The Institute of Circuit Technology Tewkesbury Seminar, 1st March 2016
March 8, 2016 | Pete Starkey, I-Connect007Estimated reading time: 8 minutes
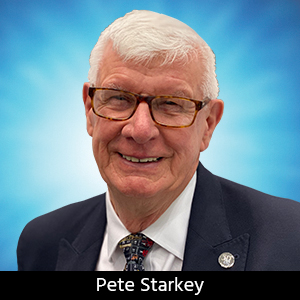
The Annual General Meeting of the Institute of Circuit Technology (ICT) was held at Puckrup Hall, near Tewkesbury in Gloucestershire, England, on 1st March 2016, and was followed by a well-attended evening seminar with presentations on a novel laser-induced deposition process, an analysis of the market for PCBs, and a review of three development projects in which the Institute had participated. The programme was introduced and moderated by ICT Technical Director Bill Wilkie.
Could laser-induced forward transfer (LIFT) offer a novel deposition process for PCBs?
Dr. James Shaw-Stewart, senior lecturer and researcher at Coventry University, gave an insight into the concept and applications of LIFT in transposing images from a donor substrate onto a receiver substrate. The transferred material could be a solid metallic or non-metallic film, or a liquid nano-ink, coated onto a sacrificial photosensitive layer on a transparent substrate. Ablation of the photosensitive layer by a laser caused transfer material to be propelled forward as “flyers,” and deposited on the receiver, placed a short distance away. A video illustration of an early example showed an 80 nanometre aluminium layer on a 350 nanometre photosensitive layer being successfully transferred across a 1 millimetre gap at a laser intensity of 270 milliJoules per cm2 and the efficiency of transfer increased as pressure was reduced from atmospheric. A further example demonstrated how a pulsed laser could be combined with a video image source to transfer a donor nano-ink to a substrate on an X-Y platform. The laser energy required to drive the transfer was significantly dependent on the viscosity of the ink.
LIFT techniques had been successfully used to build several different types of organic semiconductors, sensors and capacitors, and as a means of creating micro-bumps on flip-chip packages. The U.S. Naval Research Laboratories had demonstrated the capability to laser-print metals to form microbridges and microcantilevers. More recently, extreme-aspect-ratio copper structures had been deposited from a solid copper donor. Dr. Shaw-Stewart’s description prompted a question from the floor about the possibility of applying LIFT techniques to the repair of open circuits on PCBs and it was acknowledged that this was a topic worthy of investigation.
Dr. Shaw-Stewart concluded his presentation with “something a bit different”—a discussion of what could be accomplished by a technique known as scanned mask imaging (SMI), a development in which he was collaborating, which achieved excimer-style beam uniformity with cost-effective solid-state lasers. The system used a scanning 355 nanometre laser, with optics to shape the beam and project it onto a static substrate through a static photomask, to structure interconnects as fine as 3 micron lines and spaces with 10 micron vias. Scanned mask imaging had the potential to bridge the 1 micron to 10 micron “technology gap” between silicon wafer and PCB design rules in advanced packaging applications.
From imaging technology the attention turned to business forecasting. Market analyst and ICT council member Francesca Stern presented an outlook on the global PCB and electronics industry, beginning with an overview of trends in world electronics equipment production. Overall value in 2015 was about $1.5 trillion, almost unchanged from 2014, and distributed geographically: Asia 53%, North America 19%, Europe 15%, Japan 3%, and rest of world 10%. The forecast for 2016 was for a slight overall increase to $1.6 trillion.
Looking specifically at PCBs, world production in 2014 had been $60 billion, and this had declined about 3% in 2105 to an estimated $57.8 billion with slight growth in Europe and North America, no growth in Japan and a slight decline in South Korea and Taiwan. There had been a huge variation in the fortunes of the top twenty-five PCB fabricators in 2015, for example Fujikura showing as much as 46% growth whereas Daeduck’s figure was -22%, the overall average being 1.6% growth. Exchange rates could distort figures such that apparently positive growth measured in Asian domestic currencies could in fact be negative when converted to US dollars.
In terms of geographical distribution, of the $57.8 billion world PCB production total for 2015 China accounted for 46%, Europe 4%, and North America 5%. And the end market for PCBs was 45% in China, 10% in Europe and 8% in North America. The corresponding figures for 2016 were forecast to be $59 billion total, with production from China 46%, Europe 4% and North America 5%, supplying a market of which 46% in China, 10% in Europe and 8% in North America.
The outlook for the UK PCB industry was that the current downward trend would bottom-out mid-2016, and move into positive growth by the end of the year, peaking mid-2017 then cycle down again. European PCB production would follow a similar cycle, but with smaller peaks and troughs.
Back to technology developments, as Professor Martin Goosey took the floor with an update on ICT’s research and development projects, specifically the two current Innovate-UK funded programmes in which the Institute was the dissemination partner, STOWURC and MACFEST. (The acronyms stand for Sustainable Treatment of Waste Using Recycled Chitosans, and Manufacturing Advanced Coatings for Future Electronic Systems.) Page 1 of 2
Testimonial
"The I-Connect007 team is outstanding—kind, responsive, and a true marketing partner. Their design team created fresh, eye-catching ads, and their editorial support polished our content to let our brand shine. Thank you all! "
Sweeney Ng - CEE PCBSuggested Items
How Good Design Enables Sustainable PCBs
08/21/2025 | Gerry Partida, Summit InterconnectSustainability has become a key focus for PCB companies seeking to reduce waste, conserve energy, and optimize resources. While many discussions on sustainability center around materials or energy-efficient processes, PCB design is an often overlooked factor that lies at the heart of manufacturing. Good design practices, especially those based on established IPC standards, play a central role in enabling sustainable PCB production. By ensuring designs are manufacturable and reliable, engineers can significantly reduce the environmental impact of their products.
50% Copper Tariffs, 100% Chip Uncertainty, and a Truce
08/19/2025 | Andy Shaughnessy, I-Connect007If you’re like me, tariffs were not on your radar screen until a few months ago, but now political rhetoric has turned to presidential action. Tariffs are front-page news with major developments coming directly from the Oval Office. These are not typical times. President Donald Trump campaigned on tariff reform, and he’s now busy revamping America’s tariff policy.
Global PCB Connections: Understanding the General Fabrication Process—A Designer’s Hidden Advantage
08/14/2025 | Markus Voeltz -- Column: Global PCB ConnectionsDesigners don’t need to become fabricators, but understanding the basics of PCB fabrication can save you time, money, and frustration. The more you understand what’s happening on the shop floor, the better you’ll be able to prevent downstream issues. As you move into more advanced designs like HDI, flex circuits, stacked vias, and embedded components, this foundational knowledge becomes even more critical. Remember: the fabricator is your partner.
MKS’ Atotech to Participate in IPCA Electronics Expo 2025
08/11/2025 | AtotechMKS Inc., a global provider of enabling technologies that transform our world, announced that its strategic brands ESI® (laser systems) and Atotech® (process chemicals, equipment, software, and services) will showcase their latest range of leading manufacturing solutions for printed circuit board (PCB) and package substrate manufacturing at the upcoming 17th IPCA Show to be held at Pragati Maidan, New Delhi from August 21-23, 2025.
MKS Showcases Next-generation PCB Manufacturing Solutions at the Thailand Electronics Circuit Asia 2025
08/06/2025 | MKS Instruments, Inc.MKS Inc, a global provider of enabling technologies that transform our world, today announced its participation in Thailand Electronics Circuit Asia 2025 (THECA 2025), taking place August 20–22 at BITEC in Bangkok.