Researchers Develop Highly Efficient Hollow Copper Electrodes
March 9, 2016 | University of TwenteEstimated reading time: 3 minutes
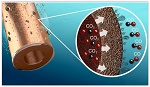
Scientists at the University of Twente research institute MESA+ have developed an electrode in the form of a hollow porous copper fibre which is able to convert carbon dioxide (CO2) into carbon monoxide (CO) extremely efficiently. In principle the invention enables a wide variety of industrial processes, for example in the steel industry, to be made more sustainable. The researchers have applied for a patent on their invention, and their research results have been published in the scientific journal Nature Communications.
Researchers at the University of Twente have developed a hollow copper fibre which can be used to convert CO2 into CO with a very high efficiency. The fibre, which serves as an electrode, is provided with countless minute pores. If the fibre is placed in a bath of water, a voltage potential applied, and CO2 pumped in, the CO2 is converted into CO as it passes out through these pores.
Efficiency and selectivity
The principle is straightforward but the efficiency and selectivity of the reaction are surprisingly high, in part because the electrode provides a huge surface area on which the reaction can take place. An important innovation is the optimized interface between gas, fluid and copper particles, allowing the very efficient supply of CO2 and removal of the product, CO. Conversion takes place at about ten times the rate when using the most advanced copper electrodes currently available, while the selectivity (expressed as the percentage of electrons that actually convert CO2 into CO) is 85%, compared to 35% in current copper electrodes. The newly developed electrode also performs better than electrodes made of expensive precious metals such as gold or silver.
Manufacturing process
The fibres are manufactured in the following way. Small copper particles are added to a polymer solution. This solution is guided through a small, ring-shaped slit in a water bath, in which the polymer solution solidifies into the form of a thin hollow fibre. A thermal treatment is then employed to remove the polymer and partially fuse the copper particles. The result is a copper oxide fibre. Reacting this with hydrogen at a high temperature yields the final product: a hollow, porous copper fibre with a diameter of 1.5mm and a wall thickness of 0.1mm.
Because this manufacturing technique is based on the way polymeric hollow-fibre membranes are currently constructed on a very large scale, e.g. for kidney dialysis equipment, the researchers involved believe it will be relatively easy to produce the new electrode on a commercial scale.
Page 1 of 2
Suggested Items
Copper Price Surge Raises Alarms for Electronics
07/15/2025 | Global Electronics Association Advocacy and Government Relations TeamThe copper market is experiencing major turbulence in the wake of U.S. President Donald Trump’s announcement of a 50% tariff on imported copper effective Aug. 1. Recent news reports, including from the New York Times, sent U.S. copper futures soaring to record highs, climbing nearly 13% in a single day as manufacturers braced for supply shocks and surging costs.
I-Connect007 Editor’s Choice: Five Must-Reads for the Week
07/11/2025 | Andy Shaughnessy, Design007 MagazineThis week, we have quite a variety of news items and articles for you. News continues to stream out of Washington, D.C., with tariffs rearing their controversial head again. Because these tariffs are targeted at overseas copper manufacturers, this news has a direct effect on our industry.I-Connect007 Editor’s Choice: Five Must-Reads for the Week
Digital Twin Concept in Copper Electroplating Process Performance
07/11/2025 | Aga Franczak, Robrecht Belis, Elsyca N.V.PCB manufacturing involves transforming a design into a physical board while meeting specific requirements. Understanding these design specifications is crucial, as they directly impact the PCB's fabrication process, performance, and yield rate. One key design specification is copper thieving—the addition of “dummy” pads across the surface that are plated along with the features designed on the outer layers. The purpose of the process is to provide a uniform distribution of copper across the outer layers to make the plating current density and plating in the holes more uniform.
Trump Copper Tariffs Spark Concern
07/10/2025 | I-Connect007 Editorial TeamPresident Donald Trump stated on July 8 that he plans to impose a 50% tariff on copper imports, sparking concern in a global industry whose output is critical to electric vehicles, military hardware, semiconductors, and a wide range of consumer goods. According to Yahoo Finance, copper futures climbed over 2% following tariff confirmation.
Happy’s Tech Talk #40: Factors in PTH Reliability—Hole Voids
07/09/2025 | Happy Holden -- Column: Happy’s Tech TalkWhen we consider via reliability, the major contributing factors are typically processing deviations. These can be subtle and not always visible. One particularly insightful column was by Mike Carano, “Causes of Plating Voids, Pre-electroless Copper,” where he outlined some of the possible causes of hole defects for both plated through-hole (PTH) and blind vias.