-
- News
- Books
Featured Books
- pcb007 Magazine
Latest Issues
Current IssueInventing the Future with SEL
Two years after launching its state-of-the-art PCB facility, SEL shares lessons in vision, execution, and innovation, plus insights from industry icons and technology leaders shaping the future of PCB fabrication.
Sales: From Pitch to PO
From the first cold call to finally receiving that first purchase order, the July PCB007 Magazine breaks down some critical parts of the sales stack. To up your sales game, read on!
The Hole Truth: Via Integrity in an HDI World
From the drilled hole to registration across multiple sequential lamination cycles, to the quality of your copper plating, via reliability in an HDI world is becoming an ever-greater challenge. This month we look at “The Hole Truth,” from creating the “perfect” via to how you can assure via quality and reliability, the first time, every time.
- Articles
- Columns
- Links
- Media kit
||| MENU - pcb007 Magazine
Estimated reading time: 9 minutes
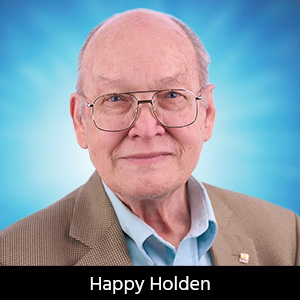
Contact Columnist Form
Design of Experiments
Design of experiments (DOE) is one of the most powerful and influential engineering tools for product yield improvements, new products or processes development, or for problem solving. As mentioned in my last column, process problems led me to a career in printed circuits, and quickly solving those problems led me to a bonus stock award and a great life. Even though I knew nothing about printed circuit manufacturing processes, I was able to quickly find the root causes of all the problems and fix them. My secret? Total quality control (TQC), statistics, and DOE.
Experimentation is the manipulation of controllable factors at different values to see their effect on some desired result. An engineer can use three methods of experimentation:
- Trial and error
- One factor at a time
- Design of experiments
Trial and Error
Hopefully a trained engineer will not use this technique. But in the rush to fix the problem, one might think they know the true root cause and start changing parameters. In my case, I didn’t know the parameters so first I talked to the other engineers, line-workers and supervisors and created a pareto of possible causes. Then I called the chemical suppliers and asked them what they thought was important. Lastly, I went to the industry bible, the Printed Circuit Handbook by Clyde Coombs, and read what it had to say. From this list I got an inkling of what the possible causes could be.
One Factor at a Time
The objective of any experiment is to establish a probable cause-and-effect relationship. The common sense approach is to make trial changes of the most likely factors contributing to the observed problem, keeping all other contributor variables constant during the experiment, and then seeing if a significant correlation can be established between the suspected cause and the effect. If the experiment with the factor chosen gives no conclusive results, the next most likely factor is tried in the same way. Although this experimental strategy sounds logical, as you can see in Figure 1, it tests only a part of the process matrix and only what you know (variables X1, X2 and X3 and changing one at a time from -1 to +1 levels). Four steps are involved in this process:
- Observation: Study all phases of the situation in which the effect to be controlled occurs.
- Reflection: Try to think of all the causes which might influence this effect. Consult with others who have had experience with this or similar situations.
- Trial: Try the influence of the most likely factor; if not successful, try the next most likely one, and so on.
- Check: With a purported relationship established, attempt to turn the effect on and off, like a water faucet, by varying the suspected cause back and forth between its different levels.
The common sense approach is always recommended as a first try. It is fast and cheap when it works— as it often does for confirming single or independent factors whose presence can be logically suspected. However, when it has been tried several times on a problem with no clear cut solution emerging, a more sophisticated approach is called for—that of statistical experimentation.
This was the situation when asked to help the printed circuit plant. Months of tests and experimentation had not resulted in finding a cause for the problems and the solution.
Figure 1: Experimental methods: Can be trial and error or factorial design of experiments (DOE) that is much more comprehensive and effective than one-factor-at-a-time method. The DOE software can be found in The NIST/SEMETECH e-Handbook of Statistical Methods[1].
Page 1 of 5
More Columns from Happy’s Tech Talk
Happy’s Tech Talk #42: Applying Density Equations to UHDI DesignHappy’s Tech Talk #41: Sustainability and Circularity for Electronics Manufacturing
Happy’s Tech Talk #40: Factors in PTH Reliability—Hole Voids
Happy’s Tech Talk #39: PCBs Replace Motor Windings
Happy’s Tech Talk #38: Novel Metallization for UHDI
Happy’s Tech Talk #37: New Ultra HDI Materials
Happy’s Tech Talk #36: The LEGO Principle of Optical Assembly
Happy’s Tech Talk #35: Yields March to Design Rules