
07/11/2025 | Aga Franczak, Robrecht Belis, Elsyca N.V.PCB manufacturing involves transforming a design into a physical board while meeting specific requirements. Understanding these design specifications is crucial, as they directly impact the PCB's fabrication process, performance, and yield rate. One key design specification is copper thieving—the addition of “dummy” pads across the surface that are plated along with the features designed on the outer layers. The purpose of the process is to provide a uniform distribution of copper across the outer layers to make the plating current density and plating in the holes more uniform.
The Knowledge Base: A Conference for Cleaning and Coating of Mission-critical Electronics
07/08/2025 | Mike Konrad -- Column: The Knowledge BaseIn electronics manufacturing, there’s a dangerous misconception that cleaning and coating are standalone options, that they operate in different lanes, and that one can compensate for the other. Let’s clear that up now. Cleaning and conformal coating are not separate decisions. They are two chapters in the same story—the story of reliability.
SMT007 Magazine July—What’s Your Competitive Sweet Spot?
07/01/2025 | I-Connect007 Editorial TeamAre you in a niche that’s growing or shrinking? Is it time to reassess and refocus? We spotlight companies thriving by redefining or reinforcing their niche—what are their insights? In the July 2025 issue of SMT007 Magazine, we spotlight companies thriving by redefining or reinforcing their niche and offer insights to help you evaluate your own.
Smarter Machines Use AOI to Transform PCB Inspections
06/30/2025 | Marcy LaRont, PCB007 MagazineAs automated optical inspection (AOI) evolves from traditional end-of-process inspections to proactive, in-line solutions, the integration of AI and machine learning is revolutionizing defect reduction and enhancing yields, marking a pivotal shift in how quality is managed in manufacturing.