-
- News
- Books
Featured Books
- pcb007 Magazine
Latest Issues
Current IssueInventing the Future with SEL
Two years after launching its state-of-the-art PCB facility, SEL shares lessons in vision, execution, and innovation, plus insights from industry icons and technology leaders shaping the future of PCB fabrication.
Sales: From Pitch to PO
From the first cold call to finally receiving that first purchase order, the July PCB007 Magazine breaks down some critical parts of the sales stack. To up your sales game, read on!
The Hole Truth: Via Integrity in an HDI World
From the drilled hole to registration across multiple sequential lamination cycles, to the quality of your copper plating, via reliability in an HDI world is becoming an ever-greater challenge. This month we look at “The Hole Truth,” from creating the “perfect” via to how you can assure via quality and reliability, the first time, every time.
- Articles
- Columns
- Links
- Media kit
||| MENU - pcb007 Magazine
Estimated reading time: 9 minutes
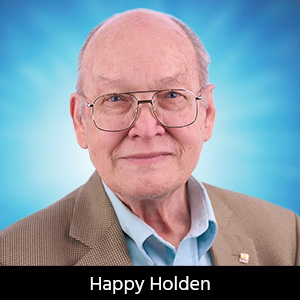
Contact Columnist Form
Design of Experiments
Design of ExperimentsI guess I was lucky to be exposed to engineering statistics early in my college education. I never took a statistics course from the math department; if I had I might have thought it to be boring. Instead, it came as part of the chemical engineering basics. Since there is no “higher math” in most statistics, it is a good introductory course for engineers and essential to analyze lab and experimental results that will be part of the science and engineering education. My first design of experiment was done by long-hand; then, we did it by punched cards, and finally, with our slide rules (guess that dates me!). It wasn’t until the HP PCB problem solving that I wrote a basic program to conduct my DOEs on an HP 2116 computer.
Critical to DOE was the type of variables. In production, qualitative factors can be more significant than quantitative factors. Important quantitative factors (variables) are usually controlled, but qualitative variables can change without notice. Qualitative factors include: time of the year, day of the week, production shifts, production line, individual workers or machines, supplier sources, maintenance frequency, and even source of water. If you remember in my second column, and Figure 6 contained therein, for DOE with “factors not all being quantitative,” “screening experiments” are called for, such as described by Plackett-Berman[1] and in Fractional Factorial[2] (center boxes in Figure 1). Other application areas are comparative, modeling and optimizing.
Screening experiments (also called fractional factorial) are test plan used for an initial scan of problems having a large number—usually six or more—of presumed independent variables. The purpose of such plans is to determine which variables have the largest effects on the dependent variables. Results show only main or first-order effects (interactions), only the sensitivity of Y to a significant change in X1, X2 or X3, etc. Generally, interaction and second-order effects are not detected in screening plans.
Once the independent variables have been reduced to four or less, full factorial experiments can be conducted to understand all interactions and if the responses are non-linear and linear equations can be developed. Further experimentation can be conducted as ‘evolutionary operations’ to discover optimum settings and performances.
In the HP PCB problems, indeed the causes of the problems were an interaction of Monday vs. Friday, Day Shift vs. Graveyard Shift, process tank #1 vs. #4, and chemical supplier source. It was the qualitative variables that were at the Root Cause! A “one-at-a-time” experimentation couldn’t duplicate the root cause.
Some Examples
The next three figures show four different PCB process DOE results. The first, in Figure 2, is an experiment to minimize shifting of innerlayers during multilayer lamination. The variable and levels were a full factorial design of three variables at two levels:
1. Vented panel borders: with venting and without venting
2. Tooling methods for layup: ¼-inch holes and four 1/8-inch slots-centerline
3. Lamination pressure: 294 PSI & 344 PSI
The results are the image shift in microns. The lowest shift was 76 μm using vented borders, ¼-inch peripheral holes and the higher pressure. Analysis shows that the tooling method has the most positive effect on shifting and interacts with panel venting (V).
Page 2 of 5
More Columns from Happy’s Tech Talk
Happy’s Tech Talk #42: Applying Density Equations to UHDI DesignHappy’s Tech Talk #41: Sustainability and Circularity for Electronics Manufacturing
Happy’s Tech Talk #40: Factors in PTH Reliability—Hole Voids
Happy’s Tech Talk #39: PCBs Replace Motor Windings
Happy’s Tech Talk #38: Novel Metallization for UHDI
Happy’s Tech Talk #37: New Ultra HDI Materials
Happy’s Tech Talk #36: The LEGO Principle of Optical Assembly
Happy’s Tech Talk #35: Yields March to Design Rules