-
- News
- Books
Featured Books
- pcb007 Magazine
Latest Issues
Current IssueInventing the Future with SEL
Two years after launching its state-of-the-art PCB facility, SEL shares lessons in vision, execution, and innovation, plus insights from industry icons and technology leaders shaping the future of PCB fabrication.
Sales: From Pitch to PO
From the first cold call to finally receiving that first purchase order, the July PCB007 Magazine breaks down some critical parts of the sales stack. To up your sales game, read on!
The Hole Truth: Via Integrity in an HDI World
From the drilled hole to registration across multiple sequential lamination cycles, to the quality of your copper plating, via reliability in an HDI world is becoming an ever-greater challenge. This month we look at “The Hole Truth,” from creating the “perfect” via to how you can assure via quality and reliability, the first time, every time.
- Articles
- Columns
- Links
- Media kit
||| MENU - pcb007 Magazine
Estimated reading time: 3 minutes
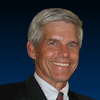
All About Flex: Using Aluminum in Flexible Circuits
While copper is the most widely used metal in flexible circuits, it is not the only metal that can be used. One such metal foil is aluminum. Aluminum is lower cost as a raw material and a lower weight alternative to copper. Aluminum is close in conductivity and current carrying capability to copper; it is very pliable which gives it excellent flexibility. In addition, aluminum is generally less corrosive and aluminum oxide tends to become a protective layer in many environments. The cost of aluminum has traditionally been considerably less than copper although processing costs and infrastructure tend to make finished circuit costs more comparable. In addition, aluminum foil is available in a wide range of thicknesses.
So why isn’t aluminum used in all flexible circuit applications? The answers become apparent when we take a closer look at the properties of aluminum.
Galvanic Corrosion
Galvanic corrosion occurs when two dissimilar metals are in contact with the presence of moisture. The rate or severity of galvanic action depends on the relative difference in passivity (or activity) between the two metals. Metals are rated based on relative potential differences as shown in the graph below:
Figure 1: Relative potential differences of metals. (Source: L-36.com)
The corrosion activity is related to the relative galvanic difference of the two metals. In other words, if a very passive (noble) metal is in contact with a very active metal then corrosion will be significant. Conversely, metals with very similar galvanic ratings will be less likely to experience galvanic corrosion. The general rule of thumb is that if two metals are within 0.1 volts on the galvanic scale, there should be few corrosion issues.
Aluminum by itself has fewer corrosion issues than copper, since aluminum oxide is not only protective, but highly conductive. However, aluminum is one of the more active metals and should not come in contact with many of the typical metals widely used in electronics (i.e., gold, graphite, silver, copper and nickel). So one of the immediate drawbacks of aluminum is the limitations on what metals it can contact. For example, gold-, nickel- or silver-plated connectors could be highly problematic.
Plating/ Soldering
The issues with galvanic action described above also become issues for plating or soldering. Common plating and soldering materials in electronics such as nickel, gold, tin, lead, palladium and silver would not be compatible with aluminum. So component attachment using soldering is not viable with aluminum. It is possible to use some conductive epoxies for component attachment, but the limitations of epoxy attachment will rule out the use of aluminum in many electronic packaging applications.
Double-sided and multilayer circuits typically need an electrical connection between the layers. For copper circuits, electroplating additional copper is used as a through-hole connection method. Electroplating would not work well with aluminum. It is possible to connect multiple aluminum layers by using mechanical crimps, but this method has density limitations and would not be viable for most two-layer or multilayer requirements.
Etching
Common etching chemistry that works extremely well for copper will not work for aluminum. Ferric acid etching chemistry is typically used for aluminum. Many flexible circuit manufacturers do not have ferric acid process capability. Even with proper chemistry, the etching process with aluminum cannot be controlled as precisely with copper, so there are significant limitations on circuit trace density. Many manufacturers use a stamping process to create aluminum traces, but again this process is not practical for high-density flex circuit applications.
Chemical Resistance
It is not necessarily accurate to suggest that copper has superior chemical resistance properties vs. aluminum; but aluminum certainly performs differently. Aluminum has better resistance to oxidizing acids when compared to copper. Other chemicals such as hydrochloric acid will rapidly dissolve aluminum and have very little effect on copper. In general, it should not be assumed that environments that copper circuits survive in will be safe for aluminum. Substituting an aluminum circuit for a copper one should be thoroughly tested.
Summary
Aluminum circuitry can be a cost-effective, lighter weight alternative to its copper cousin, but there are significant limitations to consider. Aluminum would be a poor choice for applications requiring component assembly, multilayer configuration or high density. Long term compatibility with the application environment and possibilities of metal corrosion should be properly considered when this metal becomes a circuitry candidate. The supply infrastructure is more limited when aluminum becomes the foil of choice.
Dave Becker is the V.P. of sales and marketing at All Flex Flexible Circuits and Heaters. To contact Becker, or read past columns, click here.
More Columns from All About Flex
All About Flex: Terms and ConditionsAll About Flex: ISO 9001 Basics
All About Flex: FAQs on UL Listings for Flexible Circuits
All About Flex: Avoiding Trace Fracturing in a Flexible Circuit
Polyimide vs. Silicone for Flexible Heaters
All About Flex: Copper Thickness Requirements for Flex Circuits
All About Flex: Copper Grain Direction
All About Flex: Options for Purchasing Flexible Heaters