All About Flex: Why Copper is Ideal for Flexible Circuitry
April 13, 2016 | Dave Becker, All FlexEstimated reading time: 3 minutes
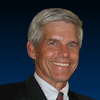
While copper may not rank the best in any one of the above criteria, it probably has the best overall rating.
Electrical Conductivity
The following chart[1] ranks the common metals by conductivity:
Copper is the second-most conductive metal (in pure form). The copper used on flexible circuits can be formed by a number of methods such as electro-deposition (ED), rolling/annealing, or a combination of the two. The conductivity of copper by volume on a flexible circuit is not exactly the same as pure copper, but it is quite close.
Thermal Conductivity
Thermal conductivity is highly related to electrical conductivity. Thermal conducting properties are very important for a number of applications, particularly when heat dissipation is critical.
As can be seen from the chart above[2], copper is an excellent thermal conductor, relative to the other common metals.
Cost
Copper is one of the lowest cost metals that are viable for electronic applications. The following chart below shows typical costs by weight, and more importantly by volume.
Spot prices of metal costs can vary significantly from day to day. The costs above are based on one snapshot in time, but one can see that the relative differences are significant. The costs shown are based on spot prices and do not include the costs for processing the metals for electronic fabrication. Aluminum is very inexpensive relative to other metals, but copper is significantly cheaper than gold or silver.
Availability
Availability or abundance of supply tends to be inversely proportional to the cost. Copper is considered plentiful and is stated to have a 40-year supply based on reserves and 200 years based on resources. The difference between reserve and resource is: Reserves are based on viable deposits that have been discovered and are either being mined or are deemed profitable to mine; Resources are based on potentially profitable discovered deposits and undiscovered deposits predicted by geological surveys[3].
Corrosion Resistance
Corrosion resistance in any environment depends on the chemical exposure. The following chart[4] rates common metals by activity, which is an indicator of the likelihood of corrosion in the presence of moisture and ionic contamination.
Copper is in the middle of the pack on the galvanic scale and is often treated, coated or plated to dramatically retard corrosion.
Flexibility
An indicator of flexibility is the Young’s Modulus of Elasticity. This measurement relates to the amount of force it takes to change the elongation direction. The lower the number, the easier it will “stretch.” The chart below shows the Modulus numbers of the more common metals.
It is important to note that the flexibility of copper substrates used in circuit fabrication is highly related to the processing method used to create the foil. Rolled annealed copper goes through a series of rolling steps that elongates the grain, giving it a higher degree of flexibility. Even ED copper, which forms metal foil by electroplating copper onto a rotating stainless steel drum, is quite flexible and suitable for many flex-to-install applications. But the overwhelming favorite copper for flexible circuitry is rolled annealed. It is comparable in cost and offers the insurance of being the most robust with flexibility.
Another critical consideration is ease of processing. Copper is incredibly versatile and works well with a diverse set of circuit fabrication steps including electroplating, immersion and electroless plating, etching and soldering. While many of these processes have been designed around copper, this metal has remained the stand-alone workhorse for more than 50 years of printed circuit board processing.
References
1. www.metaldetectingworld.com.
2. www.tibtech.com
3. copperalliance.org
4. inspectapedia.com
Dave Becker is vice president of sales and marketing at All Flex Flexible Circuits LLC.
Testimonial
"The I-Connect007 team is outstanding—kind, responsive, and a true marketing partner. Their design team created fresh, eye-catching ads, and their editorial support polished our content to let our brand shine. Thank you all! "
Sweeney Ng - CEE PCBSuggested Items
How Good Design Enables Sustainable PCBs
08/21/2025 | Gerry Partida, Summit InterconnectSustainability has become a key focus for PCB companies seeking to reduce waste, conserve energy, and optimize resources. While many discussions on sustainability center around materials or energy-efficient processes, PCB design is an often overlooked factor that lies at the heart of manufacturing. Good design practices, especially those based on established IPC standards, play a central role in enabling sustainable PCB production. By ensuring designs are manufacturable and reliable, engineers can significantly reduce the environmental impact of their products.
50% Copper Tariffs, 100% Chip Uncertainty, and a Truce
08/19/2025 | Andy Shaughnessy, I-Connect007If you’re like me, tariffs were not on your radar screen until a few months ago, but now political rhetoric has turned to presidential action. Tariffs are front-page news with major developments coming directly from the Oval Office. These are not typical times. President Donald Trump campaigned on tariff reform, and he’s now busy revamping America’s tariff policy.
Global PCB Connections: Understanding the General Fabrication Process—A Designer’s Hidden Advantage
08/14/2025 | Markus Voeltz -- Column: Global PCB ConnectionsDesigners don’t need to become fabricators, but understanding the basics of PCB fabrication can save you time, money, and frustration. The more you understand what’s happening on the shop floor, the better you’ll be able to prevent downstream issues. As you move into more advanced designs like HDI, flex circuits, stacked vias, and embedded components, this foundational knowledge becomes even more critical. Remember: the fabricator is your partner.
MKS’ Atotech to Participate in IPCA Electronics Expo 2025
08/11/2025 | AtotechMKS Inc., a global provider of enabling technologies that transform our world, announced that its strategic brands ESI® (laser systems) and Atotech® (process chemicals, equipment, software, and services) will showcase their latest range of leading manufacturing solutions for printed circuit board (PCB) and package substrate manufacturing at the upcoming 17th IPCA Show to be held at Pragati Maidan, New Delhi from August 21-23, 2025.
MKS Showcases Next-generation PCB Manufacturing Solutions at the Thailand Electronics Circuit Asia 2025
08/06/2025 | MKS Instruments, Inc.MKS Inc, a global provider of enabling technologies that transform our world, today announced its participation in Thailand Electronics Circuit Asia 2025 (THECA 2025), taking place August 20–22 at BITEC in Bangkok.